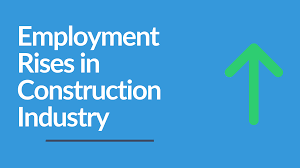
Assocations of manufacturers offer their members opportunities to network, share information and resources. Businesses can benefit from the creation of relationships outside their industry. The group also allows members to voice their concerns with regards to manufacturing and have them heard by all levels of government.
The Manufacturing Institute
The Manufacturing Institute is a nonprofit organization that aims to promote and encourage the advancement of manufacturing. It does this through the use of technology, education and training. It also attempts to promote the value and importance of manufacturing through the recognition of those in the field.
American Manufacturers Association
The American Manufacturers Association (AMA) is a trade organization that helps companies improve their business strategy by assisting them in developing and using the latest technology. The American Manufacturers Association offers a wide range of services to its members, such as legal advice and news updates about the manufacturing industry.
NAM (National Association of Manufacturers)
National Association of Manufacturers. This is a trade association with 501(c.6) status that represents both large and small manufacturers in America. The National Association of Manufacturers' goal is to ensure government policies are in place to benefit both manufacturers and their workers.
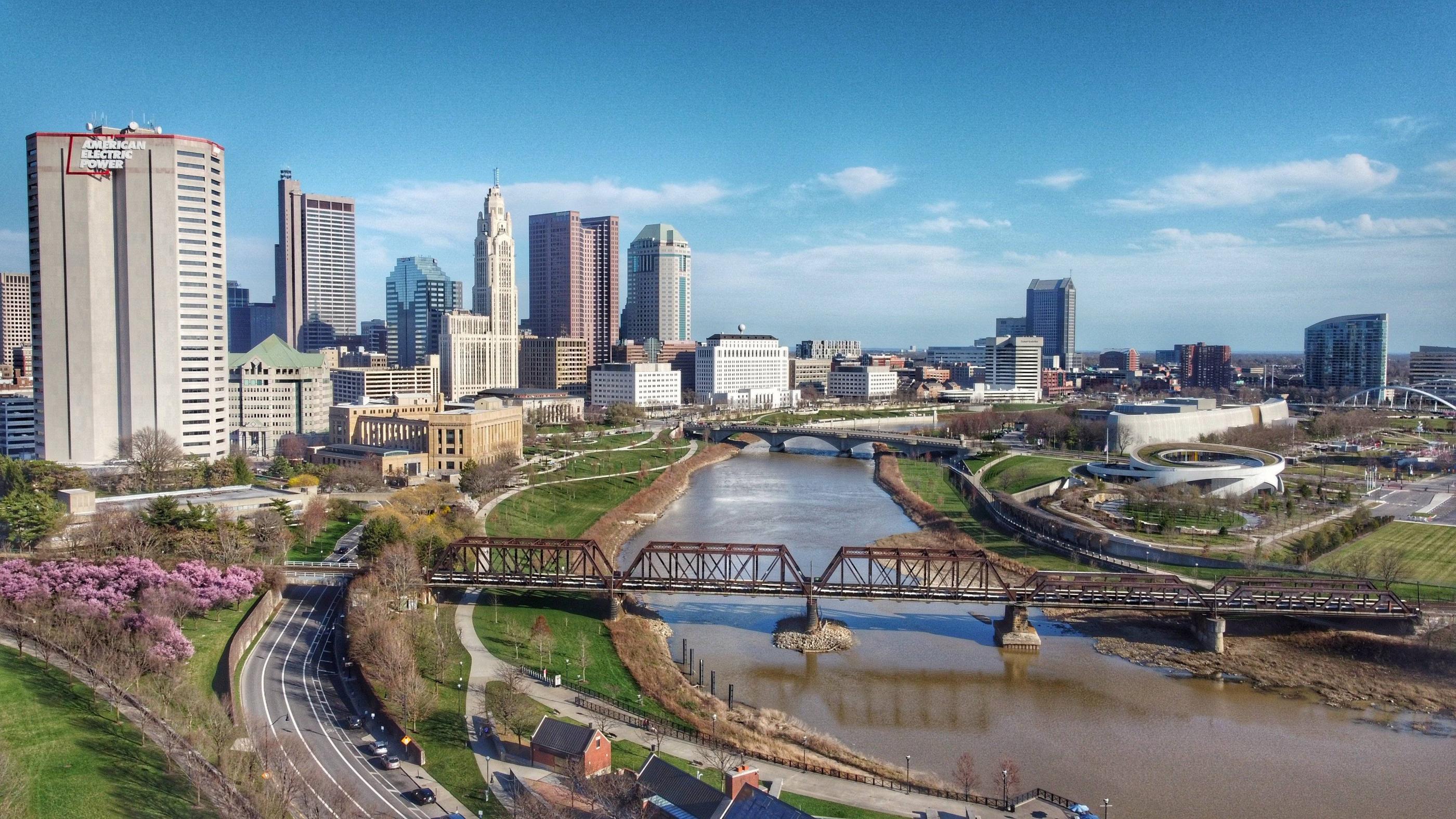
NAM has 260 member associations who collaborate on matters that are important to the industry. It is also a member of the World Trade Organization and aims to lower trade barriers.
Fabricators and Manufacturers' Association International
Fabricators & Manufacturers Association International focuses its efforts on the metal forming and processing industries. Its goals include growing, sustaining and promoting the manufacturing industry through scholarships.
FMA's focus is also on networking and training, while encouraging the industry through various initiatives to increase its workforce. They offer certifications, conferences and seminars for their members, as well as an apprenticeship program.
ISO
ISO is an international standards organization that develops technical standards to help businesses maintain a high level of quality. This is achieved through voluntary consensus standard, which allows consistency in product.
ANSI
The American National Standards Institute is a trade association that helps businesses with product quality. The American National Standards Institute's main goals are to reduce the risk of a product defect, and increase the efficiency of production.
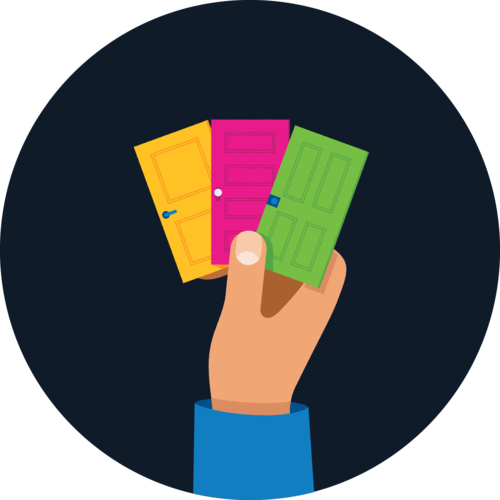
SME
SME is a non-profit organization that focuses primarily on the development of the manufacturing industries. It achieves this through technology, research and educational programs. It also attempts to promote the value and benefit of manufacturing through recognizing its people and the importance it has to society in comparison to other jobs.
MHI
The MHI is a trade association that focuses on material handling, logistics and supply chain management. Its goals include growing and sustaining their industry, improving the health of their members and ensuring that they have access to quality products and services.
FAQ
What is production planning?
Production Planning involves developing a plan for all aspects of the production, including scheduling, budgeting, casting, crew, location, equipment, props, etc. This document aims to ensure that everything is planned and ready when you are ready to shoot. It should also provide information about how best to produce the best results while on set. This information includes locations, crew details and equipment requirements.
The first step in filming is to define what you want. You may already know where you want the film to be shot, or perhaps you have specific locations and sets you wish to use. Once you have identified the scenes and locations, you can start to determine which elements are required for each scene. If you decide you need a car and don't know what model to choose, this could be an example. You could look online for cars to see what options are available, and then narrow down your choices by selecting between different makes or models.
After you have selected the car you want, you can begin to think about additional features. Do you have people who need to be seated in the front seat? Perhaps you have someone who needs to be able to walk around the back of your car. You may want to change the interior's color from black or white. These questions will help determine the look and feel you want for your car. You can also think about the type of shots you want to get. What type of shots will you choose? Perhaps you want to show the engine or the steering wheel? These factors will help you determine which car style you want to film.
Once you have made all the necessary decisions, you can start to create a schedule. You can use a schedule to determine when and where you need it to be shot. Every day will have a time for you to arrive at the location, leave when you are leaving and return home when you are done. This way, everyone knows what they need to do and when. It is possible to make arrangements in advance for additional staff if you are looking to hire. There is no point in hiring someone who won't turn up because you didn't let him know.
Your schedule will also have to be adjusted to reflect the number of days required to film. Some projects may only take a couple of days, while others could last for weeks. When you are creating your schedule, you should always keep in mind whether you need more than one shot per day or not. Multiple takes at the same place will result in higher costs and longer completion times. If you are unsure if you need multiple takes, it is better to err on the side of caution and shoot fewer takes rather than risk wasting money.
Budget setting is another important aspect in production planning. It is important to set a realistic budget so you can work within your budget. Remember that you can always reduce the budget later on if you run into unforeseen problems. But, don't underestimate how much money you'll spend. You will end up spending less money if you underestimate the cost of something.
Production planning is a detailed process. But, once you understand the workings of everything, it becomes easier for future projects to be planned.
What kind of jobs are there in logistics?
Logistics can offer many different jobs. Here are some examples:
-
Warehouse workers – They load and unload pallets and trucks.
-
Transportation drivers - They drive trucks and trailers to deliver goods and carry out pick-ups.
-
Freight handlers are people who sort and pack freight into warehouses.
-
Inventory managers – These people oversee inventory at warehouses.
-
Sales representatives: They sell products to customers.
-
Logistics coordinators: They plan and manage logistics operations.
-
Purchasing agents: They are responsible for purchasing goods and services to support company operations.
-
Customer service representatives - Answer calls and email from customers.
-
Shippers clerks - They process shipping order and issue bills.
-
Order fillers - These people fill orders based on what has been ordered.
-
Quality control inspectors (QCI) - They inspect all incoming and departing products for potential defects.
-
Others – There are many other types available in logistics. They include transport supervisors, cargo specialists and others.
What are the essential elements of running a logistics firm?
It takes a lot of skills and knowledge to run a successful logistics business. You must have good communication skills to interact effectively with your clients and suppliers. You will need to know how to interpret data and draw conclusions. You will need to be able handle pressure well and work in stressful situations. To increase efficiency and creativity, you need to be creative. Strong leadership qualities are essential to motivate your team and help them achieve their organizational goals.
You must be organized to meet tight deadlines.
How can manufacturing avoid production bottlenecks
You can avoid bottlenecks in production by making sure that everything runs smoothly throughout the production cycle, from the moment you receive an order to the moment the product is shipped.
This includes planning for both capacity requirements and quality control measures.
Continuous improvement techniques like Six Sigma are the best way to achieve this.
Six Sigma can be used to improve the quality and decrease waste in all areas of your company.
It emphasizes consistency and eliminating variance in your work.
Statistics
- [54][55] These are the top 50 countries by the total value of manufacturing output in US dollars for its noted year according to World Bank.[56] (en.wikipedia.org)
- Job #1 is delivering the ordered product according to specifications: color, size, brand, and quantity. (netsuite.com)
- According to a Statista study, U.S. businesses spent $1.63 trillion on logistics in 2019, moving goods from origin to end user through various supply chain network segments. (netsuite.com)
- It's estimated that 10.8% of the U.S. GDP in 2020 was contributed to manufacturing. (investopedia.com)
- (2:04) MTO is a production technique wherein products are customized according to customer specifications, and production only starts after an order is received. (oracle.com)
External Links
How To
How to use the Just In-Time Production Method
Just-in time (JIT), is a process that reduces costs and increases efficiency in business operations. It's the process of obtaining the right amount and timing of resources when you need them. This means that you only pay the amount you actually use. Frederick Taylor developed the concept while working as foreman in early 1900s. Taylor observed that overtime was paid to workers if they were late in working. He realized that workers should have enough time to complete their jobs before they begin work. This would help increase productivity.
JIT is about planning ahead. You should have all the necessary resources ready to go so that you don’t waste money. You should also look at the entire project from start to finish and make sure that you have sufficient resources available to deal with any problems that arise during the course of your project. You will have the resources and people to solve any problems you anticipate. This will prevent you from spending extra money on unnecessary things.
There are several types of JIT techniques:
-
Demand-driven: This JIT is where you place regular orders for the parts/materials that are needed for your project. This will allow to track how much material has been used up. You'll also be able to estimate how long it will take to produce more.
-
Inventory-based: This type allows you to stock the materials needed for your projects ahead of time. This allows you to forecast how much you will sell.
-
Project-driven: This is an approach where you set aside enough funds to cover the cost of your project. You will be able to purchase the right amount of materials if you know what you need.
-
Resource-based: This is the most common form of JIT. You assign certain resources based off demand. You will, for example, assign more staff to deal with large orders. If you don't receive many orders, then you'll assign fewer employees to handle the load.
-
Cost-based: This is the same as resource-based except that you don't care how many people there are but how much each one of them costs.
-
Price-based: This is similar to cost-based but instead of looking at individual workers' salaries, you look at the total company price.
-
Material-based: This approach is similar to cost-based. However, instead of looking at the total cost for the company, you look at how much you spend on average on raw materials.
-
Time-based JIT is another form of resource-based JIT. Instead of focusing only on how much each employee is costing, you should focus on how long it takes to complete your project.
-
Quality-based JIT - This is another form of resource-based JIT. Instead of thinking about how much each employee costs or how long it takes to manufacture something, you think about how good the quality of your product is.
-
Value-based JIT: This is the latest form of JIT. In this instance, you are not concerned about the product's performance or meeting customer expectations. Instead, you focus on the added value that you provide to your market.
-
Stock-based is an inventory-based system that measures the number of items produced at any given moment. It is used when production goals are met while inventory is kept to a minimum.
-
Just-in time (JIT), planning: This is a combination JIT/supply chain management. It is the process that schedules the delivery of components within a short time of their order. It's important because it reduces lead times and increases throughput.