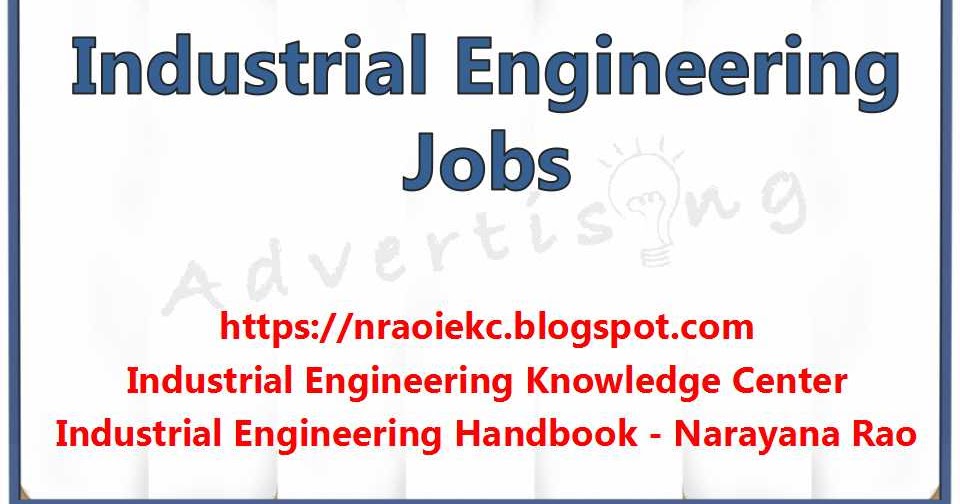
The list of manufacturers by state reveals a surprising trend: the usual suspects, such as the southeastern states, are near the top of the list. This trend is changing. Many states now show that labor costs and quality can be traded to make the best deals. This trend shows there are many factors that influence a state’s ability to attract manufacturing jobs. How do you find the right place to locate your business?
Group Five
You've found the right place if you are looking for a state-by-state list of Group Five companies. Group Five includes industrial engineering products and structural parts, as well as steel pipes. The company offers pipe design services, offering the best price-to-quality ratio of steel thickness and grade, and stiffening of thin-walled pipes. The company utilizes the latest CAD systems, computer finite analysis programs, and other advanced software to ensure that your pipe design is perfect.
Group Three
The United States Census Bureau estimates that there are about 50,000 manufacturers within Group Three. This group has a high unemployment rate and an economic growth rate, but it has a relatively low growth rate in GDP. This is because the majority of manufacturers in this group have small businesses. The data can be used as a guide, despite these limitations. Here is a list listing the top state manufacturers. Continue reading for more information.
Audi, Mercedes-Benz, BMW, and BMW are Europe's largest three manufacturers. Honda and Toyota fell to fourth and fifth respectively. However, the Detroit Three have reclaimed the Big Three title. Below is a table listing these carmakers along with their sales in each state. Click on the link below to view the top-selling model in each state. There are many models available from these manufacturers, including SUVs and midsize sedans as well as minivans.
FAQ
What does "warehouse" mean?
A warehouse, or storage facility, is where goods are stored prior to being sold. It can be either an indoor or outdoor space. It could be one or both.
How can overproduction in manufacturing be reduced?
It is essential to find better ways to manage inventory to reduce overproduction. This would reduce the amount of time spent on unnecessary activities such as purchasing, storing, and maintaining excess stock. We could use these resources to do other productive tasks.
Kanban systems are one way to achieve this. A Kanbanboard is a visual tool that allows you to keep track of the work being done. Work items are moved through various states to reach their destination in a Kanban system. Each state represents an individual priority level.
When work is completed, it can be transferred to the next stage. But if a task remains in the beginning stages it will stay that way until it reaches its end.
This keeps work moving and ensures no work is lost. Managers can see how much work has been done and the status of each task at any time with a Kanban Board. This data allows them adjust their workflow based upon real-time data.
Lean manufacturing can also be used to reduce inventory levels. Lean manufacturing focuses on eliminating waste throughout the entire production chain. Any product that isn't adding value can be considered waste. The following are examples of common waste types:
-
Overproduction
-
Inventory
-
Unnecessary packaging
-
Exceed materials
By implementing these ideas, manufacturers can improve efficiency and cut costs.
What is the best way to learn about manufacturing?
Practical experience is the best way of learning about manufacturing. You can read books, or watch instructional videos if you don't have the opportunity to do so.
How does a Production Planner differ from a Project Manager?
The primary difference between a producer planner and a manager of a project is that the manager usually plans and organizes the whole project, while a production planner is only involved in the planning stage.
How can manufacturing efficiency be improved?
First, identify the factors that affect production time. We then need to figure out how to improve these variables. If you don’t know where to begin, consider which factors have the largest impact on production times. Once you've identified them, try to find solutions for each of those factors.
Statistics
- According to the United Nations Industrial Development Organization (UNIDO), China is the top manufacturer worldwide by 2019 output, producing 28.7% of the total global manufacturing output, followed by the United States, Japan, Germany, and India.[52][53] (en.wikipedia.org)
- It's estimated that 10.8% of the U.S. GDP in 2020 was contributed to manufacturing. (investopedia.com)
- In 2021, an estimated 12.1 million Americans work in the manufacturing sector.6 (investopedia.com)
- [54][55] These are the top 50 countries by the total value of manufacturing output in US dollars for its noted year according to World Bank.[56] (en.wikipedia.org)
- Job #1 is delivering the ordered product according to specifications: color, size, brand, and quantity. (netsuite.com)
External Links
How To
How to use 5S in Manufacturing to Increase Productivity
5S stands for "Sort", "Set In Order", "Standardize", "Separate" and "Store". Toyota Motor Corporation developed the 5S method in 1954. It allows companies to improve their work environment, thereby achieving greater efficiency.
The basic idea behind this method is to standardize production processes, so they become repeatable, measurable, and predictable. This means that tasks such as cleaning, sorting, storing, packing, and labeling are performed daily. Because workers know what they can expect, this helps them perform their jobs more efficiently.
Implementing 5S requires five steps. These are Sort, Set In Order, Standardize. Separate. And Store. Each step requires a different action, which increases efficiency. Sorting things makes it easier to find them later. You arrange items by placing them in an order. Then, after you separate your inventory into groups, you store those groups in containers that are easy to access. Make sure everything is correctly labeled when you label your containers.
Employees need to reflect on how they do their jobs. Employees should understand why they do the tasks they do, and then decide if there are better ways to accomplish them. In order to use the 5S system effectively, they must be able to learn new skills.
In addition to increasing efficiency, the 5S method also improves morale and teamwork among employees. Once they start to notice improvements, they are motivated to keep working towards their goal of increasing efficiency.