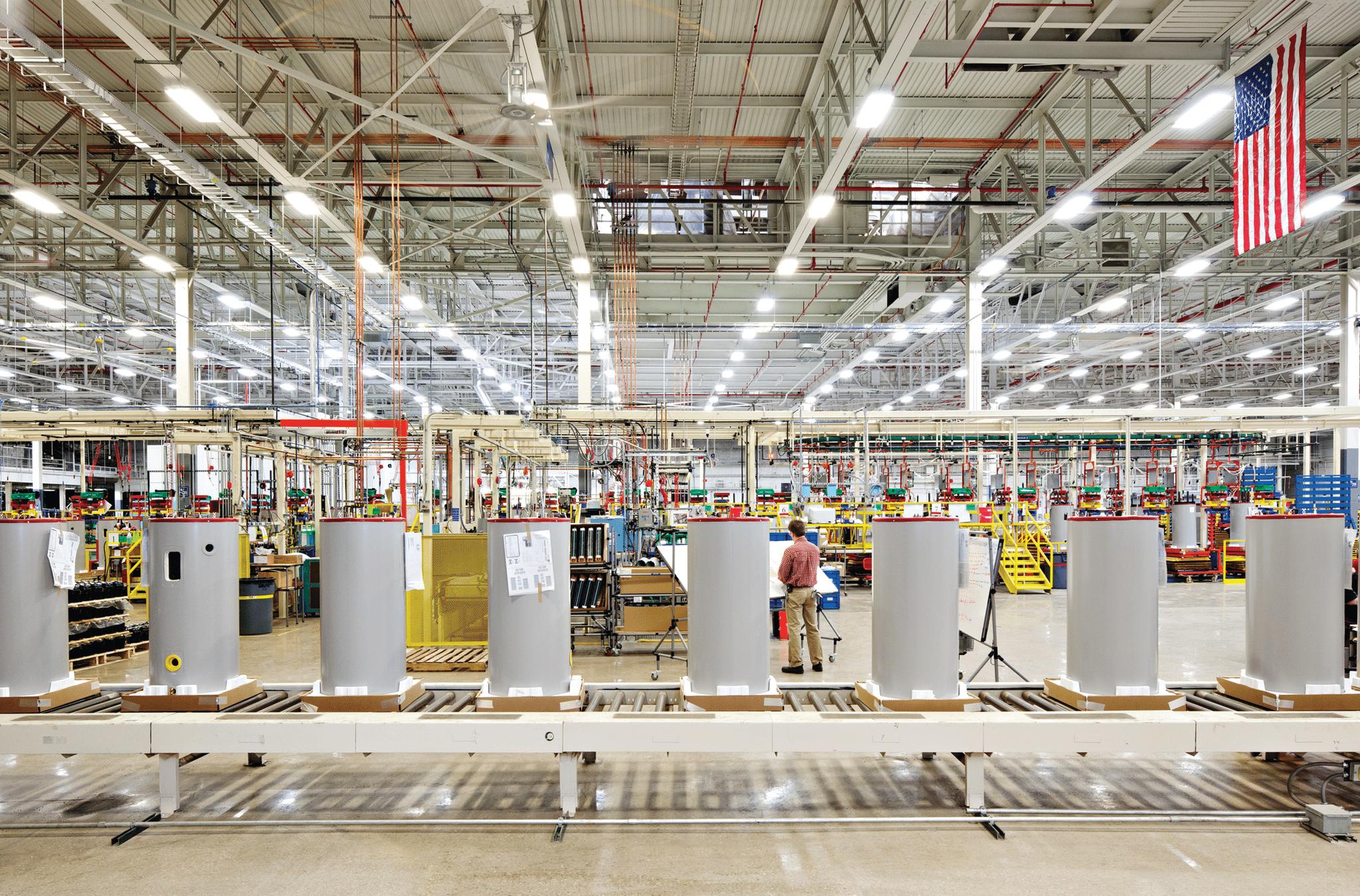
Oracle Supply Chain Management offers a comprehensive solution that enables organizations to respond quickly to changes, build resilient networks, improve forecast accuracy, and adapt quickly in the face of changing circumstances. Oracle SCM gives you complete visibility into the supply chain. This allows for flexible planning and collaboration that minimizes costs. This solution can be used to optimize your business processes, and work more effectively with suppliers using Oracle Fusion Cloud SCM. Oracle SCM helps you achieve these goals. You can also reduce disruptions, lower costs, and improve forecast accuracy.
Friendly interface
Oracle SCM has many improvements that are related to its user-friendly interface. This new release makes Oracle SCM more accessible and user-friendly. A product based analyzer script provides recommendations, solutions, and early warnings. The Oracle Inbound Transactions Analyzer (a great example) is an excellent example. It is designed specifically to identify and resolve inbound transaction issues. It is customizable, too.
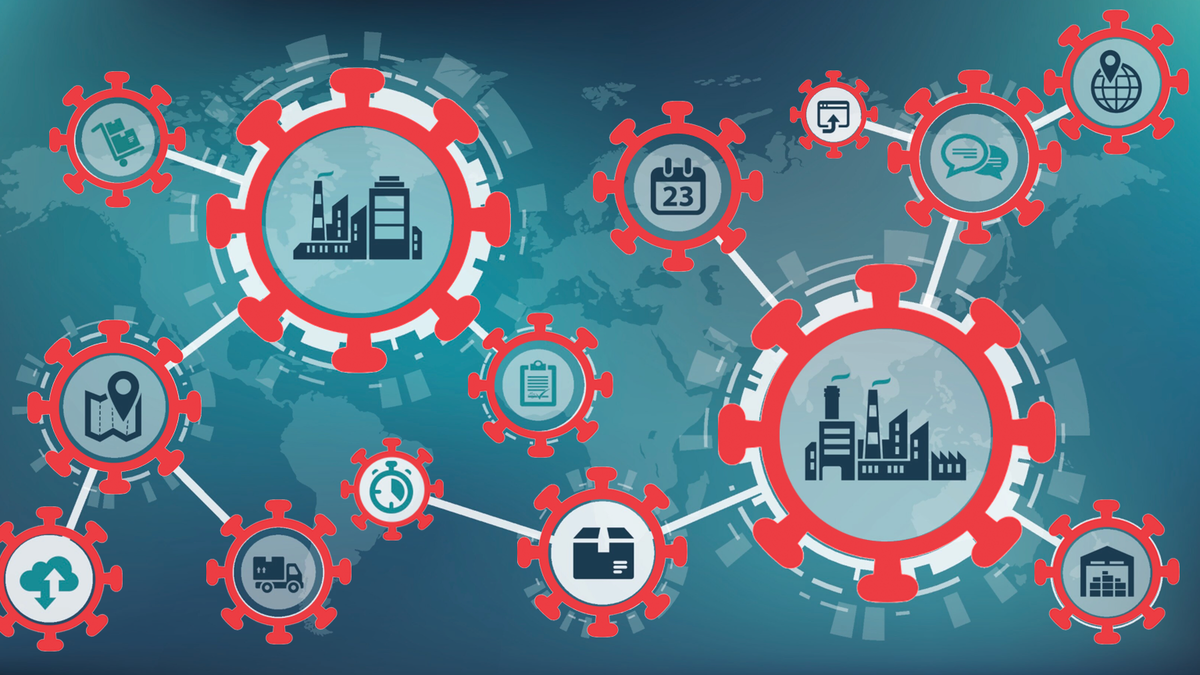
Cost management
With Oracle SCM, cost management policies and decisions can be defined at the item level. Cost profiles can be created by product or manufacturing process, and not just rely on one costing methodology. For instance, manufactured products may use a standard rolled-up cost, while for repair items, the actual costing will be used. The software also supports multiple open and closed periods. The software also has cost simulation and copying capabilities.
Decision support
Oracle SCM decision support is the application of advanced analytics to enhance the management process' performance. The management can decide the best course of action using a variety of business intelligence tools. Oracle Strategic Enterprise Management apps are designed to assist many companies in their strategic management strategies. This technology allows executives manage costs and monitor their progress against an established plan. Employee performance can be measured and compensated. These applications can be integrated with Oracle's ERP systems and used as enterprise-wide solutions.
Regulatory compliance
As regulatory compliance laws and regulations continue to increase, organizations need to find effective ways to manage them. Oracle has the solution. Oracle SCM regulatory compliance solutions allow organizations to more easily meet legal and regulatory compliance needs. Organizations of all sizes can deploy the Oracle Cloud Platform with flexible options. Oracle offers a wide range of customizable and configurable products to help customers comply with regulatory requirements.
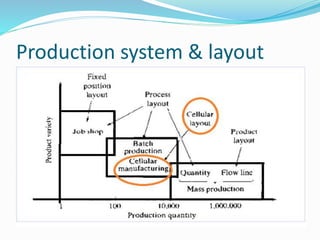
Flexible solution
Intellinum Inc., a world-renowned provider of supply chain mobility services, has created Flexi LogiPro. It is a flexible solution that supports Oracle SCM Cloud and Oracle WMS cloud. The flexible mobile solution offers a barcode enabled, customizable user interface for mobile devices. It connects to the backend system immediately and supports Oracle SCM/WMS Cloud. It is available both for cloud and on-premise deployments. This allows companies to customize mobile apps for their unique needs.
FAQ
What is the difference between Production Planning, Scheduling and Production Planning?
Production Planning (PP), is the process of deciding what production needs to take place at any given time. This is accomplished by forecasting the demand and identifying production resources.
Scheduling refers to the process of allocating specific dates to tasks in order that they can be completed within a specified timeframe.
How does a production planner differ from a project manager?
The major difference between a Production Planner and a Project Manager is that a Project Manager is often the person responsible for organizing and planning the entire project. While a Production Planner is involved mainly in the planning stage,
Are there any Manufacturing Processes that we should know before we can learn about Logistics?
No. No. However, knowing about manufacturing processes will definitely give you a better understanding of how logistics works.
What types of jobs can you find in logistics
There are many jobs available in logistics. These are some of the jobs available in logistics:
-
Warehouse workers - They load and unload trucks and pallets.
-
Transportation drivers: They drive trucks and trailers and deliver goods and make pick-ups.
-
Freight handlers - They sort and pack freight in warehouses.
-
Inventory managers - These are responsible for overseeing the stock of goods in warehouses.
-
Sales representatives - They sell products.
-
Logistics coordinators: They plan and manage logistics operations.
-
Purchasing agents – They buy goods or services necessary to run a company.
-
Customer service agents - They answer phone calls and respond to emails.
-
Shipping clerks: They process shipping requests and issue bills.
-
Order fillers are people who fill orders based only on what was ordered.
-
Quality control inspectors – They inspect incoming and outgoing products to ensure that there are no defects.
-
Others - There is a variety of other jobs in logistics. These include transportation supervisors and cargo specialists.
What are the responsibilities of a logistic manager?
Logistics managers are responsible for ensuring that all goods arrive in perfect condition and on time. This is done through his/her expertise and knowledge about the company's product range. He/she must also ensure sufficient stock to meet the demand.
What are the products of logistics?
Logistics involves the transportation of goods from point A and point B.
They include all aspects associated with transport including packaging, loading transporting, unloading storage, warehousing inventory management customer service, distribution returns and recycling.
Logisticians ensure that the right product reaches the right place at the right time and under safe conditions. They assist companies with their supply chain efficiency through information on demand forecasts. Stock levels, production times, and availability.
They also keep track of shipments in transit, monitor quality standards, perform inventories and order replenishment, coordinate with suppliers and vendors, and provide support services for sales and marketing.
Statistics
- According to the United Nations Industrial Development Organization (UNIDO), China is the top manufacturer worldwide by 2019 output, producing 28.7% of the total global manufacturing output, followed by the United States, Japan, Germany, and India.[52][53] (en.wikipedia.org)
- According to a Statista study, U.S. businesses spent $1.63 trillion on logistics in 2019, moving goods from origin to end user through various supply chain network segments. (netsuite.com)
- You can multiply the result by 100 to get the total percent of monthly overhead. (investopedia.com)
- Job #1 is delivering the ordered product according to specifications: color, size, brand, and quantity. (netsuite.com)
- In the United States, for example, manufacturing makes up 15% of the economic output. (twi-global.com)
External Links
How To
How to use the Just In-Time Production Method
Just-in time (JIT), is a process that reduces costs and increases efficiency in business operations. It's a way to ensure that you get the right resources at just the right time. This means that only what you use is charged to your account. The term was first coined by Frederick Taylor, who developed his theory while working as a foreman in the early 1900s. He saw how overtime was paid to workers for work that was delayed. He decided that workers would be more productive if they had enough time to complete their work before they started to work.
JIT is a way to plan ahead and make sure you don't waste any money. It is important to look at your entire project from beginning to end and ensure that you have enough resources to handle any issues that may arise. If you expect problems to arise, you will be able to provide the necessary equipment and personnel to address them. This will prevent you from spending extra money on unnecessary things.
There are different types of JIT methods:
-
Demand-driven JIT: This is a JIT that allows you to regularly order the parts/materials necessary for your project. This will let you track the amount of material left over after you've used it. This will allow to you estimate the time it will take for more to be produced.
-
Inventory-based: You stock materials in advance to make your projects easier. This allows you to forecast how much you will sell.
-
Project-driven: This approach involves setting aside sufficient funds to cover your project's costs. Once you have an idea of how much material you will need, you can purchase the necessary materials.
-
Resource-based: This is the most common form of JIT. You assign certain resources based off demand. If you have many orders, you will assign more people to manage them. If you don't receive many orders, then you'll assign fewer employees to handle the load.
-
Cost-based: This is similar to resource-based, except that here you're not just concerned about how many people you have but how much each person costs.
-
Price-based: This is very similar to cost-based, except that instead of looking at how much each individual worker costs, you look at the overall price of the company.
-
Material-based is an alternative to cost-based. Instead of looking at the total cost in the company, this method focuses on the average amount of raw materials that you consume.
-
Time-based JIT: This is another variant of resource-based JIT. Instead of focusing on how much each employee costs, you focus on how long it takes to complete the project.
-
Quality-based: This is yet another variation of resource-based JIT. Instead of worrying about the costs of each employee or how long it takes for something to be made, you should think about how quality your product is.
-
Value-based JIT is the newest form of JIT. In this scenario, you're not concerned about how products perform or whether customers expect them to meet their expectations. Instead, your goal is to add value to the market.
-
Stock-based. This method is inventory-based and focuses only on the actual production at any given point. This method is useful when you want to increase production while decreasing inventory.
-
Just-in-time (JIT) planning: This is a combination of JIT and supply chain management. This refers to the scheduling of the delivery of components as soon after they are ordered. This is important as it reduces lead time and increases throughput.