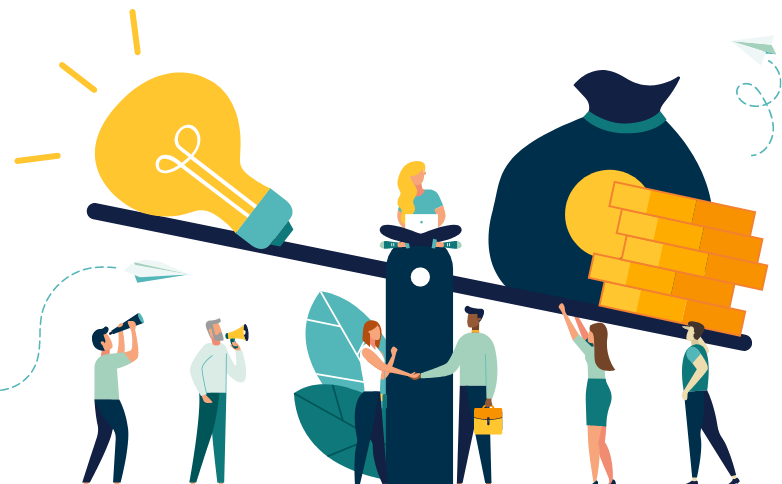
Advanced manufacturing refers specifically to the use innovative technology to improve processes and products. You can classify the technology used to achieve these results as "advanced", “innovative" or "cutting-edge". This is because advanced manufacturing has become more common in the manufacturing industry. Below are examples of advanced production. Here are some of the most commonly used technologies in advanced production.
Continuous manufacturing
The earliest description of continuous manufacturing dates back to the 1700s when it was used to make pig iron in blast furnaces. The concept has since spread across various industries, including the automotive, food, oil and refining, chemicals, and pulp and paper industries. Today, continuous manufacturing has gained considerable traction in the biopharmaceutical industry, capturing the attention of leading CMOs and big pharma players.
In a recent commentary, the FDA and its partners discussed the benefits of using continuous manufacturing to produce therapeutic proteins. This legislation would establish national centers to help companies develop standards and advance the field. This legislation is intended to improve the creation and use of medical products. Further, it would also encourage companies to use continuous manufacturing to develop and improve products. But, it is crucial to ensure that continuous production processes are safe.
Automated processes
The benefits of automating processes in advanced manufacturing cannot be overstated. Automation is often the best way to maximize floor space and increase production efficiency. Manufacturers can cut costs and improve productivity by leveraging automation technology and collecting data. Automation of the process industry can also help save time and money. Although initial investments can be costly, automation will eventually improve a company's bottom line.
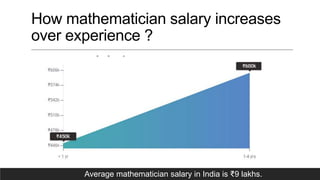
Companies today combine advanced manufacturing processes with automated processes. Audi, for example, uses automated welding and bonding to reduce production times and save energy and weight. They also use advanced manufacturing techniques such as regenerative-braking conveyor systems. 3D printing, which is a major advancement in manufacturing, has only recently been adopted by mainstream companies. But what makes it so attractive to manufacturers?
Internet of Things
Manufacturing is being transformed by the IIoT revolution. This revolution uses sensors to monitor machinery and processes. These sensors collect data from all parts of the manufacturing process and send it to a central base station. This data can then be analyzed to help optimize processes and eliminate waste. Advanced manufacturers already utilize IIoT sensors to monitor their processes and optimize production. The IIoT is an industrial version of key fobs.
IIoT deployment will require a clear roadmap and sufficient development capabilities to enable the rollout of use cases in an efficient and scalable manner. An automaker has provided the following roadmap:
Cost-effectiveness
Costs of advanced manufacturing may not be directly comparable to traditional production systems. Rather, the traditional cost-benefit analysis is an insufficient basis for evaluating economic benefits. However, a holistic model that considers both costs and benefits of technology can help to identify new benefits and accelerate decision-making processes. Munker and Schroer develop a cost-benefit tool to address the main issues involved in AMS implementation.
Advances in information technology are rapidly changing the face of manufacturing and their costs. Information technology is making production systems more interconnected and intelligent. The cost pressure is increasing, putting more emphasis on productivity and company's ability respond to customer demands. The adoption of advanced manufacturing technologies is likely to accelerate the implementation and cost effectiveness of new technologies. As the industry digitizes, this will likely lead to a rapid adoption of such technologies.
Human error reduction
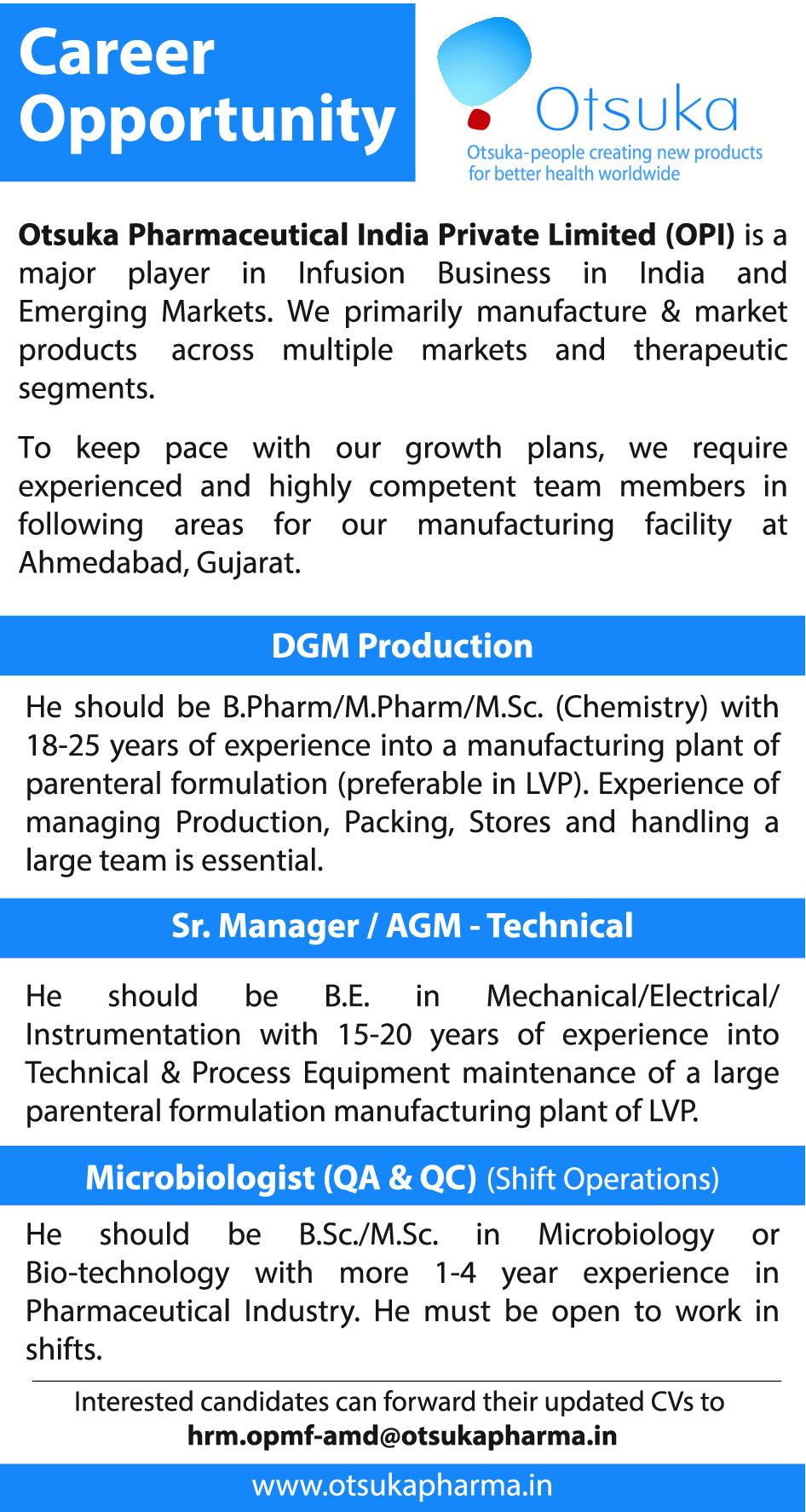
While humans make mistakes, the process they use to produce a product is usually designed to protect it. Human error can occur when employees fail to follow the written process or misunderstand instructions. For example, pharmaceutical labs must follow strict guidelines when they make drugs. Some employees believe they are familiar with a process and know how to use the correct ingredients. They then proceed to make the compound without consulting the written instructions.
Another way to reduce human error is through effective communication between junior and senior employees. Employers who are treated harshly will make mistakes. Therefore, managers should avoid punishing employees who ask questions. Employees should feel at ease asking questions. If they don't feel comfortable asking questions they won't be inclined to take corrective action. Respect senior employees' opinions and communicate with them in a friendly and professional manner.
FAQ
Are there any Manufacturing Processes that we should know before we can learn about Logistics?
No. You don't have to know about manufacturing processes before learning about logistics. Knowing about manufacturing processes will help you understand how logistics works.
What skills should a production planner have?
Being a production planner is not easy. You need to be organized and flexible. Also, you must be able and willing to communicate with clients and coworkers.
What does it take to run a logistics business?
It takes a lot of skills and knowledge to run a successful logistics business. Good communication skills are essential to effectively communicate with your suppliers and clients. You will need to know how to interpret data and draw conclusions. You will need to be able handle pressure well and work in stressful situations. To improve efficiency, you must be innovative and creative. Strong leadership qualities are essential to motivate your team and help them achieve their organizational goals.
You should also be organized and efficient to meet tight deadlines.
What is the difference between a production planner and a project manager?
The primary difference between a producer planner and a manager of a project is that the manager usually plans and organizes the whole project, while a production planner is only involved in the planning stage.
What is the distinction between Production Planning or Scheduling?
Production Planning (PP) refers to the process of determining how much production is needed at any given moment. Forecasting and identifying production capacity are two key elements to this process.
Scheduling is the process of assigning specific dates to tasks so they can be completed within the specified timeframe.
How can manufacturing excess production be decreased?
It is essential to find better ways to manage inventory to reduce overproduction. This would reduce the amount of time spent on unnecessary activities such as purchasing, storing, and maintaining excess stock. This could help us free up our time for other productive tasks.
A Kanban system is one way to achieve this. A Kanbanboard is a visual tool that allows you to keep track of the work being done. Work items are moved through various states to reach their destination in a Kanban system. Each state represents an individual priority level.
If work is moving from one stage to the other, then the current task can be completed and moved on to the next. However, if a task is still at the beginning stages, it will remain so until it reaches the end of the process.
This helps to keep work moving forward while ensuring that no work is left behind. With a Kanban board, managers can see exactly how much work is being done at any given moment. This allows them to adjust their workflows based on real-time information.
Lean manufacturing, another method to control inventory levels, is also an option. Lean manufacturing works to eliminate waste throughout every stage of the production chain. Any product that isn't adding value can be considered waste. The following are examples of common waste types:
-
Overproduction
-
Inventory
-
Unnecessary packaging
-
Overstock materials
These ideas will help manufacturers increase efficiency and lower costs.
Statistics
- According to the United Nations Industrial Development Organization (UNIDO), China is the top manufacturer worldwide by 2019 output, producing 28.7% of the total global manufacturing output, followed by the United States, Japan, Germany, and India.[52][53] (en.wikipedia.org)
- Many factories witnessed a 30% increase in output due to the shift to electric motors. (en.wikipedia.org)
- You can multiply the result by 100 to get the total percent of monthly overhead. (investopedia.com)
- In the United States, for example, manufacturing makes up 15% of the economic output. (twi-global.com)
- In 2021, an estimated 12.1 million Americans work in the manufacturing sector.6 (investopedia.com)
External Links
How To
How to Use Lean Manufacturing for the Production of Goods
Lean manufacturing is an approach to management that aims for efficiency and waste reduction. It was first developed in Japan in the 1970s/80s by Taiichi Ahno, who was awarded the Toyota Production System (TPS), award from KanjiToyoda, the founder of TPS. Michael L. Watkins published the original book on lean manufacturing, "The Machine That Changed the World," in 1990.
Lean manufacturing, often described as a set and practice of principles, is aimed at improving the quality, speed, cost, and efficiency of products, services, and other activities. It emphasizes eliminating waste and defects throughout the value stream. Lean manufacturing can be described as just-in–time (JIT), total productive maintenance, zero defect (TPM), or even 5S. Lean manufacturing eliminates non-value-added tasks like inspection, rework, waiting.
Lean manufacturing can help companies improve their product quality and reduce costs. Additionally, it helps them achieve their goals more quickly and reduces employee turnover. Lean manufacturing is a great way to manage the entire value chain including customers, suppliers, distributors and retailers as well as employees. Lean manufacturing practices are widespread in many industries. For example, Toyota's philosophy underpins its success in automobiles, electronics, appliances, healthcare, chemical engineering, aerospace, paper, food, etc.
Lean manufacturing is based on five principles:
-
Define value - Find out what your business contributes to society, and what makes it different from other competitors.
-
Reduce Waste - Eliminate any activity that doesn't add value along the supply chain.
-
Create Flow – Ensure that work flows smoothly throughout the process.
-
Standardize & simplify - Make processes consistent and repeatable.
-
Build Relationships- Develop personal relationships with both internal as well as external stakeholders.
Lean manufacturing isn’t new, but it has seen a renewed interest since 2008 due to the global financial crisis. To increase their competitiveness, many businesses have turned to lean manufacturing. According to some economists, lean manufacturing could be a significant factor in the economic recovery.
Lean manufacturing, which has many benefits, is now a standard practice in the automotive industry. These include higher customer satisfaction, lower inventory levels, lower operating expenses, greater productivity, and improved overall safety.
The principles of lean manufacturing can be applied in almost any area of an organization. This is because it ensures efficiency and effectiveness in all stages of the value chain.
There are three main types in lean manufacturing
-
Just-in-Time Manufacturing (JIT): This type of lean manufacturing is commonly referred to as "pull systems." JIT stands for a system where components are assembled on the spot rather than being made in advance. This strategy aims to decrease lead times, increase availability of parts and reduce inventory.
-
Zero Defects Manufacturing (ZDM),: ZDM is a system that ensures no defective units are left the manufacturing facility. Repairing a part that is damaged during assembly should be done, not scrapping. This applies to finished products, which may need minor repairs before they are shipped.
-
Continuous Improvement (CI: Continuous improvement aims to increase the efficiency of operations by constantly identifying and making improvements to reduce or eliminate waste. Continuous improvement refers to continuous improvement of processes as well people and tools.