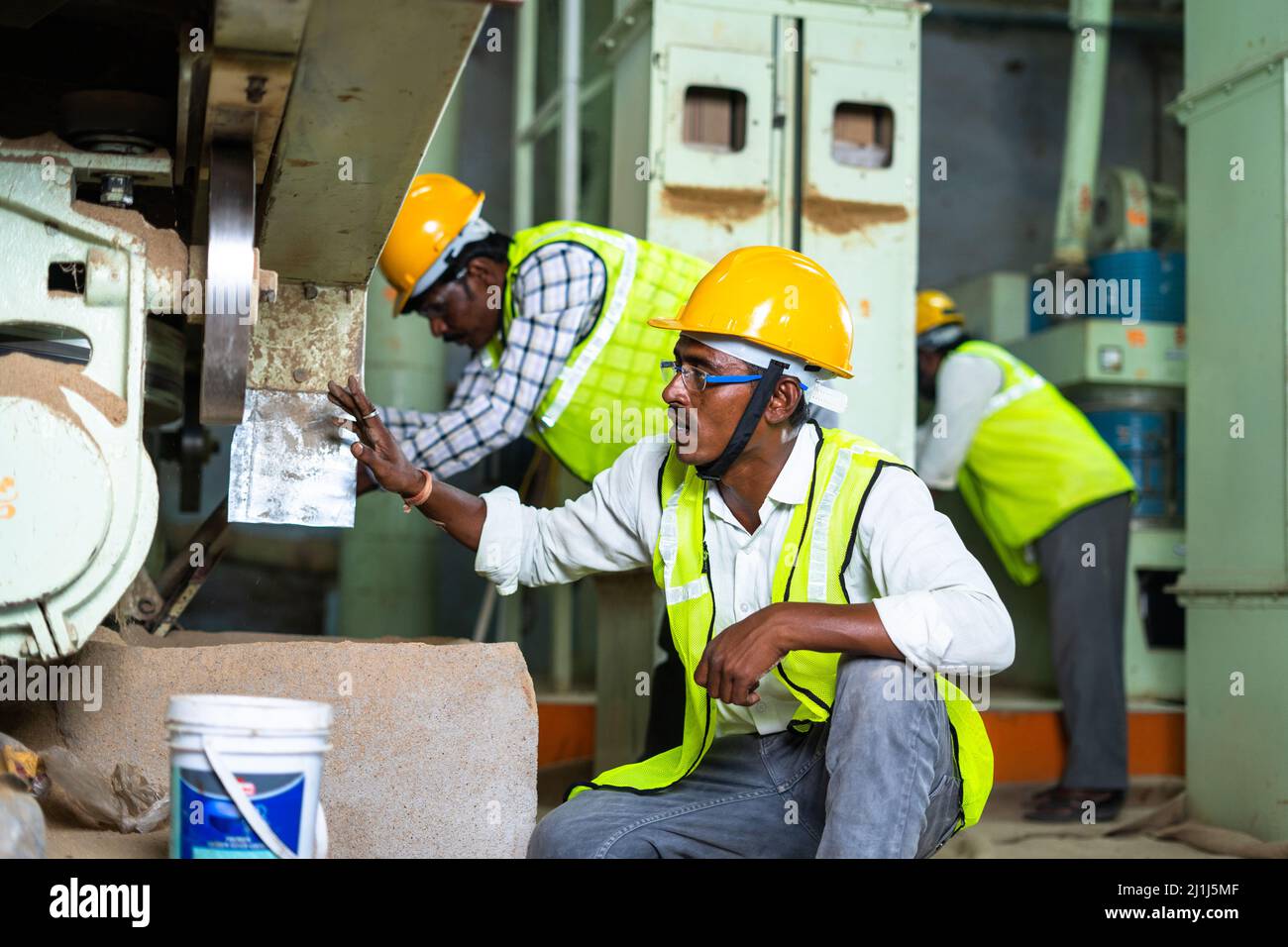
Consider lean manufacturing if you are looking to reduce costs, speed up lead times, minimize setup time, and maximize turnaround time. The benefits of lean manufacturing are clear: they reduce costs and lead time while improving the customer experience. These improvements make Lean Manufacturing the best way for your business to grow. You might still be skeptical, but here are three reasons it is the best way to produce products and reduce costs.
Lowers costs
Lean manufacturing can lead to significant efficiencies. Through reducing defects, rework and direct labor costs, manufacturers can make savings. Because labor costs are less motivating, decision-making becomes easier. A second benefit is the elimination or hazardous waste. Direct labor costs are below 15% in many industries. It is difficult to justify outsourcing manufacturing to low cost locations. This can lower overall manufacturing costs and improve customer services.

This improves lead times
Lean manufacturing has many benefits, including the ability reduce waste and increase lead times. Lean manufacturing is a philosophy that emphasizes continuous improvement or kaizen. It is a system that combines the talents and encourages employee collaboration. The process can decrease lead times by as high as 20% The key aspect of lean manufacturing, however, is the ability to make small improvements often in order to improve the product's quality and efficiency.
Shortens set-up times
The best way to shorten the time required to produce a product, is to reduce set-up periods. The time it takes for a product to be switched from its last item to the new one is called setup time. The setup time includes preparation, replacement, as well as location activities. These activities may be external or internal. External setup activities can be done while the process is still operating.
Reduces time to market
Lean manufacturing is the concept of continuous improvement. It was developed in Japan during rebuilding periods after World War II. It aimed to increase competition and reduce lead times. Companies can increase their profits and meet customer needs by reducing the time it takes for products to reach market. This method of production not only increases efficiency but also makes the facility more productive.
Improves product quality
To be successful in lean manufacturing, it is important to reduce waste, improve product value, and minimize costs. It is used by both large manufacturers and smaller businesses alike. It decreases lead times, costs, and labor. Read on for more information on how lean manufacturing can improve your business. Here are some of these key areas. Embracing lean principles can reduce lead times by 90%, improve product quality, and reduce your costs.
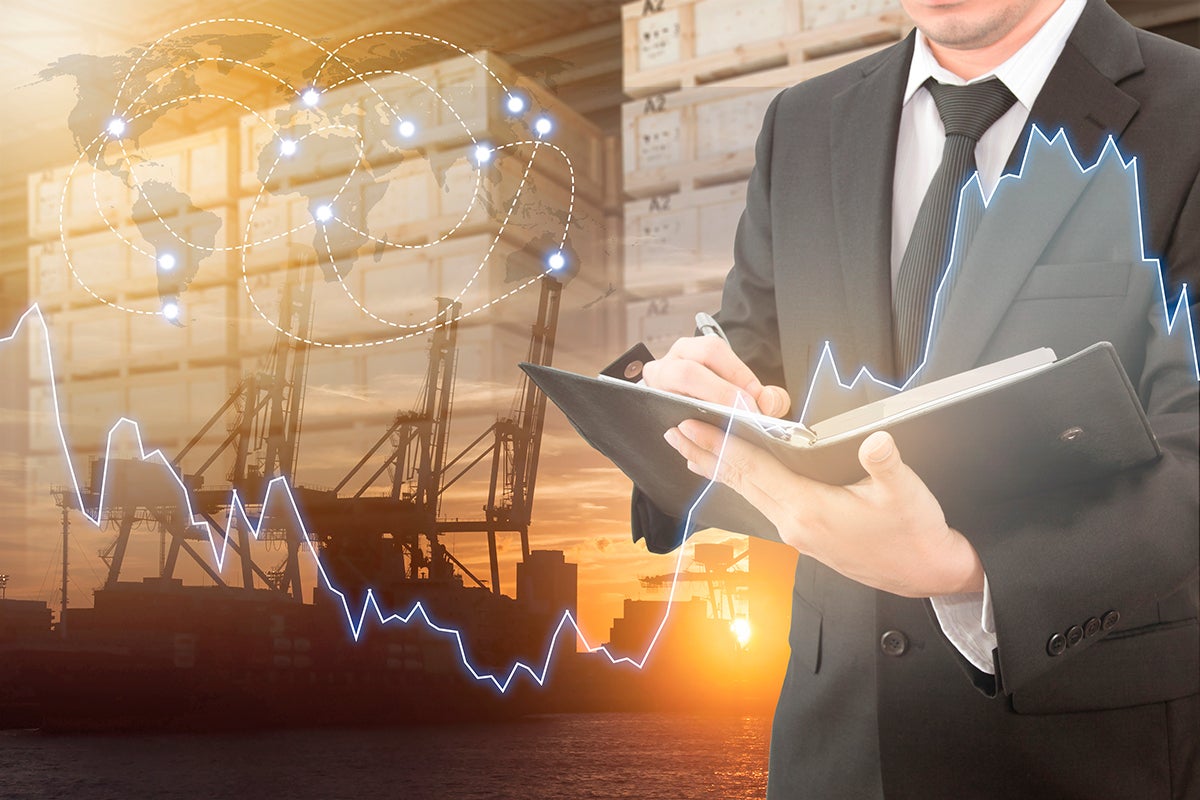
Reduces indirect labor costs
Reduced indirect labor costs is the low hanging fruit in lean manufacturing. Lean companies focus less on direct labor efficiency and look instead for ways to lower indirect labor costs. This means eliminating material handling and inspection jobs. Toyota and other companies that use lean manufacturing methods follow the same strategy. In this article we will take a closer look into how lean manufacturing can lower indirect labor cost.
FAQ
Do we need to know about Manufacturing Processes before learning about Logistics?
No. No. It is important to know about the manufacturing processes in order to understand how logistics works.
What are the essential elements of running a logistics firm?
You need to have a lot of knowledge and skills to manage a successful logistic business. Good communication skills are essential to effectively communicate with your suppliers and clients. It is important to be able to analyse data and draw conclusions. You need to be able work under pressure and manage stressful situations. You must be creative and innovative to develop new ideas to improve efficiency. You must be a strong leader to motivate others and direct them to achieve organizational goals.
To meet tight deadlines, you must also be efficient and organized.
Why automate your factory?
Modern warehousing is becoming more automated. Increased demand for efficient and faster delivery has resulted in a rise in e-commerce.
Warehouses must be able to quickly adapt to changing demands. In order to do this, they need to invest in technology. Automation of warehouses offers many benefits. Here are some of the reasons automation is worth your investment:
-
Increases throughput/productivity
-
Reduces errors
-
Improves accuracy
-
Safety increases
-
Eliminates bottlenecks
-
This allows companies to scale easily
-
This makes workers more productive
-
The warehouse can be viewed from all angles.
-
Enhances customer experience
-
Improves employee satisfaction
-
It reduces downtime, and increases uptime
-
Ensures quality products are delivered on time
-
Eliminates human error
-
It helps ensure compliance with regulations
How can manufacturing reduce production bottlenecks?
The key to avoiding bottlenecks in production is to keep all processes running smoothly throughout the entire production cycle, from the time you receive an order until the time when the product ships.
This includes planning to meet capacity requirements and quality control.
This can be done by using continuous improvement techniques, such as Six Sigma.
Six Sigma Management System is a method to increase quality and reduce waste throughout your organization.
It's all about eliminating variation and creating consistency in work.
What is production planning?
Production Planning includes planning for all aspects related to production. This document aims to ensure that everything is planned and ready when you are ready to shoot. This document should also include information on how to get the best result on set. This includes information on shooting times, locations, cast lists and crew details.
It is important to first outline the type of film you would like to make. You may have already chosen the location you want, or there are locations or sets you prefer. Once you have determined your scenes and locations, it is time to start figuring out the elements that you will need for each scene. You might decide you need a car, but not sure what make or model. If this is the case, you might start searching online for car models and then narrow your options by selecting from different makes.
After you have selected the car you want, you can begin to think about additional features. You might need to have people in the front seats. Perhaps you have someone who needs to be able to walk around the back of your car. Maybe you want to change the interior color from black to white? These questions will help determine the look and feel you want for your car. Another thing you can do is think about what type of shots are desired. Are you going to be shooting close-ups? Or wide angles? Maybe you want to show your engine or the steering wheel. This will allow you to determine the type of car you want.
Once you have made all the necessary decisions, you can start to create a schedule. You can create a schedule that will outline when you must start and finish your shoots. You will need to know when you have to be there, what time you have to leave and when your return home. So everyone is clear about what they need to do. Hire extra staff by booking them ahead of time. There is no point in hiring someone who won't turn up because you didn't let him know.
It is important to calculate the amount of filming days when you are creating your schedule. Some projects can be completed in a matter of days or weeks. Others may take several days. It is important to consider whether you require more than one photo per day when you create your schedule. Multiple shots at the same location can increase costs and make it more difficult to complete. If you are unsure if you need multiple takes, it is better to err on the side of caution and shoot fewer takes rather than risk wasting money.
Budget setting is another important aspect in production planning. You will be able to manage your resources if you have a realistic budget. Remember that you can always reduce the budget later on if you run into unforeseen problems. It is important to not overestimate how much you will spend. You will end up spending less money if you underestimate the cost of something.
Production planning is a complicated process. But once you understand how everything works together, it becomes much easier to plan future project.
Can some manufacturing processes be automated?
Yes! Automation has been around since ancient times. The Egyptians invent the wheel thousands of year ago. Nowadays, we use robots for assembly lines.
Actually, robotics can be used in manufacturing for many purposes. These include:
-
Assembly line robots
-
Robot welding
-
Robot painting
-
Robotics inspection
-
Robots that make products
Manufacturing can also be automated in many other ways. 3D printing, for example, allows us to create custom products without waiting for them to be made.
What does it mean to warehouse?
A warehouse, or storage facility, is where goods are stored prior to being sold. It can be indoors or out. In some cases, it may be a combination of both.
Statistics
- You can multiply the result by 100 to get the total percent of monthly overhead. (investopedia.com)
- [54][55] These are the top 50 countries by the total value of manufacturing output in US dollars for its noted year according to World Bank.[56] (en.wikipedia.org)
- Job #1 is delivering the ordered product according to specifications: color, size, brand, and quantity. (netsuite.com)
- (2:04) MTO is a production technique wherein products are customized according to customer specifications, and production only starts after an order is received. (oracle.com)
- According to a Statista study, U.S. businesses spent $1.63 trillion on logistics in 2019, moving goods from origin to end user through various supply chain network segments. (netsuite.com)
External Links
How To
How to Use Six Sigma in Manufacturing
Six Sigma is defined by "the application SPC (statistical process control) techniques to achieve continuous improvements." Motorola's Quality Improvement Department in Tokyo, Japan developed Six Sigma in 1986. The basic idea behind Six Sigma is to improve quality by improving processes through standardization and eliminating defects. This method has been adopted by many companies in recent years as they believe there are no perfect products or services. The main goal of Six Sigma is to reduce variation from the mean value of production. This means that if you take a sample of your product, then measure its performance against the average, you can find out what percentage of the time the process deviates from the norm. If you notice a large deviation, then it is time to fix it.
Understanding the dynamics of variability within your business is the first step in Six Sigma. Once you have a good understanding of the basics, you can identify potential sources of variation. Also, you will need to identify the sources of variation. Random variations happen when people make errors; systematic variations are caused externally. If you make widgets and some of them end up on the assembly line, then those are considered random variations. But if you notice that every widget you make falls apart at the exact same place each time, this would indicate that there is a problem.
Once you identify the problem areas, it is time to create solutions. You might need to change the way you work or completely redesign the process. After implementing the new changes, you should test them again to see if they worked. If they didn't work, then you'll need to go back to the drawing board and come up with another plan.