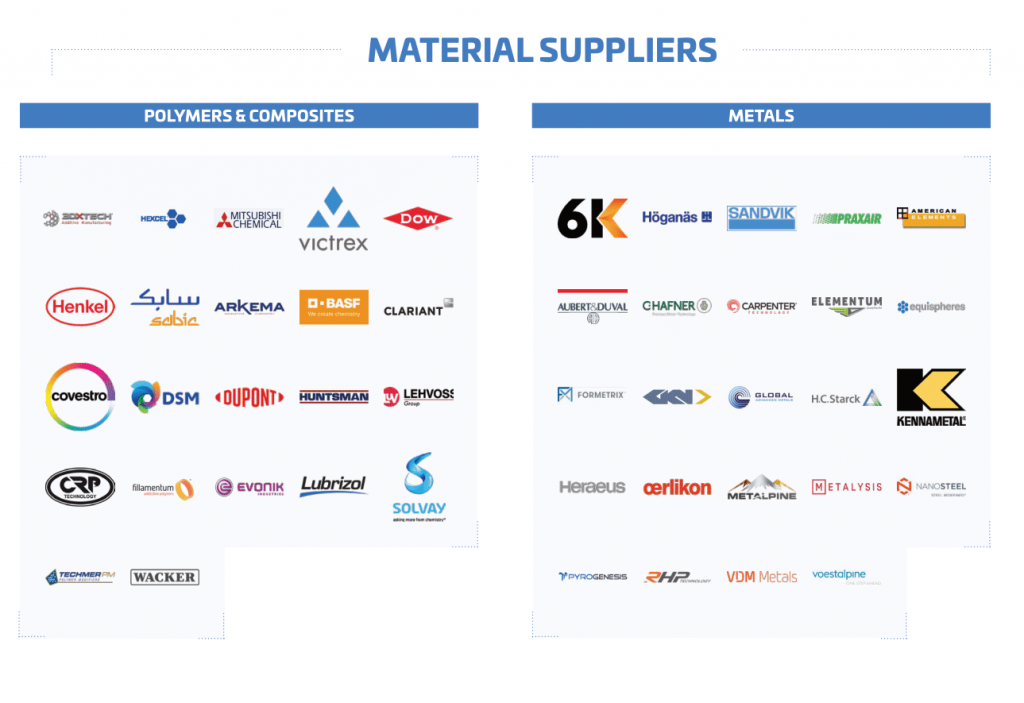
OEE stands to represent Overall Equipment Effectiveness. This is a measure that can be used to evaluate the equipment's performance. This article explains the definition and calculates OEE. It is best practice and based on availability, performance, quality. OEE can be used to increase the efficiency of manufacturing operations, by decreasing downtime and increasing production. It also helps manufacturers save money.
OEE can be described as a labor efficiency metric.
OEE is a metric that measures overall production quality. It is dependent on the interaction between quality, availability, production performance. OEE refers to time lost because of incontinence in production. These include lost time, rate loss in the process, scrap and rework during operative mode.
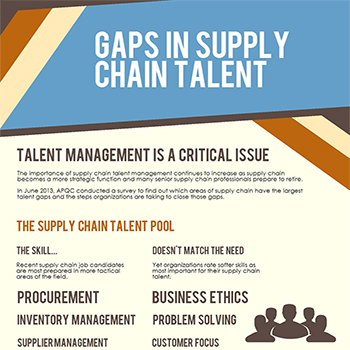
It is based Availability, Performance, Quality
OEE (Optimum Equipment Efficiency) is a production management strategy that emphasizes quality, performance, and availability. The availability of a product/service is the period that it is available for sale. It can be, for example, the time period between delivery to a customer, recovery, or the time between scrapping, repair, and delivery. Performance directly relates to the quality and performance of a business. The best way to gauge performance is to have a professional company assess your business and give you suggestions for improvement.
It is a best practices measure
OEE is an excellent tool to measure and improve your operations. This metric allows you to analyze different levels of your operations, which can help you reduce waste and improve your operations. However, it is important to note that it cannot be used as an end-all-be-all metric. This means that you should not start an OEE improvement program without carefully piloting it first.
It is a directional measurement
OEE, in addition to being a directional measure that allows you to compare the performance across similar types of machines within a company, is also defined. Companies can gauge if their machines have become more efficient by continuously measuring this metric across all of their machines.
It is a TPM metric
For analyzing production efficiency, the overall equipment effectiveness (OEE metric) is an important tool. It measures inefficiencies and losses in three areas: availability, performance, quality. It can also be used to track progress and identify areas where improvement is needed.
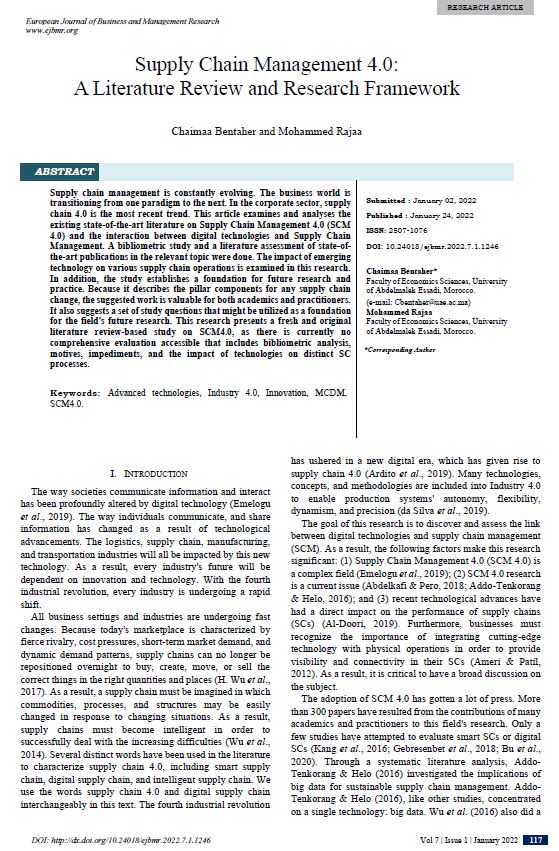
It is a manufacturing best practice
OEE stands for overall equipment effectiveness. OEE is the ratio between what a machine/cell can produce in a certain time and how long it takes to actually produce that product. It is important to minimize downtime and maximize OEE. As a result, manufacturing operations can improve quality and reduce costs.
FAQ
Why automate your warehouse?
Modern warehousing has seen automation take center stage. E-commerce has brought increased demand for more efficient and quicker delivery times.
Warehouses must adapt quickly to meet changing customer needs. They must invest heavily in technology to do this. Automation warehouses can bring many benefits. Here are some of the reasons automation is worth your investment:
-
Increases throughput/productivity
-
Reduces errors
-
Increases accuracy
-
Safety is boosted
-
Eliminates bottlenecks
-
Allows companies to scale more easily
-
It makes workers more efficient
-
It gives visibility to everything that happens inside the warehouse
-
Enhances customer experience
-
Improves employee satisfaction
-
Reduces downtime and improves uptime
-
This ensures that quality products are delivered promptly
-
Removes human error
-
It helps ensure compliance with regulations
What are manufacturing and logistics?
Manufacturing refers to the process of making goods using raw materials and machines. Logistics manages all aspects of the supply chain, including procurement, production planning and distribution, inventory control, transportation, customer service, and transport. Manufacturing and logistics can often be grouped together to describe a larger term that covers both the creation of products, and the delivery of them to customers.
What are the 7 Rs of logistics?
The acronym 7R's of Logistic is an acronym that stands for seven fundamental principles of logistics management. It was developed and published by the International Association of Business Logisticians in 2004 as part of the "Seven Principles of Logistics Management".
The following letters form the acronym:
-
Responsible - to ensure that all actions are within the legal requirements and are not detrimental to others.
-
Reliable: Have faith in your ability or the ability to honor any promises made.
-
Use resources effectively and sparingly.
-
Realistic - Take into consideration all aspects of operations including cost-effectiveness, environmental impact, and other factors.
-
Respectful - treat people fairly and equitably.
-
Reliable - Find ways to save money and increase your productivity.
-
Recognizable is a company that provides customers with value-added solutions.
How can manufacturing prevent production bottlenecks?
The key to avoiding bottlenecks in production is to keep all processes running smoothly throughout the entire production cycle, from the time you receive an order until the time when the product ships.
This includes both quality control and capacity planning.
Continuous improvement techniques such Six Sigma are the best method to accomplish this.
Six Sigma Management System is a method to increase quality and reduce waste throughout your organization.
It emphasizes consistency and eliminating variance in your work.
What does it take to run a logistics business?
To run a successful logistics company, you need a lot knowledge and skills. For clients and suppliers to be successful, you need to have excellent communication skills. You need to understand how to analyze data and draw conclusions from it. You must be able and able to handle stress situations and work under pressure. You must be creative and innovative to develop new ideas to improve efficiency. To motivate and guide your team towards reaching organizational goals, you must have strong leadership skills.
It is also important to be efficient and well organized in order meet deadlines.
Statistics
- It's estimated that 10.8% of the U.S. GDP in 2020 was contributed to manufacturing. (investopedia.com)
- In 2021, an estimated 12.1 million Americans work in the manufacturing sector.6 (investopedia.com)
- According to the United Nations Industrial Development Organization (UNIDO), China is the top manufacturer worldwide by 2019 output, producing 28.7% of the total global manufacturing output, followed by the United States, Japan, Germany, and India.[52][53] (en.wikipedia.org)
- [54][55] These are the top 50 countries by the total value of manufacturing output in US dollars for its noted year according to World Bank.[56] (en.wikipedia.org)
- According to a Statista study, U.S. businesses spent $1.63 trillion on logistics in 2019, moving goods from origin to end user through various supply chain network segments. (netsuite.com)
External Links
How To
How to Use the 5S to Increase Productivity In Manufacturing
5S stands for "Sort", "Set In Order", "Standardize", "Separate" and "Store". Toyota Motor Corporation created the 5S methodology in 1954. This methodology helps companies improve their work environment to increase efficiency.
This method aims to standardize production processes so that they are repeatable, measurable and predictable. This means that daily tasks such as cleaning and sorting, storage, packing, labeling, and packaging are possible. This knowledge allows workers to be more efficient in their work because they are aware of what to expect.
Implementing 5S requires five steps. These are Sort, Set In Order, Standardize. Separate. And Store. Each step requires a different action to increase efficiency. If you sort items, it makes them easier to find later. You arrange items by placing them in an order. Then, after you separate your inventory into groups, you store those groups in containers that are easy to access. Make sure everything is correctly labeled when you label your containers.
Employees will need to be more critical about their work. Employees need to understand the reasons they do certain jobs and determine if there is a better way. They must learn new skills and techniques in order to implement the 5S system.
The 5S method increases efficiency and morale among employees. Once they start to notice improvements, they are motivated to keep working towards their goal of increasing efficiency.