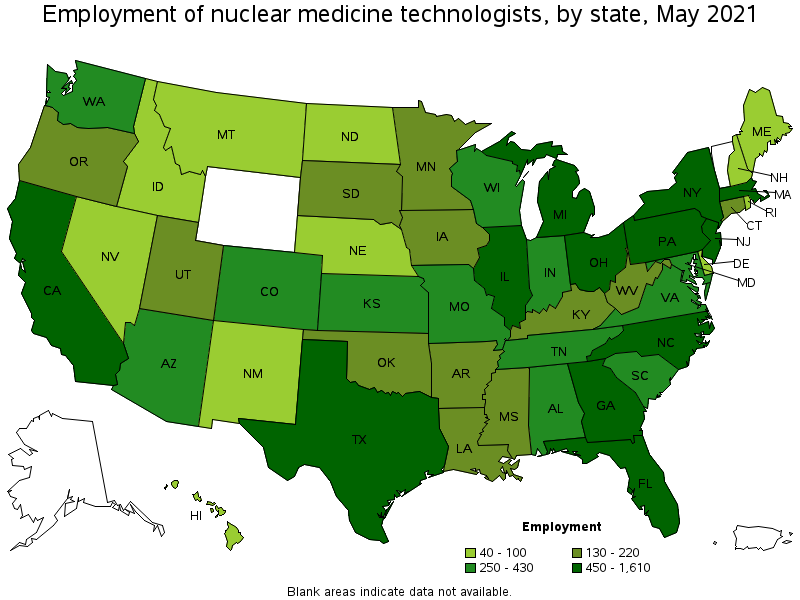
The United States is third in manufacturing in the world and saw its manufacturing output reach a record at $2.00 trillion in Q1 2018. This was nearly twice the amount it had before the Great Recession. The United States' manufacturing sector is not taking the right approach to its challenges despite a strong economy. We need to be more aggressive when addressing the challenges facing our industry, whether it is because of a lack investment or lack of skilled labor.
In 2000, the number of jobs has fallen by 5,000,000
Five million US manufacturing jobs were lost between 2000 and now. Some people blame the rise in trade with China, but that accounts only for about a fourth the decline in manufacturing jobs. Manufacturing jobs were also lost in countries that couldn't compete with Chinese imports. There are many reasons why manufacturing jobs have declined. Here are some of these reasons:
The US manufacturing sector has lost almost a third of its jobs over the past 20 years. It stood at 17 million in 1965, and fell to just 12 million in 2010. The decline in manufacturing jobs is not due to trade. It has been caused by structural problems, such as a decrease in capital investment, output and productivity. This is not sustainable. While productivity gains have a major role to play in the decline, they weren't enough to offset the loss of manufacturing jobs. Automation is the problem, not productivity increases.
Strong demand is for manufactured products
In the United States, the demand for manufactured goods remains strong despite the fact that the share of consumer spending on these items has decreased over the past few decades. In 1945, 58% of personal spending on durable goods was made, while it is now only 28%. This is due to the fact that the cost of manufacturing and selling these goods has declined while the content has risen. This has led to a significant drop in the price of computers, TVs, and audio equipment.
The recovery in manufacturing activity has boosted the production of manufactured goods in the US. According to the Fifth District Manufacturing Activity Survey (Fifth District Manufacturing Activity Survey), demand is strong for manufactured goods, and production is on the rise. However supply chain bottlenecks are hindering output. The increased production has put stress on supply chains, and respondents have reported supply chain disruptions that affect their ability to maintain necessary inventories. Backlogs in orders have increased and so has the time it takes for vendors to respond.
The trade deficit in manufactured products has more than doubled over the past decade
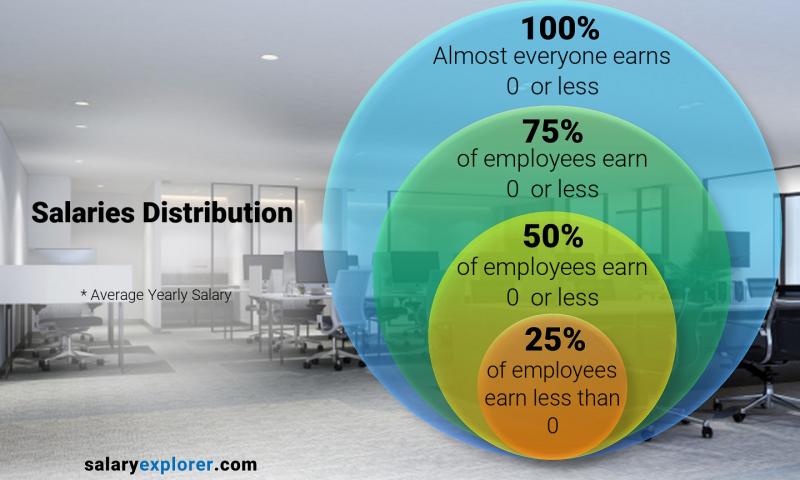
Economists are concerned that the U.S. trade surplus could lead to lower global growth and more instability among its trading partners. Others point out that high imports of US manufactured goods are not necessarily a bad thing for the U.S. economy, which is a key to maintaining global economic stability. Trade deficits may be an inevitable evil since the U.S. is heavily dependent on foreign markets to generate its economy. This may make it more difficult to achieve full employment.
Since 2000, the U.S. has almost doubled its trade deficit for manufactured goods. The US deficit is partly due to the rise in Chinese imports. This imbalance is mainly concentrated in the manufacturing sector. Wages and employment have fallen since the 1990s, which is the bigger problem. As a result, US manufacturing employment has fallen dramatically from 26 percent in 1970 to 8.5 percent in 2016. Some economists attribute China's increasing competition to the decline, but most blame the decline on automation, productivity increases and the shifting of consumer demand away form goods to services.
Industry has a shotgun approach
The US manufacturing industry is well-respected for its advanced manufacturing efforts and has many other initiatives. However, some countries have chosen to bring the internet of everything into manufacturing. The US, however, is a multi-technology nation that combines traditional mass media with Internet advertising. The result is a shotgun approach, where companies focus on many different technologies and aim for a broad customer base.
FAQ
Why automate your warehouse
Modern warehousing is becoming more automated. With the rise of ecommerce, there is a greater demand for faster delivery times as well as more efficient processes.
Warehouses must be able to quickly adapt to changing demands. They must invest heavily in technology to do this. The benefits of automating warehouses are numerous. These are just a few reasons to invest in automation.
-
Increases throughput/productivity
-
Reduces errors
-
Increases accuracy
-
Safety enhancements
-
Eliminates bottlenecks
-
Allows companies scale more easily
-
It makes workers more efficient
-
It gives visibility to everything that happens inside the warehouse
-
Enhances customer experience
-
Improves employee satisfaction
-
This reduces downtime while increasing uptime
-
You can be sure that high-quality products will arrive on time
-
Eliminates human error
-
This helps to ensure compliance with regulations
How can manufacturing efficiency be improved?
First, we need to identify which factors are most critical in affecting production times. We then need to figure out how to improve these variables. You can start by identifying the most important factors that impact production time. Once you identify them, look for solutions.
Why is logistics so important in manufacturing?
Logistics are an essential component of any business. They help you achieve great results by helping you manage all aspects of product flow, from raw materials to finished goods.
Logistics play a key role in reducing expenses and increasing efficiency.
What does warehouse refer to?
A warehouse is an area where goods are stored before being sold. It can be an indoor space or an outdoor area. Sometimes, it can be both an indoor and outdoor space.
What are the responsibilities for a manufacturing manager
Manufacturing managers must ensure that manufacturing processes are efficient, effective, and cost-effective. They should be aware of any issues within the company and respond accordingly.
They must also be able to communicate with sales and marketing departments.
They should also be knowledgeable about the latest trends in the industry so they can use this information for productivity and efficiency improvements.
What skills is required for a production planner?
To become a successful production planner, you need to be organized, flexible, and able to multitask. It is also important to be able communicate with colleagues and clients.
What can I do to learn more about manufacturing?
The best way to learn about manufacturing is through hands-on experience. But if that is not possible you can always read books and watch educational videos.
Statistics
- According to a Statista study, U.S. businesses spent $1.63 trillion on logistics in 2019, moving goods from origin to end user through various supply chain network segments. (netsuite.com)
- It's estimated that 10.8% of the U.S. GDP in 2020 was contributed to manufacturing. (investopedia.com)
- According to the United Nations Industrial Development Organization (UNIDO), China is the top manufacturer worldwide by 2019 output, producing 28.7% of the total global manufacturing output, followed by the United States, Japan, Germany, and India.[52][53] (en.wikipedia.org)
- In 2021, an estimated 12.1 million Americans work in the manufacturing sector.6 (investopedia.com)
- [54][55] These are the top 50 countries by the total value of manufacturing output in US dollars for its noted year according to World Bank.[56] (en.wikipedia.org)
External Links
How To
How to Use the Just-In-Time Method in Production
Just-intime (JIT), which is a method to minimize costs and maximize efficiency in business process, is one way. It is a process where you get the right amount of resources at the right moment when they are needed. This means that your only pay for the resources you actually use. Frederick Taylor first coined this term while working in the early 1900s as a foreman. He observed how workers were paid overtime if there were delays in their work. He concluded that if workers were given enough time before they start work, productivity would increase.
JIT is about planning ahead. You should have all the necessary resources ready to go so that you don’t waste money. Also, you should look at the whole project from start-to-finish and make sure you have the resources necessary to address any issues. You'll be prepared to handle any potential problems if you know in advance. This way, you won't end up paying extra money for things that weren't really necessary.
There are many JIT methods.
-
Demand-driven: This is a type of JIT where you order the parts/materials needed for your project regularly. This will let you track the amount of material left over after you've used it. You'll also be able to estimate how long it will take to produce more.
-
Inventory-based: This type allows you to stock the materials needed for your projects ahead of time. This allows for you to anticipate how much you can sell.
-
Project-driven: This approach involves setting aside sufficient funds to cover your project's costs. If you know the amount you require, you can buy the materials you need.
-
Resource-based JIT is the most widespread form. This is where you assign resources based upon demand. For instance, if you have a lot of orders coming in, you'll assign more people to handle them. If there aren't many orders, you will assign fewer people.
-
Cost-based : This is similar in concept to resource-based. But here, you aren't concerned about how many people your company has but how much each individual costs.
-
Price-based: This approach is very similar to the cost-based method except that you don't look at individual workers costs but the total cost of the company.
-
Material-based is an alternative to cost-based. Instead of looking at the total cost in the company, this method focuses on the average amount of raw materials that you consume.
-
Time-based JIT is another form of resource-based JIT. Instead of focusing on the cost of each employee, you will focus on the time it takes to complete a project.
-
Quality-based JIT: Another variation on resource-based JIT. Instead of thinking about how much each employee costs or how long it takes to manufacture something, you think about how good the quality of your product is.
-
Value-based JIT is the newest form of JIT. In this case, you're not concerned with how well the products perform or whether they meet customer expectations. Instead, you're focused on how much value you add to the market.
-
Stock-based. This method is inventory-based and focuses only on the actual production at any given point. This method is useful when you want to increase production while decreasing inventory.
-
Just-intime planning (JIT), is a combination JIT/sales chain management. It's the process of scheduling delivery of components immediately after they are ordered. This is important as it reduces lead time and increases throughput.