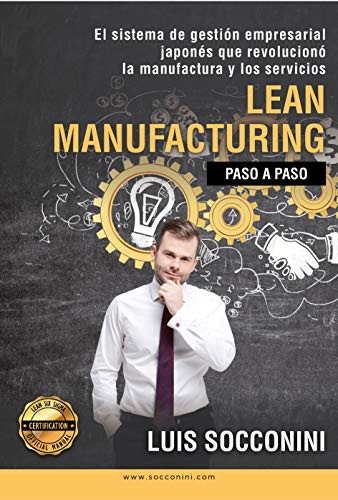
Japanese factories make high-quality products at affordable prices. They are the backbone for the country's economy and account for five per cent GDP. They have been challenged by tighter standards and increased competition as well as the cost pressures from the recent recession.
A white paper published by the government last year found that Japanese companies were not prepared to handle a cut in parts procurement. The recession had a devastating effect on the Japanese auto industry. Traditionally, the car manufacturing industry relies on 30,000 different parts, so a disruption to the supply chain can stop production. Some parts cannot be replaced.
In order to keep the quality of their products high, Japanese manufacturers are working closely with suppliers to solve problems and improve efficiency. They are also encouraging feedback from workers, salesmen and quality inspectors.
Japanese manufacturers are concerned about the high number of accidents on the factory floor. There have been a series of safety scandals that have erupted across the country's manufacturing sector. This has led the government to pay more attention to the standards of work in factories.
Non-regular staff is another problem that has impacted the production of Japanese products. Although non-regular staff allow companies to cut labor costs, they can also de-skill production workers and increase the likelihood of accidents. For their employees to be more safe and competent, companies are now focusing on training them.
Japan's increasing labor shortage is due to its declining birthrate. Companies complaining about a shortage of labor are at an all-time high of 25 years. Japanese companies will face increased challenges if the workforce shrinks.
Despite the shortage of skilled workers, a large percentage of factories have been cutting costs. There are a growing number of "factories", which employ less than ten people. Many of these small workshops create the finest equipment in the entire world.
China and South Korea are increasingly challenging the Japanese manufacturing sector. As a result, many factories are trying to improve productivity and cut costs. The Japanese government warns that the industry could lose its competitive edge on overseas markets.
Japan is confronted with increased competition from Asia as well as abroad and it is questioning whether its ability to adapt and adjust its processes to meet this demand. Even if it is able to adapt, skilled workers are expected to increase.
Japanese factories are a major source of components for global markets. They also have advanced materials such silicon chips, which are used to make smart phones and computers. Although Chinese factories are skilled in low-cost assembly, the Japanese supply essential components.
While they have tried to improve their quality and productivity, the Japanese have also faced increased competition from other countries. They have had to reduce their costs due to the fact that their products are less valuable in the domestic market. Despite these difficulties, the Japanese managed to continue producing high quality products.
FAQ
What is the difference between a production planner and a project manager?
The primary difference between a producer planner and a manager of a project is that the manager usually plans and organizes the whole project, while a production planner is only involved in the planning stage.
Why automate your warehouse?
Modern warehousing has seen automation take center stage. E-commerce has brought increased demand for more efficient and quicker delivery times.
Warehouses should be able adapt quickly to new needs. To do so, they must invest heavily in technology. Automating warehouses has many benefits. Here are some of the reasons automation is worth your investment:
-
Increases throughput/productivity
-
Reduces errors
-
Accuracy is improved
-
Safety is boosted
-
Eliminates bottlenecks
-
Allows companies to scale more easily
-
Increases efficiency of workers
-
Provides visibility into everything that happens in the warehouse
-
Enhances customer experience
-
Improves employee satisfaction
-
It reduces downtime, and increases uptime
-
This ensures that quality products are delivered promptly
-
Removes human error
-
Helps ensure compliance with regulations
What is the difference in Production Planning and Scheduling, you ask?
Production Planning (PP), is the process of deciding what production needs to take place at any given time. This can be done by forecasting demand and identifying production capabilities.
Scheduling involves the assignment of dates and times to tasks in order to complete them within the timeframe.
What skills do production planners need?
Production planners must be flexible, organized, and able handle multiple tasks. Effective communication with clients and colleagues is essential.
Statistics
- You can multiply the result by 100 to get the total percent of monthly overhead. (investopedia.com)
- Many factories witnessed a 30% increase in output due to the shift to electric motors. (en.wikipedia.org)
- According to the United Nations Industrial Development Organization (UNIDO), China is the top manufacturer worldwide by 2019 output, producing 28.7% of the total global manufacturing output, followed by the United States, Japan, Germany, and India.[52][53] (en.wikipedia.org)
- Job #1 is delivering the ordered product according to specifications: color, size, brand, and quantity. (netsuite.com)
- According to a Statista study, U.S. businesses spent $1.63 trillion on logistics in 2019, moving goods from origin to end user through various supply chain network segments. (netsuite.com)
External Links
How To
How to use 5S in Manufacturing to Increase Productivity
5S stands as "Sort", Set In Order", Standardize", Separate" and "Store". Toyota Motor Corporation invented the 5S strategy in 1954. It helps companies achieve higher levels of efficiency by improving their work environment.
This approach aims to standardize production procedures, making them predictable, repeatable, and easily measurable. It means tasks like cleaning, sorting or packing, labeling, and storing are done every day. This knowledge allows workers to be more efficient in their work because they are aware of what to expect.
Implementing 5S requires five steps. These are Sort, Set In Order, Standardize. Separate. And Store. Each step has a different action and leads to higher efficiency. If you sort items, it makes them easier to find later. Once you have placed items in an ordered fashion, you will put them together. Then, after you separate your inventory into groups, you store those groups in containers that are easy to access. Finally, when you label your containers, you ensure everything is labeled correctly.
Employees will need to be more critical about their work. Employees must understand why they do certain tasks and decide if there's another way to accomplish them without relying on the old ways of doing things. To be successful in the 5S system, employees will need to acquire new skills and techniques.
In addition to increasing efficiency, the 5S method also improves morale and teamwork among employees. They are more motivated to achieve higher efficiency levels as they start to see improvement.