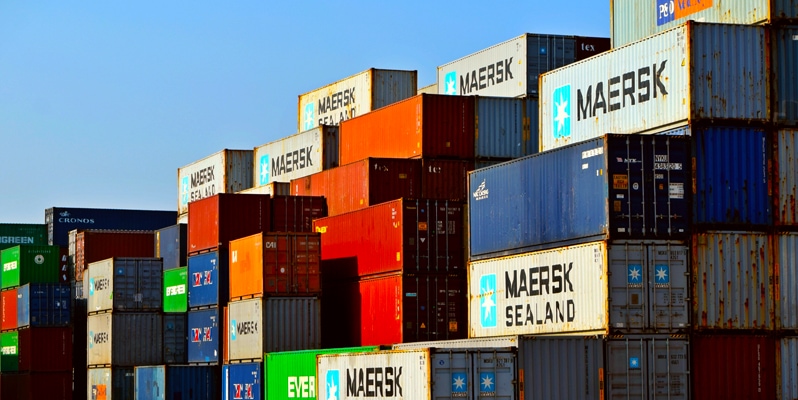
Many opportunities exist for those who are interested in becoming nuclear engineers. There are many roles in the industry, including designing and developing nuclear systems, improving medical equipment, and designing new equipment. The industry is also responsible for decommissioning nuclear power plants.
A nuclear engineer can make a good living, but it all depends on where you are located. In the United States, for example, the average salary is about $106,060. Location and years of experience can impact the salary. The highest-paid nuclear engineers are paid over $143,000 per annum.
Although the nuclear industry has a reputation as a male-dominated field, it doesn't mean that you can't work in it. In fact, major companies have been very proactive in recruiting women and minorities.
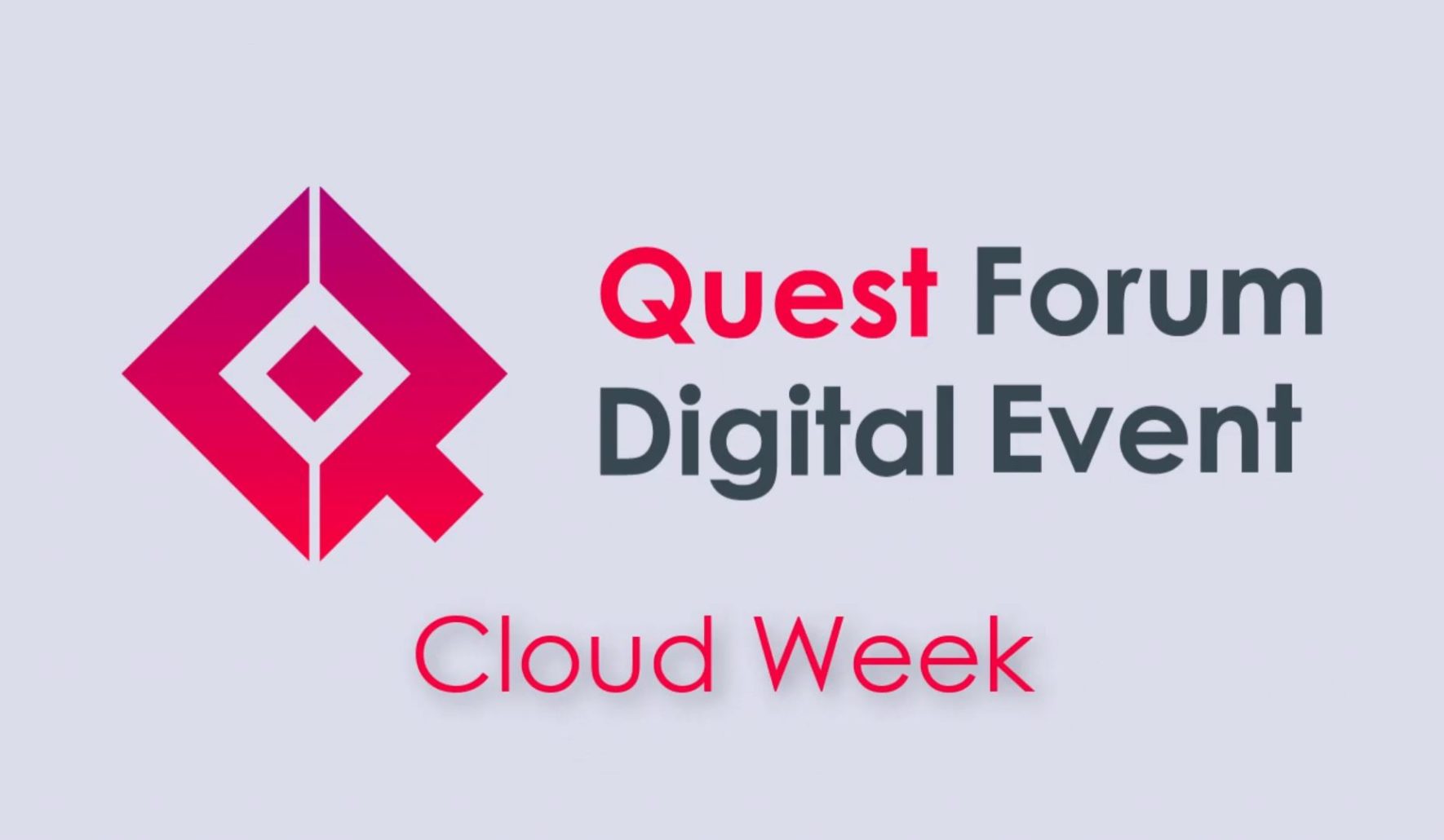
There are many tasks that nuclear engineers have to perform, including the design of nuclear power plants, research into radiation's effects on humans, and overseeing radioactive waste disposal. They also work on pilot projects and may run nuclear power plants. Entry-level positions usually require a bachelor’s degree in nuclear Engineering. A master's degree can open up more doors for those with higher-ranking positions in engineering.
Nuclear engineers must stay abreast with the latest developments, including regulations and laws. Additionally, they must attend regular training sessions to maintain their skills. They could work a standard work schedule or may work overtime.
Most nuclear engineers work at universities or in power plants. You may also find them in an office, or on a construction site. You will need to have strong problem-solving skills, interpersonal skills, logical thinking, and interpersonal skills. The nuclear engineers must also be able to maintain their calm under pressure. There is a zero tolerance for errors, but nuclear engineers are also required to complete a thorough investigation when they make mistakes. They are required to share their lessons with fellow engineers and present their findings in writing to a committee.
In the future, there will be a greater demand for nuclear engineers. According to the future, demand will rise in both medical and research areas as well as technical consultancy services. Over the next decade, however, electric power generation demand is expected to fall.
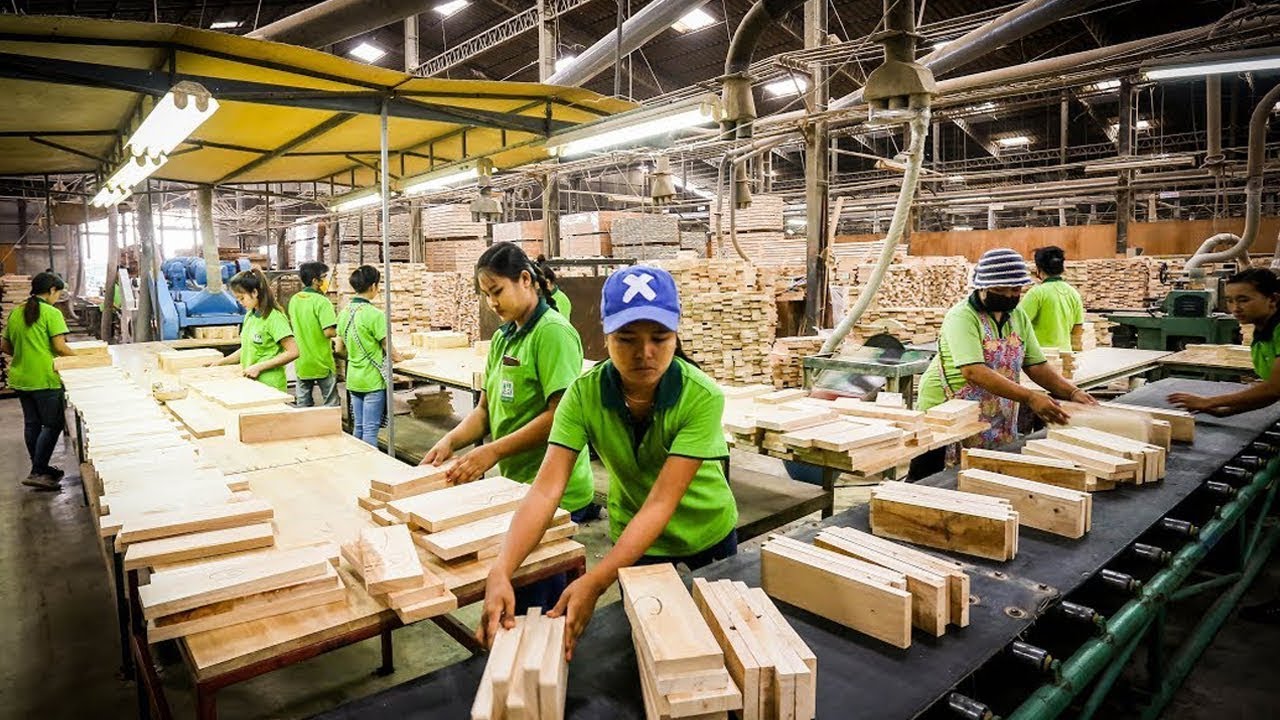
The category Professional, Scientific and Technical Services is the most lucrative for nuclear engineers. The annual salary can go up to $125130. The median annual wage for nuclear engineers can be found in the Occupational Employment Statistics Survey for Nuclear Engineers (OES Survey for Nuclear Engineers) at $120,000. There are also some places where the salary is higher. California has the highest average salary for nuclear engineers at $152,620. San Francisco is the second highest, followed by Bolinas.
A doctorate in nuclear engineer can expect to make mid-to high-$150s. These jobs aren't very common but can be very lucrative. As a PhD nuclear engineer, you can serve as a professor in the US Navy or join a commercial company that produces nuclear power.
FAQ
What are manufacturing and logistics?
Manufacturing is the act of producing goods from raw materials using machines and processes. Logistics is the management of all aspects of supply chain activities, including procurement, production planning, distribution, warehousing, inventory control, transportation, and customer service. Logistics and manufacturing are often referred to as one thing. It encompasses both the creation of products and their delivery to customers.
What is production plan?
Production Planning includes planning for all aspects related to production. It is important to have everything ready and planned before you start shooting. This document should also include information on how to get the best result on set. This information includes locations, crew details and equipment requirements.
The first step is to outline what you want to film. You may already know where you want the film to be shot, or perhaps you have specific locations and sets you wish to use. Once you have identified your locations and scenes it's time to begin figuring out what elements you will need for each one. For example, you might decide that you need a car but don't know exactly what model you want. You could look online for cars to see what options are available, and then narrow down your choices by selecting between different makes or models.
After you've found the perfect car, it's time to start thinking about adding extras. Are you looking for people to sit in the front seats? Maybe you need someone to move around in the back. You may want to change the interior's color from black or white. These questions will help you determine the exact look and feel of your car. The type of shots that you are looking for is another thing to consider. Will you be filming close-ups or wide angles? Maybe you want to show your engine or the steering wheel. This will allow you to determine the type of car you want.
Once you have established all the details, you can create a schedule. You can create a schedule that will outline when you must start and finish your shoots. The schedule will show you when to get there, what time to leave, and when to return home. Everyone knows exactly what they should do and when. If you need to hire extra staff, you can make sure you book them in advance. It's not worth paying someone to show up if you haven't told him.
You will need to factor in the days that you have to film when creating your schedule. Some projects take only a few days while others can last several weeks. When you are creating your schedule, you should always keep in mind whether you need more than one shot per day or not. Multiple shots at the same location can increase costs and make it more difficult to complete. If you are unsure if you need multiple takes, it is better to err on the side of caution and shoot fewer takes rather than risk wasting money.
Budgeting is another important aspect of production planning. As it will allow you and your team to work within your financial means, setting a realistic budget is crucial. Remember that you can always reduce the budget later on if you run into unforeseen problems. It is important to not overestimate how much you will spend. You'll end up with less money after paying for other things if the cost is underestimated.
Production planning is a complicated process. But once you understand how everything works together, it becomes much easier to plan future project.
How is a production manager different from a producer planner?
The major difference between a Production Planner and a Project Manager is that a Project Manager is often the person responsible for organizing and planning the entire project. While a Production Planner is involved mainly in the planning stage,
What is the role of a manager in manufacturing?
A manufacturing manager must ensure that all manufacturing processes are efficient and effective. They should also be aware and responsive to any company problems.
They must also be able to communicate with sales and marketing departments.
They must also keep up-to-date with the latest trends in their field and be able use this information to improve productivity and efficiency.
What skills should a production planner have?
A production planner must be organized, flexible, and able multitask to succeed. It is also important to be able communicate with colleagues and clients.
What are the 7 Rs of logistics?
The acronym 7R's of Logistic is an acronym that stands for seven fundamental principles of logistics management. It was created by the International Association of Business Logisticians and published in 2004 under its "Seven Principles of Logistics Management".
The acronym consists of the following letters:
-
Responsible – ensure that all actions are legal and don't cause harm to anyone else.
-
Reliable - have confidence in the ability to deliver on commitments made.
-
It is reasonable to use resources efficiently and not waste them.
-
Realistic – Consider all aspects, including cost-effectiveness as well as environmental impact.
-
Respectful – Treat others fairly and equitably.
-
You are resourceful and look for ways to save money while increasing productivity.
-
Recognizable - provide customers with value-added services.
What does it take to run a logistics business?
You need to have a lot of knowledge and skills to manage a successful logistic business. You must have good communication skills to interact effectively with your clients and suppliers. You will need to know how to interpret data and draw conclusions. You will need to be able handle pressure well and work in stressful situations. You must be creative and innovative to develop new ideas to improve efficiency. You need to have strong leadership qualities to motivate team members and direct them towards achieving organizational goals.
You should also be organized and efficient to meet tight deadlines.
Statistics
- According to a Statista study, U.S. businesses spent $1.63 trillion on logistics in 2019, moving goods from origin to end user through various supply chain network segments. (netsuite.com)
- According to the United Nations Industrial Development Organization (UNIDO), China is the top manufacturer worldwide by 2019 output, producing 28.7% of the total global manufacturing output, followed by the United States, Japan, Germany, and India.[52][53] (en.wikipedia.org)
- (2:04) MTO is a production technique wherein products are customized according to customer specifications, and production only starts after an order is received. (oracle.com)
- In the United States, for example, manufacturing makes up 15% of the economic output. (twi-global.com)
- In 2021, an estimated 12.1 million Americans work in the manufacturing sector.6 (investopedia.com)
External Links
How To
How to use 5S in Manufacturing to Increase Productivity
5S stands for "Sort", "Set In Order", "Standardize", "Separate" and "Store". Toyota Motor Corporation created the 5S methodology in 1954. It helps companies achieve higher levels of efficiency by improving their work environment.
The basic idea behind this method is to standardize production processes, so they become repeatable, measurable, and predictable. It means tasks like cleaning, sorting or packing, labeling, and storing are done every day. These actions allow workers to perform their job more efficiently, knowing what to expect.
Implementing 5S requires five steps. These are Sort, Set In Order, Standardize. Separate. And Store. Each step requires a different action, which increases efficiency. For example, when you sort things, you make them easy to find later. When you arrange items, you place them together. You then organize your inventory in groups. You can also label your containers to ensure everything is properly labeled.
This requires employees to critically evaluate how they work. Employees must understand why they do certain tasks and decide if there's another way to accomplish them without relying on the old ways of doing things. They will need to develop new skills and techniques in order for the 5S system to be implemented.
The 5S method increases efficiency and morale among employees. As they begin to see improvements, they feel motivated to continue working towards the goal of achieving higher levels of efficiency.