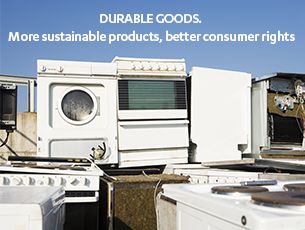
You can research the opportunities available in supply chain management to find out if you are interested. It's important to determine how many people work within a particular industry, the skills required to succeed, and what kinds of jobs are available. You can also connect with human resource professionals and recruiters when you are looking for work. Depending on your goals you may also be interested in joining a professional association to learn more about certification programs.
Supply chain management is a fast-paced field that requires a wide range of skills. Although it can seem complicated and difficult, it is also very rewarding. You'll have a lot of flexibility and opportunities, and can use your skills in many industries.
Logistics and supply-chain managers need skills in critical thinking and project management as well as interpersonal communication and sustainability. Additionally, they need to be able and able to communicate with stakeholders at all levels within an organization. They should also be able to use new technologies and comprehend international regulations.
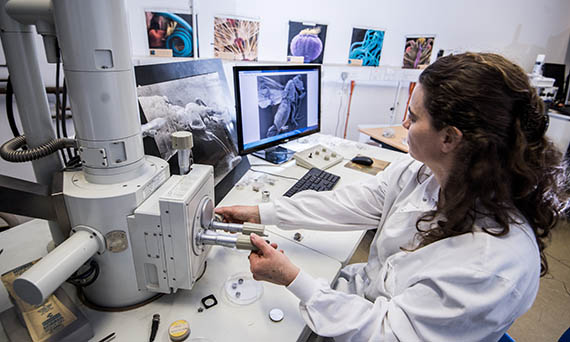
Many companies now look at their supply chain from a more holistic perspective. You'll see that not all supply chains are the same. You might be able to work on multiple product lines in a large business, but fewer opportunities for career advancement in a family-owned small business. You may also feel satisfied if the company is large.
To get started you will need a strong support network. Meet supply chain and HR professionals. Learn more about the industries you are interested in. Once you have established a strong network, you are ready to look for a position in the supply chain. Supply chain jobs are highly competitive and you will need to prove that you have the required experience and expertise.
Supply chain management is an unpredictable, fast-paced field. You must be flexible and be able solve problems quickly. If you are able to solve problems quickly, you can avoid interruptions in your supply chain. This will help you achieve your goals.
As part your supply chain career, data management is also a responsibility. This ability is crucial for making good decisions and allocating team resources. Data collection and management are essential for supporting all aspects of customer service.
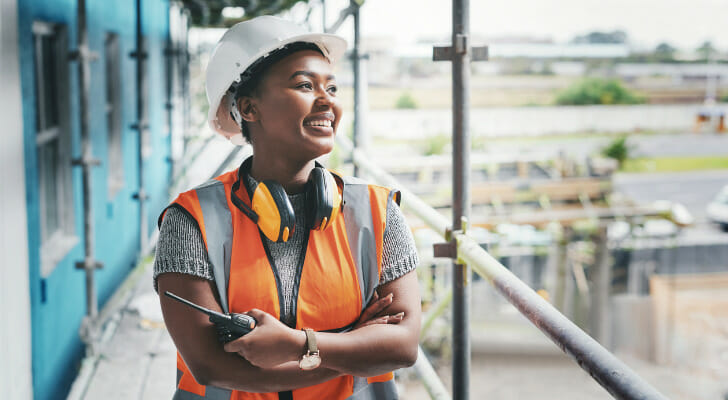
Supply chain managers should also be able to manage projects and oversee finances. Although they may be responsible for managing several projects simultaneously, they should also be able decide which ones to prioritize. They'll need to weigh the pros and cons of each decision.
Supply chain management is a career that can be pursued by those who wish to work in retail, healthcare or transportation. These positions can vary in salary and employment. You will need to have at least a few years' experience in order to be hired in each industry.
The field of supply chain management is growing and there are many opportunities for you to get involved. Take into account what you enjoy most about working alongside people and how you can make this a career in this fast-paced industry.
FAQ
What is meant by manufacturing industries?
Manufacturing Industries are those businesses that make products for sale. These products are sold to consumers. This is accomplished by using a variety of processes, including production, distribution and retailing. They manufacture goods from raw materials using machines and other equipment. This includes all types if manufactured goods.
What kind of jobs are there in logistics?
Logistics can offer many different jobs. Here are some:
-
Warehouse workers - They load and unload trucks and pallets.
-
Transportation drivers - They drive trucks and trailers to deliver goods and carry out pick-ups.
-
Freight handlers: They sort and package freight in warehouses.
-
Inventory managers - They oversee the inventory of goods in warehouses.
-
Sales representatives: They sell products to customers.
-
Logistics coordinators: They plan and manage logistics operations.
-
Purchasing agents - They purchase goods and services needed for company operations.
-
Customer service agents - They answer phone calls and respond to emails.
-
Shipping clerks: They process shipping requests and issue bills.
-
Order fillers are people who fill orders based only on what was ordered.
-
Quality control inspectors are responsible for inspecting incoming and outgoing products looking for defects.
-
Others - There is a variety of other jobs in logistics. These include transportation supervisors and cargo specialists.
What is the job of a logistics manger?
A logistics manager makes sure that all goods are delivered on-time and in good condition. This is done through his/her expertise and knowledge about the company's product range. He/she also needs to ensure adequate stock to meet demand.
Statistics
- Job #1 is delivering the ordered product according to specifications: color, size, brand, and quantity. (netsuite.com)
- You can multiply the result by 100 to get the total percent of monthly overhead. (investopedia.com)
- According to the United Nations Industrial Development Organization (UNIDO), China is the top manufacturer worldwide by 2019 output, producing 28.7% of the total global manufacturing output, followed by the United States, Japan, Germany, and India.[52][53] (en.wikipedia.org)
- [54][55] These are the top 50 countries by the total value of manufacturing output in US dollars for its noted year according to World Bank.[56] (en.wikipedia.org)
- According to a Statista study, U.S. businesses spent $1.63 trillion on logistics in 2019, moving goods from origin to end user through various supply chain network segments. (netsuite.com)
External Links
How To
How to use the Just-In Time Method in Production
Just-in-time (JIT) is a method that is used to reduce costs and maximize efficiency in business processes. It allows you to get the right amount resources at the right time. This means that your only pay for the resources you actually use. Frederick Taylor first coined this term while working in the early 1900s as a foreman. After observing how workers were paid overtime for late work, he realized that overtime was a common practice. He realized that workers should have enough time to complete their jobs before they begin work. This would help increase productivity.
JIT teaches you to plan ahead and prepare everything so you don’t waste time. Look at your entire project, from start to end. Make sure you have enough resources in place to deal with any unexpected problems. You will have the resources and people to solve any problems you anticipate. This will prevent you from spending extra money on unnecessary things.
There are many types of JIT methods.
-
Demand-driven JIT: You order the parts and materials you need for your project every other day. This will allow for you to track the material that you have left after using it. It will also allow you to predict how long it takes to produce more.
-
Inventory-based: This is a type where you stock the materials required for your projects in advance. This allows one to predict how much they will sell.
-
Project-driven: This approach involves setting aside sufficient funds to cover your project's costs. Knowing how much money you have available will help you purchase the correct amount of materials.
-
Resource-based JIT : This is probably the most popular type of JIT. Here you can allocate certain resources based purely on demand. If you have many orders, you will assign more people to manage them. If there aren't many orders, you will assign fewer people.
-
Cost-based: This is similar to resource-based, except that here you're not just concerned about how many people you have but how much each person costs.
-
Price-based: This is a variant of cost-based. However, instead of focusing on the individual workers' costs, this looks at the total price of the company.
-
Material-based: This is quite similar to cost-based, but instead of looking at the total cost of the company, you're concerned with how much raw materials you spend on average.
-
Time-based: Another variation of resource-based JIT. Instead of focusing on the cost of each employee, you will focus on the time it takes to complete a project.
-
Quality-based JIT: Another variation on resource-based JIT. Instead of worrying about the costs of each employee or how long it takes for something to be made, you should think about how quality your product is.
-
Value-based JIT: This is the latest form of JIT. In this instance, you are not concerned about the product's performance or meeting customer expectations. Instead, you focus on the added value that you provide to your market.
-
Stock-based: This inventory-based approach focuses on how many items are being produced at any one time. This method is useful when you want to increase production while decreasing inventory.
-
Just-in-time (JIT) planning: This is a combination of JIT and supply chain management. It refers to the process of scheduling the delivery of components as soon as they are ordered. It's important because it reduces lead times and increases throughput.