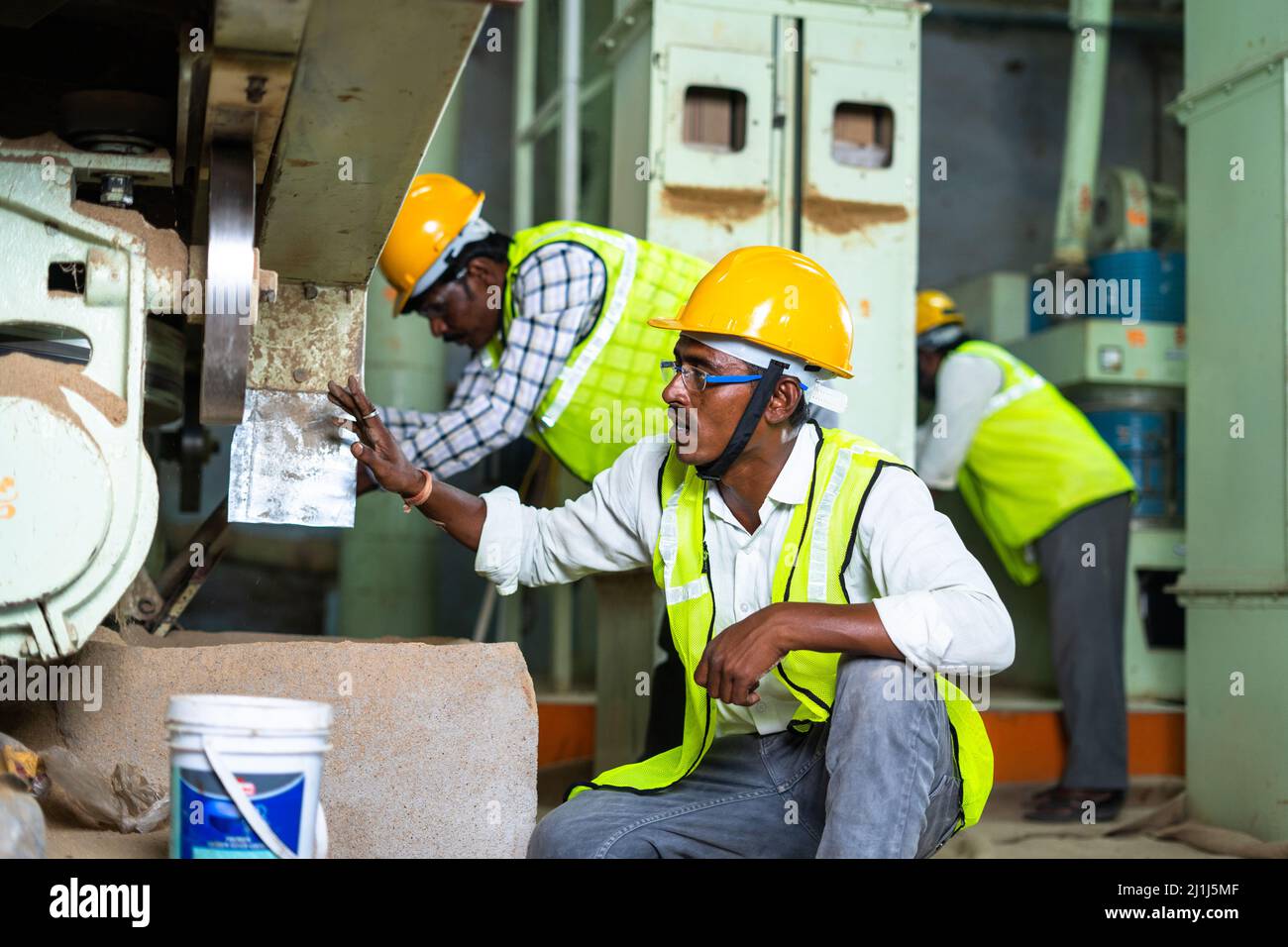
The Internet of Things (IoT), which is transforming the manufacturing industry, makes cybersecurity critical. Companies must protect their assets, customer information, designs, and intellectual property in light of rising cyberattacks. Companies can use the right technology to respond to threats and keep their assets secure. The safety of industrial equipment can be ensured by a physical security system, which includes access cards, cameras, locks, and cameras.
According to Kaspersky Labs, a third of all cybersecurity incidents are targeted at manufacturers. These threats are increasingly complex and widespread. These can include malware, ransomware, and phishing attacks. Manufacturers should protect their intellectual property and designs. A strategy to reduce cyberattacks is also essential.
Cybersecurity for manufacturers is critical for protecting sensitive data and information like customer orders, product specifications, design blueprints, and other details. Cybersecurity plans should include a plan for how to deal with a cyberattack, which can be as costly as $3 million to $6 million. Companies are susceptible to data breaches and theft, as well as disruption of production lines. Many manufacturers struggle to keep up in the face of cyberattacks.
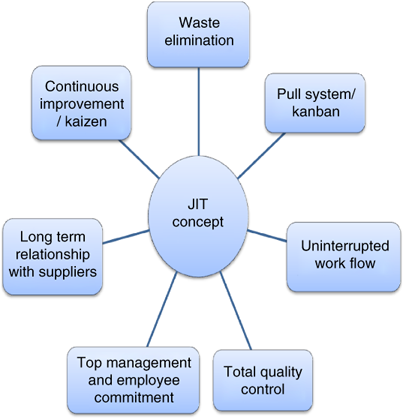
It is essential to invest in cybersecurity for manufacturers. This will help protect customer and employee data, as well as the company's reputation as well as its revenue. A thorough audit of your systems is essential to assess the readiness of your organization and identify any vulnerabilities.
Contact your local Manufacturing Executive Program (MEP), if you are ready to get started. You'll receive expert advice on how to make your business safer from cyberattacks.
You should not only audit your systems, but also set up a backup plan. Regular testing of your system is essential to make sure it functions as intended. By generating hard copies of key documents and creating a process for testing the effectiveness of your system, you can reduce the risk of an attack.
Many manufacturers have not implemented cybersecurity measures, including data standardization. Almost half of OEMs are using outdated or non-compliant hardware, software, and processes. However, more companies are investing in digital tech. Information-related technologies, including networked devices, sensors, cloud computing and networked machines are revolutionizing the industry. The increased globalization of the industry and the Internet of Things (IoT), have raised new concerns. However, a cybersecurity strategy can help ensure your organization is safe.
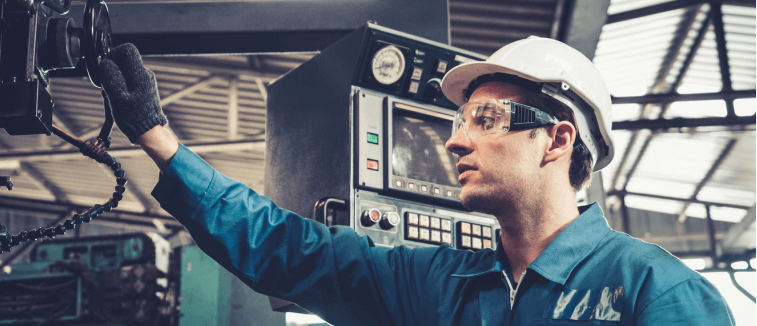
It is crucial to be aware of the diverse requirements for different manufacturing industries when creating a cybersecurity program. Global manufacturers that have long supply chains need to adhere to specific standards depending on where they are located. Manufacturers of small or medium size often have simpler cybersecurity policies. No matter your company size, it is important to have a comprehensive plan in place to protect your business against cyberattacks.
Cybersecurity Framework for Manufacturers by the National Institute of Standards and Technology, (NIST), is a resource designed to help manufacturers protect themselves from cyberattacks. This framework provides a roadmap for managing cybersecurity activities in a variety of sectors, including industrial manufacturing.
FAQ
What skills should a production planner have?
Being a production planner is not easy. You need to be organized and flexible. Also, you must be able and willing to communicate with clients and coworkers.
What are the 7 Rs of logistics?
The acronym 7R's of Logistic is an acronym that stands for seven fundamental principles of logistics management. It was developed by International Association of Business Logisticians (IABL), and published as part of their "Seven Principles of Logistics Management Series" in 2004.
The following letters make up the acronym:
-
Responsible - ensure that all actions taken are within legal requirements and are not harmful to others.
-
Reliable - have confidence in the ability to deliver on commitments made.
-
Reasonable - use resources efficiently and don't waste them.
-
Realistic - consider all aspects of operations, including cost-effectiveness and environmental impact.
-
Respectful - Treat people fairly and equitably
-
Reliable - Find ways to save money and increase your productivity.
-
Recognizable provides value-added products and services to customers
What is the job of a logistics manger?
A logistics manager makes sure that all goods are delivered on-time and in good condition. This is achieved by using their knowledge and experience with the products of the company. He/she must also ensure sufficient stock to meet the demand.
How can manufacturing overproduction be reduced?
Improved inventory management is the key to reducing overproduction. This would reduce the amount of time spent on unnecessary activities such as purchasing, storing, and maintaining excess stock. This will allow us to free up resources for more productive tasks.
A Kanban system is one way to achieve this. A Kanban Board is a visual display that tracks work progress. In a Kanban system, work items move through a sequence of states until they reach their final destination. Each state represents an individual priority level.
To illustrate, work can move from one stage or another when it is complete enough for it to be moved to a new stage. If a task is still in its beginning stages, it will continue to be so until it reaches the end.
This allows for work to continue moving forward, while also ensuring that there is no work left behind. Managers can view the Kanban board to see how much work they have done. This information allows managers to adjust their workflow based off real-time data.
Lean manufacturing, another method to control inventory levels, is also an option. Lean manufacturing works to eliminate waste throughout every stage of the production chain. Anything that does nothing to add value to a product is waste. There are several types of waste that you might encounter:
-
Overproduction
-
Inventory
-
Packaging that is not necessary
-
Overstock materials
Manufacturers can reduce their costs and improve their efficiency by using these ideas.
What does it take to run a logistics business?
To be a successful businessman in logistics, you will need many skills and knowledge. Effective communication skills are necessary to work with suppliers and clients. You will need to know how to interpret data and draw conclusions. You need to be able work under pressure and manage stressful situations. In order to innovate and create new ways to improve efficiency, creativity is essential. You will need strong leadership skills to motivate and direct your team members towards achieving their organizational goals.
It is important to be organized and efficient in order to meet tight deadlines.
Statistics
- According to the United Nations Industrial Development Organization (UNIDO), China is the top manufacturer worldwide by 2019 output, producing 28.7% of the total global manufacturing output, followed by the United States, Japan, Germany, and India.[52][53] (en.wikipedia.org)
- It's estimated that 10.8% of the U.S. GDP in 2020 was contributed to manufacturing. (investopedia.com)
- (2:04) MTO is a production technique wherein products are customized according to customer specifications, and production only starts after an order is received. (oracle.com)
- Many factories witnessed a 30% increase in output due to the shift to electric motors. (en.wikipedia.org)
- [54][55] These are the top 50 countries by the total value of manufacturing output in US dollars for its noted year according to World Bank.[56] (en.wikipedia.org)
External Links
How To
How to use 5S in Manufacturing to Increase Productivity
5S stands as "Sort", Set In Order", Standardize", Separate" and "Store". Toyota Motor Corporation invented the 5S strategy in 1954. It helps companies achieve higher levels of efficiency by improving their work environment.
The idea behind standardizing production processes is to make them repeatable and measurable. This means that every day tasks such cleaning, sorting/storing, packing, and labeling can be performed. Because workers know what they can expect, this helps them perform their jobs more efficiently.
Implementing 5S involves five steps: Sort, Set in Order, Standardize Separate, Store, and Each step requires a different action, which increases efficiency. For example, when you sort things, you make them easy to find later. Once you have placed items in an ordered fashion, you will put them together. You then organize your inventory in groups. Finally, label all containers correctly.
Employees must be able to critically examine their work practices. Employees need to understand the reasons they do certain jobs and determine if there is a better way. To implement the 5S system, employees must acquire new skills and techniques.
In addition to improving efficiency, the 5S system also increases morale and teamwork among employees. Once they start to notice improvements, they are motivated to keep working towards their goal of increasing efficiency.