
There are many reasons supply chain disruptions could occur. You can think of natural disasters, product recalls, or delays in transport as examples. These interruptions can result in price increases and margin reductions. To continue production, some companies may need a change in their sourcing strategies. In many cases, companies will need to re-evaluate their supply networks, diversify their production, and audit their current inventories to prepare for the next disruption.
Various industries, such as transportation, electronics, and pharmaceuticals, have experienced supply chain disruptions. In some cases, the disruption was due to an internal issue at a company, while in other cases it was a response to a global event. A pandemic in one example caused widespread disruptions to the health systems of several countries. It also had an adverse impact on retail. The pandemic forced governments into adopting policies to stop the spread of the disease.
A pandemic can affect a company's workforce, distribution, and manufacturing processes. This can affect the production of essential products, which means companies will need to re-evaluate and adjust their production and supply chains. Depending on the severity of the disruption, the impact can range from a few weeks to months. Businesses will need to evaluate their inventory and, if necessary, reallocate capital.
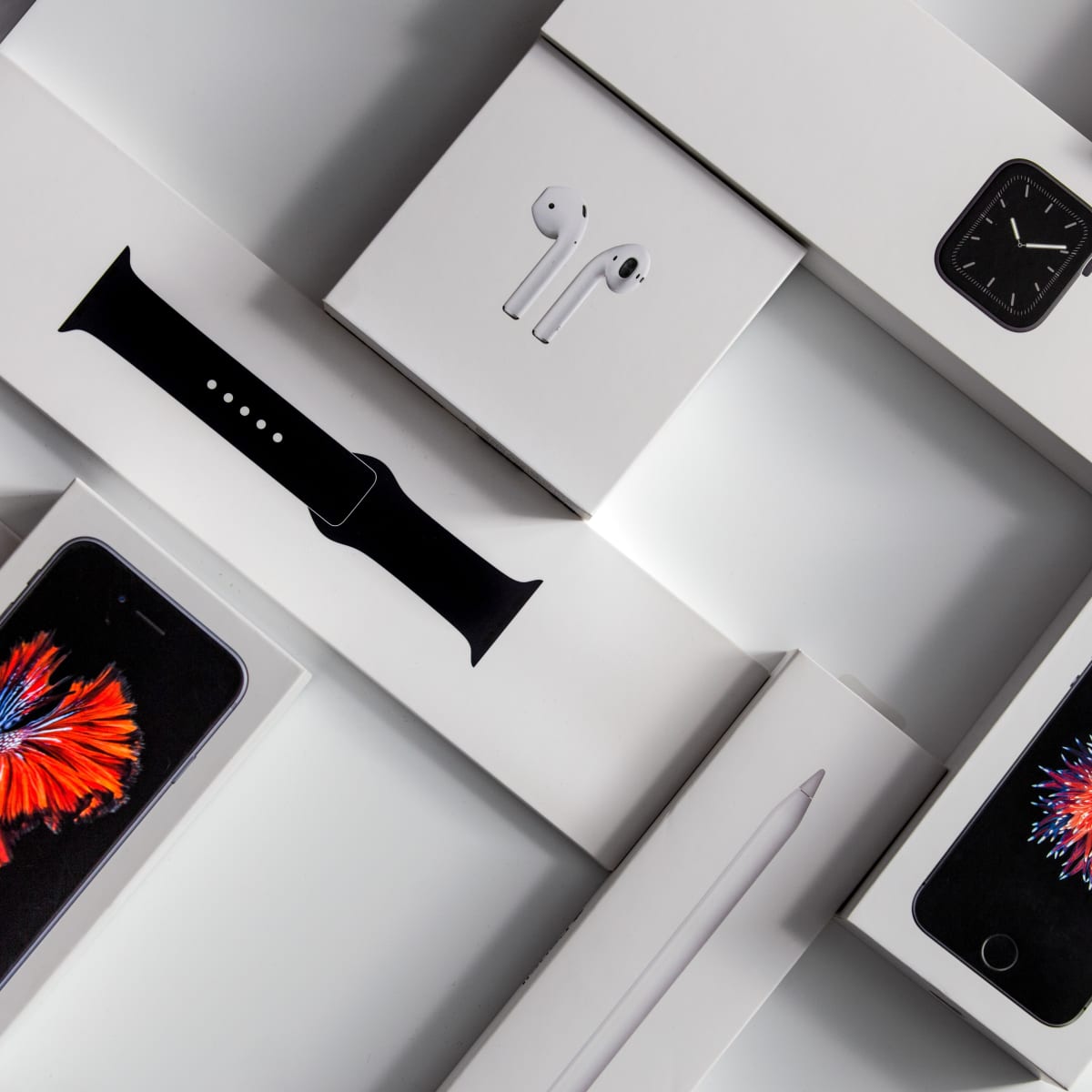
Disruption may occur at any stage in the supply chain and can impact both supply or demand. In most cases, the demand will be more affected that the supply. But if the supply side is affected by a pandemic, it will have a ripple effect on the entire economy.
Supply chain disruptions can have major consequences for a company and are often hard to predict. While seasonal fluctuations are easy to spot, it's more difficult to predict the rapid shifts in consumer behavior. Predictive analytics is one of the best tools to detect potential problems and mitigate them.
Unemployment is another reason supply chain disruptions can occur. If they cannot get equipment or parts from reliable suppliers, companies can lose productivity. A machine failure can also disrupt an entire operation.
Natural disasters, market fluctuations, geopolitical stability, and other factors are all common causes of supply-chain disruptions. Natural disasters can be very costly and disrupt the global supply chains. Supply chain disruption can also be caused by a power cut, telecommunications blackouts, and even border closures. Moreover, companies may be forced to store large amounts of stock to protect their business.
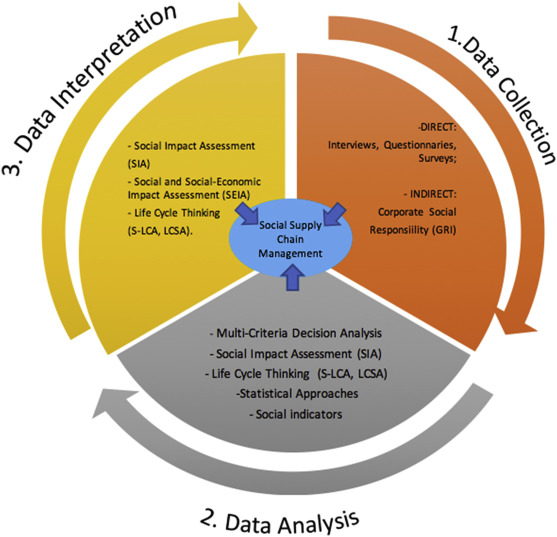
The impact of disruptions in supply chains is generally low. Companies will need to take action if they detect a disruption, and a majority of them will need to do so at some point. It is important to identify issues quickly in order to reduce conflict.
In a recent survey, Ernest & Young LLP found that 72 percent of companies have experienced a disruption at some point, and 57 percent have reported adverse effects. Some of these issues can easily be solved quickly, while others require a more strategic approach.
FAQ
Is it necessary to be familiar with Manufacturing Processes before we learn about Logistics.
No. You don't have to know about manufacturing processes before learning about logistics. Understanding the manufacturing process will allow you to better understand logistics.
What are the 7 Rs of logistics?
The acronym "7R's" of Logistics stands for seven principles that underpin logistics management. It was developed by the International Association of Business Logisticians (IABL) and published in 2004 as part of its "Seven Principles of Logistics Management" series.
The acronym is made up of the following letters:
-
Responsive - ensure all actions are legal and not harmful to others.
-
Reliable - have confidence in the ability to deliver on commitments made.
-
Be responsible - Use resources efficiently and avoid wasting them.
-
Realistic - consider all aspects of operations, including cost-effectiveness and environmental impact.
-
Respectful - treat people fairly and equitably.
-
Resourceful - look for opportunities to save money and increase productivity.
-
Recognizable - Provide value-added services to customers
How can manufacturing prevent production bottlenecks?
You can avoid bottlenecks in production by making sure that everything runs smoothly throughout the production cycle, from the moment you receive an order to the moment the product is shipped.
This includes planning to meet capacity requirements and quality control.
This can be done by using continuous improvement techniques, such as Six Sigma.
Six Sigma is a management system used to improve quality and reduce waste in every aspect of your organization.
It seeks to eliminate variation and create consistency in your work.
What are the products and services of logistics?
Logistics are the activities involved in moving goods from point A to point B.
They include all aspects associated with transport including packaging, loading transporting, unloading storage, warehousing inventory management customer service, distribution returns and recycling.
Logisticians ensure the product reaches its destination in the most efficient manner. They help companies manage their supply chain efficiency by providing information on demand forecasts, stock levels, production schedules, and availability of raw materials.
They coordinate with vendors and suppliers, keep track of shipments, monitor quality standards and perform inventory and order replenishment.
What are the responsibilities of a manufacturing manager
Manufacturing managers must ensure that manufacturing processes are efficient, effective, and cost-effective. They should be aware of any issues within the company and respond accordingly.
They should also be able communicate with other departments, such as sales or marketing.
They should be informed about industry trends and be able make use of this information to improve their productivity and efficiency.
Statistics
- Job #1 is delivering the ordered product according to specifications: color, size, brand, and quantity. (netsuite.com)
- (2:04) MTO is a production technique wherein products are customized according to customer specifications, and production only starts after an order is received. (oracle.com)
- According to the United Nations Industrial Development Organization (UNIDO), China is the top manufacturer worldwide by 2019 output, producing 28.7% of the total global manufacturing output, followed by the United States, Japan, Germany, and India.[52][53] (en.wikipedia.org)
- You can multiply the result by 100 to get the total percent of monthly overhead. (investopedia.com)
- According to a Statista study, U.S. businesses spent $1.63 trillion on logistics in 2019, moving goods from origin to end user through various supply chain network segments. (netsuite.com)
External Links
How To
How to use 5S to increase Productivity in Manufacturing
5S stands in for "Sort", the "Set In Order", "Standardize", or "Separate". The 5S methodology was developed at Toyota Motor Corporation in 1954. It improves the work environment and helps companies to achieve greater efficiency.
The idea behind standardizing production processes is to make them repeatable and measurable. Cleaning, sorting and packing are all done daily. Through these actions, workers can perform their jobs more efficiently because they know what to expect from them.
Five steps are required to implement 5S: Sort, Set In Order, Standardize. Separate. Each step requires a different action to increase efficiency. By sorting, for example, you make it easy to find the items later. When you arrange items, you place them together. You then organize your inventory in groups. Finally, label all containers correctly.
Employees need to reflect on how they do their jobs. Employees need to be able understand their motivations and discover alternative ways to do them. To implement the 5S system, employees must acquire new skills and techniques.
The 5S method not only increases efficiency but also boosts morale and teamwork. Once they start to notice improvements, they are motivated to keep working towards their goal of increasing efficiency.