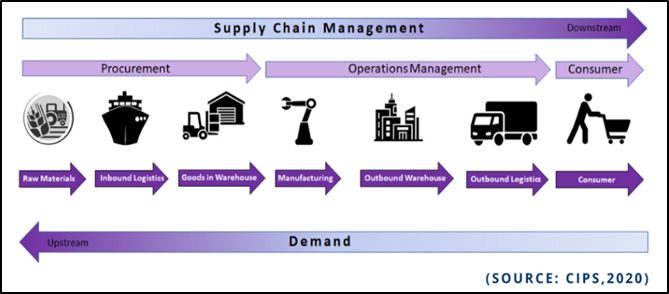
The key elements of bringing back manufacturing to America are reshoring and Opportunity zones, Deregulatory strategy, and lower transportation cost. What can the United States help to do? Here are some suggestions:
Reshoring
Some companies are now shifting production to the U.S. such as Intel which plans to invest $20 billion in two new Arizona semiconductor factories. General Motors is one of the companies that has begun to shift their production to Michigan. Michigan is expected to be a hub for lithium-based products. US Steel has decided to not build its new $3B steelmaking plant overseas, instead choosing to build a plant either in Alabama or Arkansas. Others are looking into reshoring opportunities, including Lockheed and General Electric as well as Thermo Fisher.
Opportunity zones
Trump is a passionate supporter for opportunity zones. To further support the creation of these zones, it created the White House Opportunity and Revitalization Council. This council has increased the number of quoting forms and prioritized them. However, local investors in California have one arm tied when it comes to opportunity zones. Below are five strategies local investment professionals can use to maximize their investment opportunities.
Deregulatory Policy
The United States has long struggled to attract major manufacturers and is currently losing out to countries such as China, which subsidizes the construction and equipping of new production facilities. The tide is changing, however. Walmart and other major companies are increasing their investment in the U.S. A recent study by the Manufacturing Institute reveals that American manufacturing is 9 per cent cheaper than manufacturing in nine high-cost countries.
Reduced transportation costs
Companies are motivated to move their manufacturing operations to the United States by reducing transportation costs. As a result, companies are able to bring manufacturing jobs back to the United States, where labor costs are lower than overseas. Relocating manufacturing operations from overseas is not an easy task. It could take years for jobs to be brought back to the United States. While the price of goods would go up, the benefits would outweigh the inconvenience. Recently, the Covid-19 pandemic brought supply chain issues to the forefront of the American public's consciousness. Products like toilet paper and pharmaceuticals were affected.
Qualified labor
Manufacturing's surprising political relevance was revealed by the recent presidential elections. Commentators said that "U.S. manufacturers is having a moment." Unfortunately, campaign rhetoric rarely leads to long-term commitment. Washington D.C.'s debate topics tend to be focused on trade and other issues that do not directly benefit manufacturing. They also neglect to address strategies that would support manufacturing communities and clusters.
FAQ
What is production planning?
Production planning is the process of creating a plan that covers all aspects of production. This includes scheduling, budgeting and crew, location, equipment, props, and more. It is important to have everything ready and planned before you start shooting. It should also contain information on achieving the best results on set. This includes information on shooting times, locations, cast lists and crew details.
First, you need to plan what you want to film. You may already know where you want the film to be shot, or perhaps you have specific locations and sets you wish to use. Once you have determined your scenes and locations, it is time to start figuring out the elements that you will need for each scene. You might decide you need a car, but not sure what make or model. This is where you can look up car models online and narrow down your options by choosing from different makes and models.
Once you have found the right car, you can start thinking about extras. Do you need people sitting in the front seats? Or maybe you just need someone to push the car around. Maybe you'd like to change the interior from black to a white color. These questions will help you determine the exact look and feel of your car. It is also worth considering the types of shots that you wish to take. Will you be filming close-ups or wide angles? Maybe the engine or steering wheel is what you are looking to film. This will allow you to determine the type of car you want.
Once you've determined the above, it is time to start creating a calendar. The schedule will show you when to begin shooting and when to stop. The schedule will show you when to get there, what time to leave, and when to return home. Everyone knows exactly what they should do and when. Book extra staff ahead of time if you need them. It is not worth hiring someone who won’t show up because you didn’t tell him.
Also, consider how many days you will be filming your schedule. Some projects only take one or two days, while others may last weeks. When creating your schedule, be aware of whether you need more shots per day. Multiplying takes in the same area will result both in increased costs and a longer time. It's better to be safe than sorry and shoot less takes if you're not certain whether you need more takes.
Budgeting is another crucial aspect of production plan. As it will allow you and your team to work within your financial means, setting a realistic budget is crucial. You can always lower the budget if you encounter unexpected problems. It is important to not overestimate how much you will spend. You'll end up with less money after paying for other things if the cost is underestimated.
Planning production is a tedious process. Once you have a good understanding of how everything works together, planning future projects becomes easy.
What are the four types of manufacturing?
Manufacturing is the process by which raw materials are transformed into useful products through machines and processes. It includes many different activities like designing, building and testing, packaging, shipping and selling, as well as servicing.
What are the 7 R's of logistics?
The acronym "7R's" of Logistics stands for seven principles that underpin logistics management. It was developed by International Association of Business Logisticians (IABL), and published as part of their "Seven Principles of Logistics Management Series" in 2004.
The acronym is made up of the following letters:
-
Responsible - to ensure that all actions are within the legal requirements and are not detrimental to others.
-
Reliable: Have faith in your ability or the ability to honor any promises made.
-
Reasonable - use resources efficiently and don't waste them.
-
Realistic – consider all aspects of operations, from cost-effectiveness to environmental impact.
-
Respectful – Treat others fairly and equitably.
-
You are resourceful and look for ways to save money while increasing productivity.
-
Recognizable - provide customers with value-added services.
How can we reduce manufacturing overproduction?
Improved inventory management is the key to reducing overproduction. This would reduce the time spent on unproductive activities like purchasing, storing and maintaining excess stock. This would allow us to use our resources for more productive tasks.
You can do this by adopting a Kanban method. A Kanban board is a visual display used to track work in progress. A Kanban system allows work items to move through several states before reaching their final destination. Each state is assigned a different priority.
As an example, if work is progressing from one stage of the process to another, then the current task is complete and can be transferred to the next. A task that is still in the initial stages of a process will be considered complete until it moves on to the next stage.
This allows work to move forward and ensures that no work is missed. Managers can see how much work has been done and the status of each task at any time with a Kanban Board. This allows them to adjust their workflows based on real-time information.
Lean manufacturing is another way to manage inventory levels. Lean manufacturing works to eliminate waste throughout every stage of the production chain. Anything that doesn't add value to the product is considered waste. The following are examples of common waste types:
-
Overproduction
-
Inventory
-
Packaging that is not necessary
-
Exceed materials
By implementing these ideas, manufacturers can improve efficiency and cut costs.
What is the job of a production plan?
A production planner ensures all aspects of the project are delivered on time, within budget, and within scope. A production planner ensures that the service and product meet the client's expectations.
Statistics
- (2:04) MTO is a production technique wherein products are customized according to customer specifications, and production only starts after an order is received. (oracle.com)
- According to the United Nations Industrial Development Organization (UNIDO), China is the top manufacturer worldwide by 2019 output, producing 28.7% of the total global manufacturing output, followed by the United States, Japan, Germany, and India.[52][53] (en.wikipedia.org)
- [54][55] These are the top 50 countries by the total value of manufacturing output in US dollars for its noted year according to World Bank.[56] (en.wikipedia.org)
- According to a Statista study, U.S. businesses spent $1.63 trillion on logistics in 2019, moving goods from origin to end user through various supply chain network segments. (netsuite.com)
- In the United States, for example, manufacturing makes up 15% of the economic output. (twi-global.com)
External Links
How To
How to Use Lean Manufacturing in the Production of Goods
Lean manufacturing is an approach to management that aims for efficiency and waste reduction. It was created in Japan by Taiichi Ohno during the 1970s and 80s. He received the Toyota Production System award (TPS), from Kanji Toyoda, founder of TPS. Michael L. Watkins published the original book on lean manufacturing, "The Machine That Changed the World," in 1990.
Lean manufacturing is often described as a set if principles that help improve the quality and speed of products and services. It emphasizes eliminating waste and defects throughout the value stream. Just-in-time (JIT), zero defect (TPM), and 5S are all examples of lean manufacturing. Lean manufacturing emphasizes reducing non-value-added activities like inspection, rework and waiting.
Lean manufacturing improves product quality and costs. It also helps companies reach their goals quicker and decreases employee turnover. Lean Manufacturing is one of the most efficient ways to manage the entire value chains, including suppliers and customers as well distributors and retailers. Lean manufacturing practices are widespread in many industries. Toyota's philosophy is the foundation of its success in automotives, electronics and appliances, healthcare, chemical engineers, aerospace, paper and food, among other industries.
Five fundamental principles underlie lean manufacturing.
-
Define Value - Determine the value that your business brings to society. Also, identify what sets you apart from your competitors.
-
Reduce Waste - Remove any activity which doesn't add value to your supply chain.
-
Create Flow - Make sure work runs smoothly without interruptions.
-
Standardize and Simplify – Make processes as consistent, repeatable, and as simple as possible.
-
Build relationships - Develop and maintain personal relationships with both your internal and external stakeholders.
Although lean manufacturing has always been around, it is gaining popularity in recent years because of a renewed interest for the economy after 2008's global financial crisis. To increase their competitiveness, many businesses have turned to lean manufacturing. Some economists even believe that lean manufacturing can be a key factor in economic recovery.
Lean manufacturing is becoming a popular practice in automotive. It has many advantages. These include better customer satisfaction and lower inventory levels. They also result in lower operating costs.
The principles of lean manufacturing can be applied in almost any area of an organization. Because it makes sure that all value chains are efficient and effectively managed, Lean Manufacturing is particularly helpful for organizations.
There are three main types of lean manufacturing:
-
Just-in-Time Manufacturing (JIT): This type of lean manufacturing is commonly referred to as "pull systems." JIT refers to a system in which components are assembled at the point of use instead of being produced ahead of time. This strategy aims to decrease lead times, increase availability of parts and reduce inventory.
-
Zero Defects Manufacturing (ZDM),: ZDM is a system that ensures no defective units are left the manufacturing facility. Repairing a part that is damaged during assembly should be done, not scrapping. This is also true for finished products that require minor repairs before shipping.
-
Continuous Improvement: Continuous Improvement aims to improve efficiency by continually identifying problems and making adjustments to eliminate or minimize waste. Continuous improvement involves continuous improvement of processes and people as well as tools.