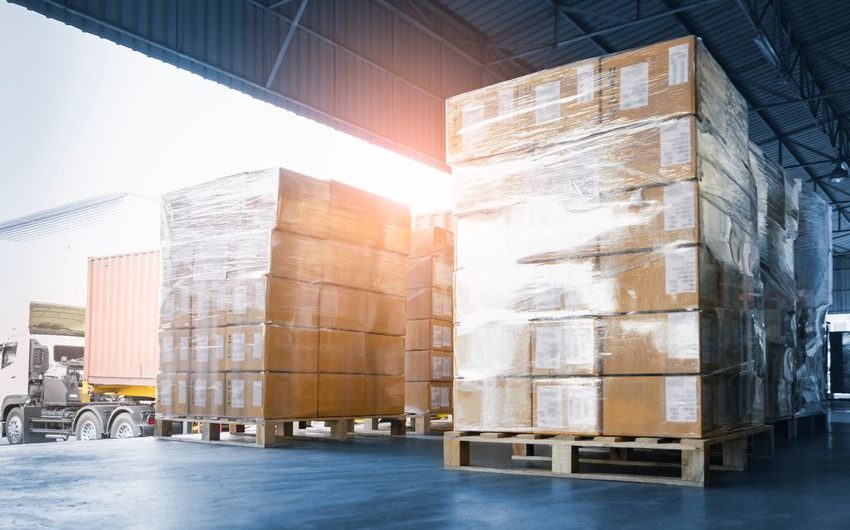
An educational degree in architecture or engineering is usually required to work as an architectural and engineering manager. These professionals are often found working in offices. However, some work on construction sites. They have either a bachelor's or master's degree in engineering or architecture and have extensive field experience. To complement their education, some choose to pursue a graduate degree in business administration. There are many paths to advancement in this profession. Consider a MBA to help you get a job as an architect or engineer manager.
The occupational outlook for engineering and architectural managers
Good prospects exist for engineering and architectural managers. Over the next decade, the number of job openings is expected to grow by about two percent. This will be due to the expansion of different industries. However, there will be fierce competition for jobs. Visit the O*NET Website for more information regarding the career outlook.
The role of engineering managers and architects is to plan and direct activities within an architectural or engineering company. Their knowledge of architecture allows them to plan, design, build, and manage a wide variety of activities. This could include large-scale building design, construction and maintenance, as well as engineering research or site management. They are also responsible in the conceptual design of new products. They must identify the company's technical goals, and then create detailed plans that will assist in achieving them.
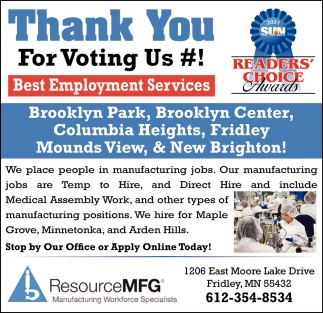
Applicants for this field usually have at least a master's degree in management. The best graduate-level program depends on the type of management position you want. A master's program in engineering can prepare for managerial positions. However, a master's program in business administration will allow you to develop management skills. Both types require at least one academic year to complete.
Education required
Engineering managers and architects need to be educated. These managers oversee the day-today operations of engineering departments. They also supervise and train staff. They also propose budgets for specific tasks and act as mentors for other employees. A bachelor's degree is a good option if you're interested in a career as a mentor for other employees.
Most of these managers have a bachelor’s degree either in architecture or engineering. However, many have advanced degrees or certificates in technology or business administration. A master's degree in engineering management, or technology management, also known as MsEM will provide you with the necessary managerial skills. You will need to have strong communication and analytical skills in addition to technical knowledge.
Architects and engineering managers are responsible for implementing new projects while ensuring that the quality of the end product is high. They consider the environmental impact and the user's needs. They prepare budgets and plans based on technical specifications. To ensure that projects are successfully executed, they supervise engineers.
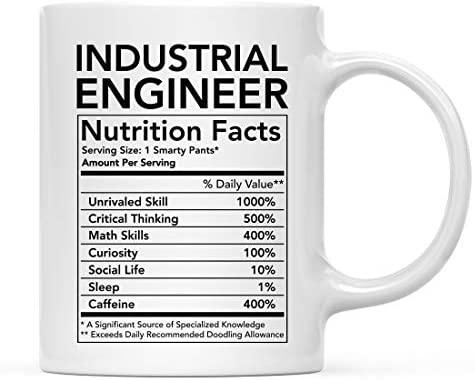
Earning potential
Over the next decade, the earning potential of engineers and architects will increase by 13 percent. This industry is expected to see an increase of jobs. Despite the fact that the number of jobs in this industry is expected to increase, competition will remain intense. However, the industry's growth rate won't be as fast as that of all other occupations.
The salary range for this profession depends on experience, education and geographic location. This field offers an entry-level salary of $75,000. With four to five years experience, you can expect to make $104,800. Meanwhile, those with at least ten years of experience can expect to make around $156,620 per year.
FAQ
How can manufacturing prevent production bottlenecks?
Production bottlenecks can be avoided by ensuring that processes are running smoothly during the entire production process, starting with the receipt of an order and ending when the product ships.
This includes planning for capacity requirements as well as quality control measures.
The best way to do this is to use continuous improvement techniques such as Six Sigma.
Six Sigma management is a system that improves quality and reduces waste within your organization.
It seeks to eliminate variation and create consistency in your work.
How can manufacturing excess production be decreased?
Better inventory management is key to reducing excess production. This would reduce the time spent on unproductive activities like purchasing, storing and maintaining excess stock. We could use these resources to do other productive tasks.
Kanban systems are one way to achieve this. A Kanbanboard is a visual tool that allows you to keep track of the work being done. Kanban systems allow work items to move through different states until they reach their final destination. Each state represents a different priority level.
If work is moving from one stage to the other, then the current task can be completed and moved on to the next. If a task is still in its beginning stages, it will continue to be so until it reaches the end.
This allows work to move forward and ensures that no work is missed. Managers can view the Kanban board to see how much work they have done. This information allows managers to adjust their workflow based off real-time data.
Lean manufacturing is another option to control inventory levels. Lean manufacturing is about eliminating waste from all stages of the production process. Anything that does nothing to add value to a product is waste. Here are some examples of common types.
-
Overproduction
-
Inventory
-
Packaging that is not necessary
-
Materials in excess
These ideas can help manufacturers improve efficiency and reduce costs.
What are the four types of manufacturing?
Manufacturing is the process of transforming raw materials into useful products using machines and processes. Manufacturing involves many activities, including designing, building, testing and packaging, shipping, selling, service, and so on.
Why is logistics so important in manufacturing?
Logistics is an integral part of every business. They enable you to achieve outstanding results by helping manage product flow from raw materials through to finished goods.
Logistics plays a significant role in reducing cost and increasing efficiency.
What skills does a production planner need?
You must be flexible and organized to become a productive production planner. Effective communication with clients and colleagues is essential.
What are the essential elements of running a logistics firm?
To run a successful logistics company, you need a lot knowledge and skills. Effective communication skills are necessary to work with suppliers and clients. You should be able analyse data and draw inferences. You must be able to work well under pressure and handle stressful situations. You need to be innovative and creative to come up with new ways to increase efficiency. Strong leadership qualities are essential to motivate your team and help them achieve their organizational goals.
You must be organized to meet tight deadlines.
Statistics
- Job #1 is delivering the ordered product according to specifications: color, size, brand, and quantity. (netsuite.com)
- According to a Statista study, U.S. businesses spent $1.63 trillion on logistics in 2019, moving goods from origin to end user through various supply chain network segments. (netsuite.com)
- Many factories witnessed a 30% increase in output due to the shift to electric motors. (en.wikipedia.org)
- [54][55] These are the top 50 countries by the total value of manufacturing output in US dollars for its noted year according to World Bank.[56] (en.wikipedia.org)
- It's estimated that 10.8% of the U.S. GDP in 2020 was contributed to manufacturing. (investopedia.com)
External Links
How To
How to use lean manufacturing in the production of goods
Lean manufacturing refers to a method of managing that seeks to improve efficiency and decrease waste. It was created in Japan by Taiichi Ohno during the 1970s and 80s. He received the Toyota Production System award (TPS), from Kanji Toyoda, founder of TPS. Michael L. Watkins published the book "The Machine That Changed the World", which was the first to be published about lean manufacturing.
Lean manufacturing is often defined as a set of principles used to improve the quality, speed, and cost of products and services. It is about eliminating defects and waste from all stages of the value stream. Just-in-time (JIT), zero defect (TPM), and 5S are all examples of lean manufacturing. Lean manufacturing emphasizes reducing non-value-added activities like inspection, rework and waiting.
Lean manufacturing is a way for companies to achieve their goals faster, improve product quality, and lower costs. Lean Manufacturing is one of the most efficient ways to manage the entire value chains, including suppliers and customers as well distributors and retailers. Lean manufacturing practices are widespread in many industries. Toyota's philosophy is the foundation of its success in automotives, electronics and appliances, healthcare, chemical engineers, aerospace, paper and food, among other industries.
Five fundamental principles underlie lean manufacturing.
-
Define Value - Identify the value your business adds to society and what makes you different from competitors.
-
Reduce Waste - Remove any activity which doesn't add value to your supply chain.
-
Create Flow. Ensure that your work is uninterrupted and flows seamlessly.
-
Standardize & simplify - Make processes consistent and repeatable.
-
Build Relationships - Establish personal relationships with both internal and external stakeholders.
Although lean manufacturing isn't a new concept in business, it has gained popularity due to renewed interest in the economy after the 2008 global financial crisis. Many businesses have adopted lean manufacturing techniques to help them become more competitive. Some economists even believe that lean manufacturing can be a key factor in economic recovery.
Lean manufacturing is now becoming a common practice in the automotive industry, with many benefits. These include better customer satisfaction and lower inventory levels. They also result in lower operating costs.
The principles of lean manufacturing can be applied in almost any area of an organization. This is because it ensures efficiency and effectiveness in all stages of the value chain.
There are three main types in lean manufacturing
-
Just-in-Time Manufacturing (JIT): This type of lean manufacturing is commonly referred to as "pull systems." JIT means that components are assembled at the time of use and not manufactured in advance. This approach reduces lead time, increases availability and reduces inventory.
-
Zero Defects Manufacturing - ZDM: ZDM focuses its efforts on making sure that no defective units leave a manufacturing facility. If a part is required to be repaired on the assembly line, it should not be scrapped. This is also true for finished products that require minor repairs before shipping.
-
Continuous Improvement (CI), also known as Continuous Improvement, aims at improving the efficiency of operations through continuous identification and improvement to minimize or eliminate waste. Continuous Improvement involves continuous improvement of processes.