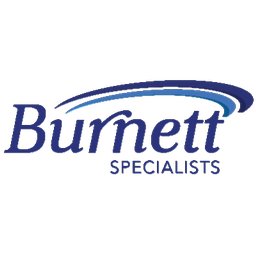
Six-sigma principles can be used to improve productivity and efficiency in a company. Moreover, they reduce costs and improve quality. It is possible to implement the process using different strategies and methodologies such as process maps, statistical analysis and control charts.
What are the 6 Sigma Principles?
The 6 Sigma principles are a series of methods for identifying and eliminating manufacturing defects. They can be implemented in many ways, and the results can be huge. The can also be used to ensure that every process runs smoothly and efficiently.
Lean six sigma:
The first principle of lean six sigma is to understand the real workflow. You need to take note of the actual process to determine where you can make improvements. This is a very important step because it allows you to determine the problem and create a solution.
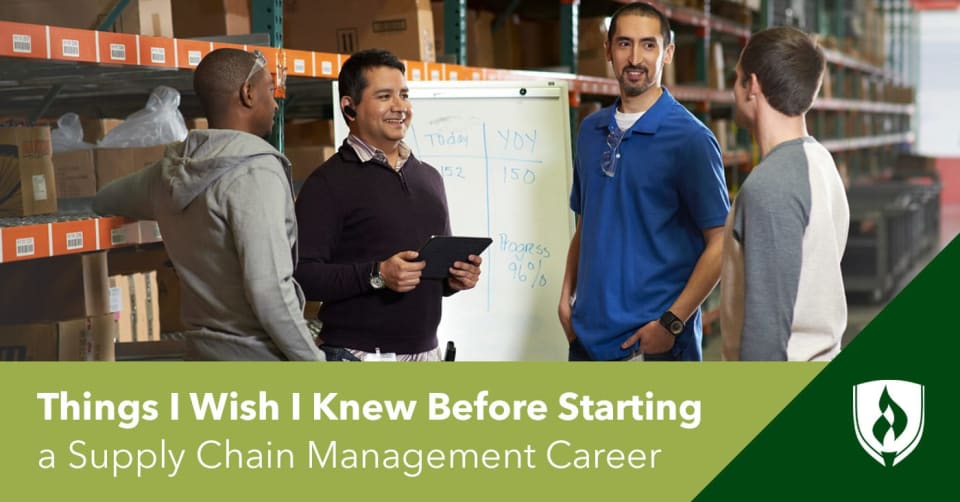
This is an important principle for any type of project, and it is especially crucial in the area of process improvement. It is difficult to change a process if you do not know how to improve it.
To improve a business process, it may be necessary to alter the work practices of employees or to adjust their approach. It may seem like a difficult task, but by adapting, a business can make changes quickly and effectively.
Six sigma is built on the principle that employees should be empowered to take part in a project. The reason is that it is difficult to implement the changes if upper management only is involved.
The training of employees in the processes is crucial to ensure they understand the concepts and can eliminate errors. Also, they should have the resources and tools necessary to be a part of the project.
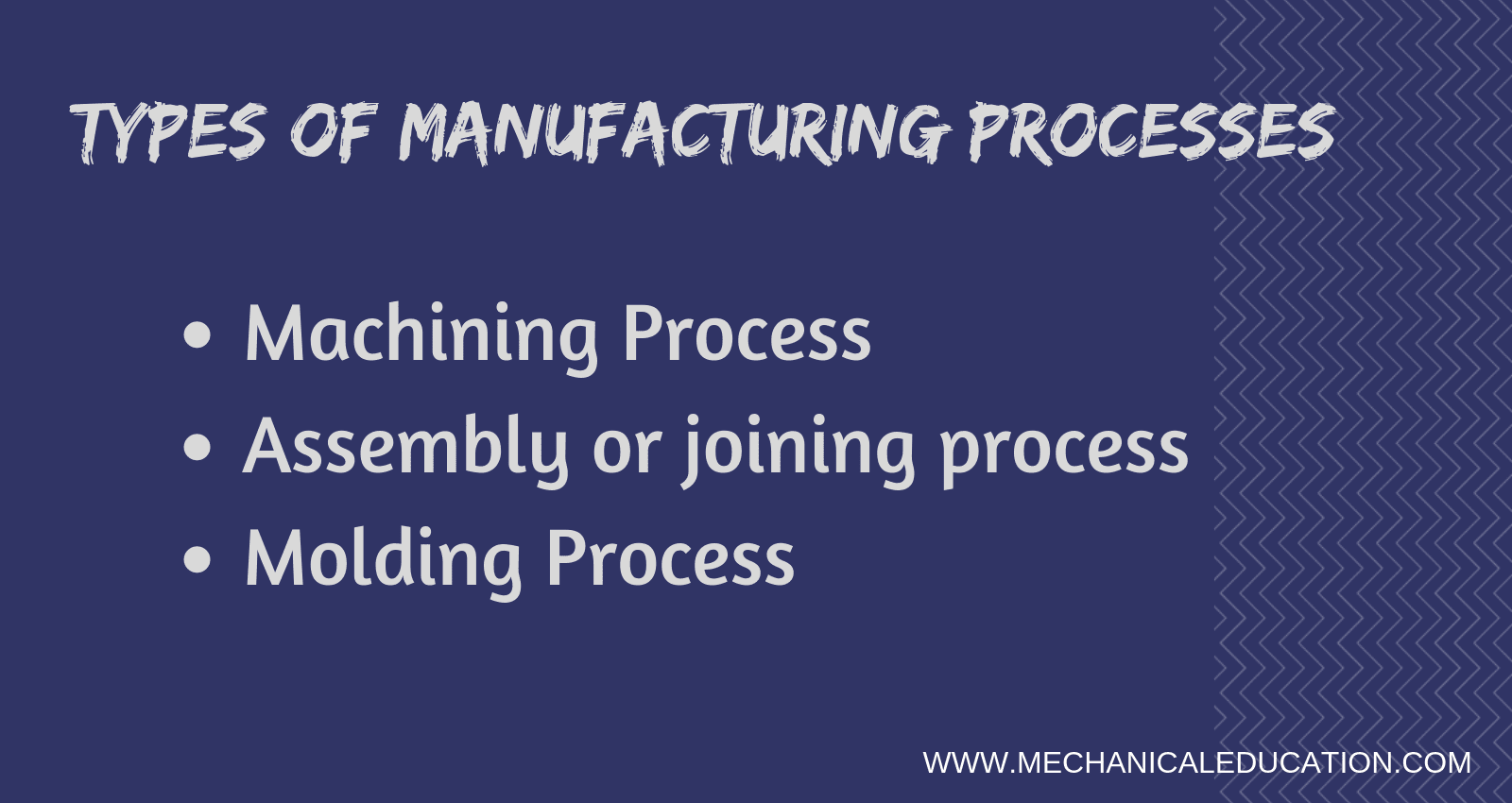
What are the six sigma Values?
Six Sigma values focus on customer satisfaction and loyalty, believe that each process should be designed for minimal waste, and place an emphasis on measuring and analysing data. These factors are all important in achieving a high level of satisfaction and loyalty from customers.
Consistency and reliability are also part of the six-sigma values. These factors play a vital role in industries that demand high quality products and/or services. They should apply to all aspects within the company and be continually evaluated and revised, if required.
The six sigma principles help improve the efficiency of organizations and their operations. They are also important for creating a sustainable system that will allow the company to grow and succeed. This is a great method to make sure that your company remains competitive and profitable.
FAQ
How can overproduction in manufacturing be reduced?
The key to reducing overproduction lies in developing better ways to manage inventory. This would decrease the time that is spent on inefficient activities like purchasing, storing, or maintaining excess stock. This will allow us to free up resources for more productive tasks.
A Kanban system is one way to achieve this. A Kanban board, a visual display to show the progress of work, is called a Kanban board. Work items are moved through various states to reach their destination in a Kanban system. Each state represents a different priority.
When work is completed, it can be transferred to the next stage. However, if a task is still at the beginning stages, it will remain so until it reaches the end of the process.
This allows you to keep work moving along while making sure that no work gets neglected. Managers can view the Kanban board to see how much work they have done. This information allows managers to adjust their workflow based off real-time data.
Another way to control inventory levels is to implement lean manufacturing. Lean manufacturing is about eliminating waste from all stages of the production process. Anything that does nothing to add value to a product is waste. Here are some examples of common types.
-
Overproduction
-
Inventory
-
Packaging that is not necessary
-
Material surplus
Manufacturers can increase efficiency and decrease costs by implementing these ideas.
How can manufacturing avoid production bottlenecks
Avoiding production bottlenecks is as simple as keeping all processes running smoothly, from the time an order is received until the product ships.
This includes planning for both capacity requirements and quality control measures.
Continuous improvement techniques such Six Sigma can help you achieve this.
Six Sigma is a management system used to improve quality and reduce waste in every aspect of your organization.
It seeks to eliminate variation and create consistency in your work.
What are the responsibilities of a manufacturing manager
A manufacturing manager must make sure that all manufacturing processes run smoothly and effectively. They should be aware of any issues within the company and respond accordingly.
They must also be able to communicate with sales and marketing departments.
They should also be knowledgeable about the latest trends in the industry so they can use this information for productivity and efficiency improvements.
What are my options for learning more about manufacturing
You can learn the most about manufacturing by getting involved in it. However, if that's not possible, you can always read books or watch educational videos.
What are the 7 Rs of logistics management?
The acronym 7R's of Logistic is an acronym that stands for seven fundamental principles of logistics management. It was created by the International Association of Business Logisticians and published in 2004 under its "Seven Principles of Logistics Management".
The acronym is composed of the following letters.
-
Responsible - ensure that all actions taken are within legal requirements and are not harmful to others.
-
Reliable - Have confidence in your ability to fulfill all of your commitments.
-
Reasonable - use resources efficiently and don't waste them.
-
Realistic - Consider all aspects of operations, including environmental impact and cost effectiveness.
-
Respectful – Treat others fairly and equitably.
-
Resourceful - look for opportunities to save money and increase productivity.
-
Recognizable - Provide value-added services to customers
Statistics
- [54][55] These are the top 50 countries by the total value of manufacturing output in US dollars for its noted year according to World Bank.[56] (en.wikipedia.org)
- In 2021, an estimated 12.1 million Americans work in the manufacturing sector.6 (investopedia.com)
- It's estimated that 10.8% of the U.S. GDP in 2020 was contributed to manufacturing. (investopedia.com)
- According to a Statista study, U.S. businesses spent $1.63 trillion on logistics in 2019, moving goods from origin to end user through various supply chain network segments. (netsuite.com)
- You can multiply the result by 100 to get the total percent of monthly overhead. (investopedia.com)
External Links
How To
How to use 5S to increase Productivity in Manufacturing
5S stands for "Sort", "Set In Order", "Standardize", "Separate" and "Store". The 5S methodology was developed at Toyota Motor Corporation in 1954. This methodology helps companies improve their work environment to increase efficiency.
This method has the basic goal of standardizing production processes to make them repeatable. This means that every day tasks such cleaning, sorting/storing, packing, and labeling can be performed. This knowledge allows workers to be more efficient in their work because they are aware of what to expect.
Implementing 5S requires five steps. These are Sort, Set In Order, Standardize. Separate. And Store. Each step requires a different action, which increases efficiency. If you sort items, it makes them easier to find later. Once you have placed items in an ordered fashion, you will put them together. After you have divided your inventory into groups you can store them in easy-to-reach containers. Finally, when you label your containers, you ensure everything is labeled correctly.
This requires employees to critically evaluate how they work. Employees need to be able understand their motivations and discover alternative ways to do them. They will need to develop new skills and techniques in order for the 5S system to be implemented.
The 5S Method not only improves efficiency, but it also helps employees to be more productive and happier. They feel more motivated to work towards achieving greater efficiency as they see the results.