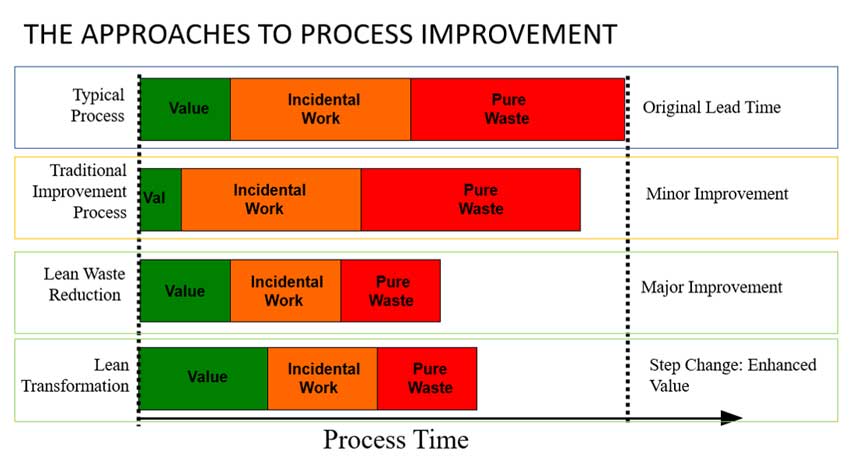
Non-value added activities are those that do not contribute to the product or service being produced. Although it might be necessary or helpful, it doesn't directly contribute to the final product's value. For example, if you want to cut lumber to the right dimensions, sharpening your saw is necessary. However, sharpening the saw does not enhance the value of the finished product.
First, define value to understand non-value added activities. Value is what customers pay for a product, or service. This will vary depending on which product or service is being offered. It is crucial to add value to your product or service in order for your business's success. It is not possible for a business to succeed if it does not offer value through its products and services. Customers will also be lost if a business does not add value to its products or services.
In order to determine if an action has value, ask yourself "Does it add any value to the product/service?" There are three possible answers. The first is to determine how the action impacts the value of the finished product. Another way is to determine how the action contributes toward customer satisfaction. Last, ask yourself the question "Does it contribute to customer satisfaction?"
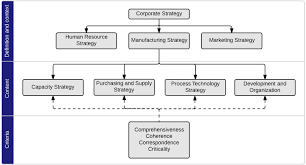
Value-added activities are those that have a positive return on investments. A value-added activity could be selling merchandise. Because it generates a profit, selling merchandise is a worthwhile activity. Selling merchandise is an attractive activity because it helps to recover manufacturing costs.
It is important to identify a value-added activity, but this does not guarantee success. The value-added activity has to be created in a way that meets the customer's expectations. The right process will ensure that the product or service arrives on time and is of high quality. The wrong process can lead to delays and quality problems.
Understanding what a non-valued task is will help you identify a value-added function. Non-valued activities are tasks that do not change the form or function of the product or service. The following are examples of non-valued actions: checking, inspecting or billing.
Activities that are not valued by customers or contribute to customer satisfaction are called non-valued. They are also activities that consume resources and incur expenses. It will help you improve the speed, quality and service level of your processes by identifying any wastes. Taking steps to eliminate wastes will improve your cash flow and competitive profile.
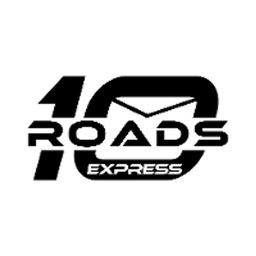
The most common mistake is to waste time on activities that are not value added. Some examples of non-valued activities are waiting, performing inspections, and repairing defective items. Other activities that are not valuable to the finished product include copying documents, moving material, and filing paperwork.
You can determine whether your current process is optimizing your potential by creating a list that includes processes that add value to your product or service. You can save time, money and resources by breaking down the process.
FAQ
What does it mean to be a manufacturer?
Manufacturing Industries is a group of businesses that produce goods for sale. The people who buy these products are called consumers. These companies employ many processes to achieve this purpose, such as production and distribution, retailing, management and so on. They produce goods from raw materials by using machines and other machinery. This includes all types if manufactured goods.
What is manufacturing and logistics?
Manufacturing is the process of creating goods from raw materials by using machines and processes. Logistics includes all aspects related to supply chain management, such as procurement, distribution planning, inventory control and transportation. Sometimes manufacturing and logistics are combined to refer to a wider term that includes both the process of creating products as well as their delivery to customers.
Is it necessary to be familiar with Manufacturing Processes before we learn about Logistics.
No. It doesn't matter if you don't know anything about manufacturing before you learn about logistics. Understanding the manufacturing process will allow you to better understand logistics.
Statistics
- According to a Statista study, U.S. businesses spent $1.63 trillion on logistics in 2019, moving goods from origin to end user through various supply chain network segments. (netsuite.com)
- In the United States, for example, manufacturing makes up 15% of the economic output. (twi-global.com)
- According to the United Nations Industrial Development Organization (UNIDO), China is the top manufacturer worldwide by 2019 output, producing 28.7% of the total global manufacturing output, followed by the United States, Japan, Germany, and India.[52][53] (en.wikipedia.org)
- It's estimated that 10.8% of the U.S. GDP in 2020 was contributed to manufacturing. (investopedia.com)
- Many factories witnessed a 30% increase in output due to the shift to electric motors. (en.wikipedia.org)
External Links
How To
How to use 5S in Manufacturing to Increase Productivity
5S stands in for "Sort", the "Set In Order", "Standardize", or "Separate". Toyota Motor Corporation developed the 5S method in 1954. It helps companies achieve higher levels of efficiency by improving their work environment.
This method aims to standardize production processes so that they are repeatable, measurable and predictable. This means that daily tasks such as cleaning and sorting, storage, packing, labeling, and packaging are possible. Because workers know what they can expect, this helps them perform their jobs more efficiently.
There are five steps that you need to follow in order to implement 5S. Each step requires a different action to increase efficiency. If you sort items, it makes them easier to find later. When you arrange items, you place them together. Next, organize your inventory into categories and store them in containers that are easily accessible. Make sure everything is correctly labeled when you label your containers.
Employees will need to be more critical about their work. Employees need to understand the reasons they do certain jobs and determine if there is a better way. They will need to develop new skills and techniques in order for the 5S system to be implemented.
The 5S Method not only improves efficiency, but it also helps employees to be more productive and happier. As they begin to see improvements, they feel motivated to continue working towards the goal of achieving higher levels of efficiency.