
This article will explain what a biochemical salary is. This article will provide information on biochemical salaries for BOTHELL, WA, and San Mateo CA. Explore the various biochemical salaries options to get started in your career. Youtell Biochemical, Worthington Biochemical have detailed job descriptions and requirements. These companies are both headquartered in BOTHELL, WA and both offer competitive benefits and compensation.
Youtell Biochemical is paying $29 an hour
Youtell Biochemical pays an average of $99,854. Salaries range from $88,159 up to $114,509. However, individual salaries can vary wildly depending on the position, department, education, and skills required. Below are examples showing the types of jobs available and the salaries offered by Youtell Biochemical. The salary ranges are also based on experience and education, so keep this in mind when evaluating salaries.
Youtell Biochemical headquarters are located in BOTHELL WA
Youtell Biochemical is an enzyme product-focused chemical company with headquarters in BOTHELL. They have a state -of-the art biotechnology research center at Bothell, and two downstream process and fermentation plants in China. The enzyme products are produced by these companies using patented technologies. In fact, you can find over 80,000 tons of enzyme products per year produced by Youtell Biochemical at their main campus in BOTHELL, WA.
Worthington Biochemical's headquarters are in San Mateo CA.
Worthington Biochemical was established in 1947. Its founder, Charles Worthington, had worked as a research assistant at the Rockefeller Institute, preparing crystalline enzymes for use in biochemical research. He realized quickly that reliable and high-purity enzymes were crucial for the biochemical research community. It would be difficult to purify them by researchers. Worthington, a New Jersey native, started its own company in Freehold in 1947 to supply these enzymes.
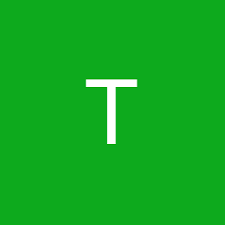
In 1985, Worthington acquired the Clinical Division of Cooper, a biotech firm based in New Jersey. Worthington's acquisition of the Clinical Division of Cooper, a biotech firm based in New Jersey, allowed it to expand its operations and allow it to concentrate more on the lucrative clinic market. The company did not expand into molecular biology or immunology. Instead, it expanded its diagnostic kit manufacturing facility while investing less in enzyme production.
FAQ
What skills are required to be a production manager?
To become a successful production planner, you need to be organized, flexible, and able to multitask. Also, you must be able and willing to communicate with clients and coworkers.
Is it possible to automate certain parts of manufacturing
Yes! Automation has been around since ancient times. The Egyptians invent the wheel thousands of year ago. Today, robots assist in the assembly of lines.
Robotics is used in many manufacturing processes today. These include:
-
Line robots
-
Robot welding
-
Robot painting
-
Robotics inspection
-
Robots that make products
Manufacturing could also benefit from automation in other ways. 3D printing is a way to make custom products quickly and without waiting weeks or months for them to be manufactured.
Is automation important for manufacturing?
Not only are service providers and manufacturers important, but so is automation. It allows them provide faster and more efficient services. It also helps to reduce costs and improve productivity.
What jobs are available in logistics?
There are many jobs available in logistics. Here are some examples:
-
Warehouse workers - They load and unload trucks and pallets.
-
Transportation drivers – These drivers drive trucks and wagons to transport goods and pick up the goods.
-
Freight handlers - They sort and pack freight in warehouses.
-
Inventory managers: They are responsible for the inventory and management of warehouses.
-
Sales reps are people who sell products to customers.
-
Logistics coordinators are responsible for organizing and planning logistics operations.
-
Purchasing agents: They are responsible for purchasing goods and services to support company operations.
-
Customer service representatives are available to answer customer calls and emails.
-
Shipping clerks – They process shipping orders, and issue bills.
-
Order fillers are people who fill orders based only on what was ordered.
-
Quality control inspectors – They inspect incoming and outgoing products to ensure that there are no defects.
-
Other - Logistics has many other job opportunities, including transportation supervisors, logistics specialists, and cargo specialists.
Why automate your warehouse
Modern warehouses are increasingly dependent on automation. Increased demand for efficient and faster delivery has resulted in a rise in e-commerce.
Warehouses need to adapt quickly to meet changing needs. In order to do this, they need to invest in technology. Automation warehouses can bring many benefits. These are some of the benefits that automation can bring to warehouses:
-
Increases throughput/productivity
-
Reduces errors
-
Improves accuracy
-
Safety is boosted
-
Eliminates bottlenecks
-
Companies can scale more easily
-
Workers are more productive
-
Provides visibility into everything that happens in the warehouse
-
Enhances customer experience
-
Improves employee satisfaction
-
This reduces downtime while increasing uptime
-
Quality products delivered on time
-
Human error can be eliminated
-
Assure compliance with regulations
What are the responsibilities of a logistic manager?
A logistics manager ensures that all goods are delivered on time and without damage. This is done using his/her knowledge of the company's products. He/she should also ensure enough stock is available to meet demand.
What is manufacturing and logistics?
Manufacturing is the act of producing goods from raw materials using machines and processes. Logistics covers all aspects involved in managing supply chains, including procurement and production planning. Sometimes manufacturing and logistics are combined to refer to a wider term that includes both the process of creating products as well as their delivery to customers.
Statistics
- In 2021, an estimated 12.1 million Americans work in the manufacturing sector.6 (investopedia.com)
- In the United States, for example, manufacturing makes up 15% of the economic output. (twi-global.com)
- According to the United Nations Industrial Development Organization (UNIDO), China is the top manufacturer worldwide by 2019 output, producing 28.7% of the total global manufacturing output, followed by the United States, Japan, Germany, and India.[52][53] (en.wikipedia.org)
- According to a Statista study, U.S. businesses spent $1.63 trillion on logistics in 2019, moving goods from origin to end user through various supply chain network segments. (netsuite.com)
- [54][55] These are the top 50 countries by the total value of manufacturing output in US dollars for its noted year according to World Bank.[56] (en.wikipedia.org)
External Links
How To
How to use Lean Manufacturing in the production of goods
Lean manufacturing is an approach to management that aims for efficiency and waste reduction. It was developed in Japan between 1970 and 1980 by Taiichi Ohno. TPS founder Kanji Tyoda gave him the Toyota Production System, or TPS award. Michael L. Watkins published the "The Machine That Changed the World", the first book about lean manufacturing. It was published in 1990.
Lean manufacturing is often defined as a set of principles used to improve the quality, speed, and cost of products and services. It emphasizes the elimination of defects and waste throughout the value stream. Lean manufacturing is called just-in-time (JIT), zero defect, total productive maintenance (TPM), or 5S. Lean manufacturing emphasizes reducing non-value-added activities like inspection, rework and waiting.
In addition to improving product quality and reducing costs, lean manufacturing helps companies achieve their goals faster and reduces employee turnover. Lean manufacturing has been deemed one of the best ways to manage the entire value-chain, including customers, distributors as well retailers and employees. Lean manufacturing can be found in many industries. Toyota's philosophy is a great example of this. It has helped to create success in automobiles as well electronics, appliances and healthcare.
Five fundamental principles underlie lean manufacturing.
-
Define value - Find out what your business contributes to society, and what makes it different from other competitors.
-
Reduce Waste - Eliminate any activity that doesn't add value along the supply chain.
-
Create Flow - Ensure work moves smoothly through the process without interruption.
-
Standardize and simplify – Make processes as repeatable and consistent as possible.
-
Develop Relationships: Establish personal relationships both with internal and external stakeholders.
Lean manufacturing is not a new concept, but it has been gaining popularity over the last few years due to a renewed interest in the economy following the global financial crisis of 2008. To increase their competitiveness, many businesses have turned to lean manufacturing. Economists think that lean manufacturing is a crucial factor in economic recovery.
With many benefits, lean manufacturing is becoming more common in the automotive industry. These include better customer satisfaction and lower inventory levels. They also result in lower operating costs.
You can apply Lean Manufacturing to virtually any aspect of your organization. This is because it ensures efficiency and effectiveness in all stages of the value chain.
There are three main types of lean manufacturing:
-
Just-in Time Manufacturing (JIT), also known as "pull system": This form of lean manufacturing is often referred to simply as "pull". JIT means that components are assembled at the time of use and not manufactured in advance. This approach reduces lead time, increases availability and reduces inventory.
-
Zero Defects Manufacturing (ZDM),: ZDM is a system that ensures no defective units are left the manufacturing facility. You should repair any part that needs to be repaired during an assembly line. This is true even for finished products that only require minor repairs prior to shipping.
-
Continuous Improvement (CI),: Continuous improvement aims improve the efficiency and effectiveness of operations by continuously identifying issues and making changes to reduce waste. Continuous improvement involves continuous improvement of processes and people as well as tools.