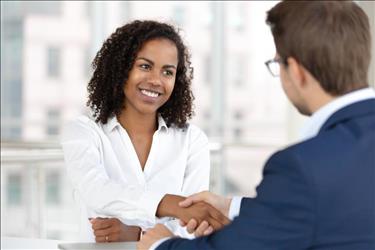
The purchase and delivery management of materials is the responsibility of a material manager. They come typically from inventory or material management. It is important that they are knowledgeable about the types of raw material required to produce a product. They should be resourceful in locating these materials. They should also have strong relationships with vendors to get the best price and delivery rates. Materials managers also earn a significant salary. These are some tips to help get the job.
Job description
A materials manager oversees the purchasing and stock management. A materials manager must be able to solve problems and have a good understanding of stock management. The job description of a material manager includes the management of inventory, budgets and efficiencies. Besides managing inventory, this position also has to coordinate the supply chain and supervise subordinates. This role requires an advanced degree. Materials managers must also have experience in similar roles.
A materials manager typically has a bachelor's degree, usually in business administration. A master's degree in the same field is helpful if the position calls for a supervisor. Although an advanced degree may be more useful than on the job experience, education can also be beneficial. A materials manager must have at least three years experience in an industrial or manufacturing setting before applying to a managerial job.
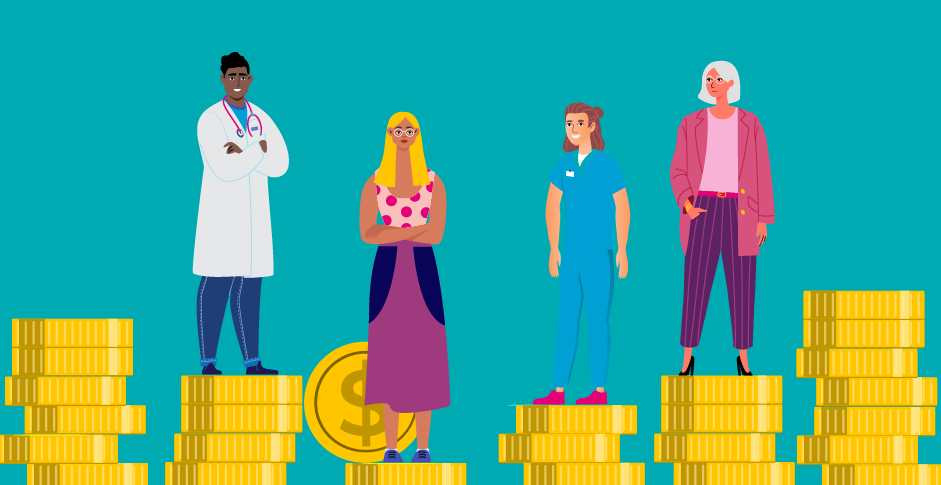
Responsibilities
Materials managers are responsible for evaluating projects and determining the materials that will be required to produce finished products. He or she also keeps track of inventory through the company's supply chain management system, and may be responsible for maintaining stock of spare parts for repairing faulty products. He or she may also be responsible in training employees about the proper use of inventory management systems. These positions are vital in many companies, but not all of them require extensive training.
Job description: A material manager oversees the procurement of materials for a company. The material manager also oversees the distribution and storage of these materials. This job requires knowledge in logistics, supply chain management, inventory control, as well as logistics. Those with experience in these areas will have an advantage. They will also work closely with the purchasing department, vendors, and production departments to determine requirements and plan distribution. These positions require a bachelor’s degree in business as well as a strong analytical mind.
Education necessary
It is important to understand the requirements for material managers if you are interested in a career. This position requires excellent management skills as well as a thorough understanding of logistics. As a material manger, you will work closely with QC employees and higher-ranking management. You will be responsible for planning and delegating work. You should be able assess the performance of subordinates and foster harmonious working relationships.
Materials managers should have a Bachelor's degree. In addition, some companies require two to three years of experience as a material manager before hiring someone with that educational background. Higher-level positions may require additional education. Many material managers have certifications such as the American Purchasing Society (CPSCP), and the APICS (Association of Purchasing Professionals).
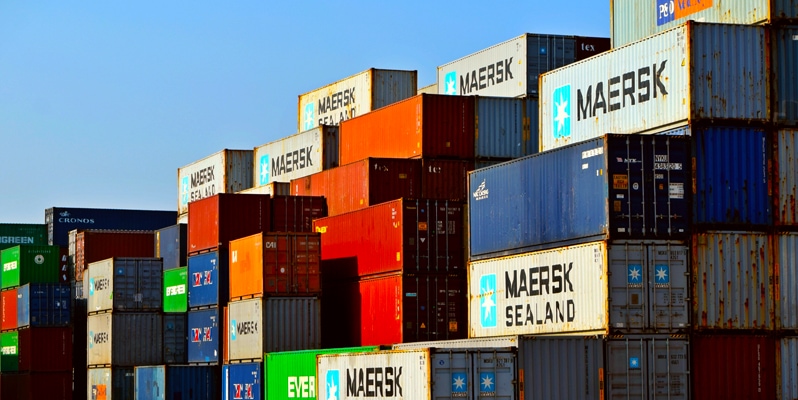
Salary
The average annual salary for a Materials Manager is around $78,500. This number is based on the salaries of 106 TurboTax users. This includes tips and bonuses, taxable wages, and taxable wages. The exact salary will vary depending on education and experience. Salary data is adjusted to reflect inflation each year. You can read the following to learn about the average salary for a Materials Manager job.
You will need to have some management experience in order to be a materials manager. An understanding of logistics, receipt, and shipping are essential. A basic understanding of the industry is necessary if you plan to work for a manufacturing company. This will allow your to negotiate the best possible prices with suppliers. A materials manager's salary will likely depend on the type of experience and training they have.
FAQ
How is a production manager different from a producer planner?
The primary difference between a producer planner and a manager of a project is that the manager usually plans and organizes the whole project, while a production planner is only involved in the planning stage.
What type of jobs is there in logistics
There are many types of jobs in logistics. Some examples are:
-
Warehouse workers - They load trucks and pallets.
-
Transportation drivers: They drive trucks and trailers and deliver goods and make pick-ups.
-
Freight handlers are people who sort and pack freight into warehouses.
-
Inventory managers - They oversee the inventory of goods in warehouses.
-
Sales representatives: They sell products to customers.
-
Logistics coordinators are responsible for organizing and planning logistics operations.
-
Purchasing agents - They buy goods and services that are necessary for company operations.
-
Customer service representatives - They answer calls and emails from customers.
-
Shippers clerks - They process shipping order and issue bills.
-
Order fillers - They fill orders based on what is ordered and shipped.
-
Quality control inspectors are responsible for inspecting incoming and outgoing products looking for defects.
-
Others - There is a variety of other jobs in logistics. These include transportation supervisors and cargo specialists.
What is the best way to learn about manufacturing?
You can learn the most about manufacturing by getting involved in it. You can read books, or watch instructional videos if you don't have the opportunity to do so.
Statistics
- According to a Statista study, U.S. businesses spent $1.63 trillion on logistics in 2019, moving goods from origin to end user through various supply chain network segments. (netsuite.com)
- In the United States, for example, manufacturing makes up 15% of the economic output. (twi-global.com)
- Job #1 is delivering the ordered product according to specifications: color, size, brand, and quantity. (netsuite.com)
- In 2021, an estimated 12.1 million Americans work in the manufacturing sector.6 (investopedia.com)
- [54][55] These are the top 50 countries by the total value of manufacturing output in US dollars for its noted year according to World Bank.[56] (en.wikipedia.org)
External Links
How To
How to use the Just-In Time Method in Production
Just-intime (JIT), a method used to lower costs and improve efficiency in business processes, is called just-in-time. It's the process of obtaining the right amount and timing of resources when you need them. This means that you only pay for what you actually use. Frederick Taylor was the first to coin this term. He developed it while working as a foreman during the early 1900s. Taylor observed that overtime was paid to workers if they were late in working. He concluded that if workers were given enough time before they start work, productivity would increase.
JIT teaches you to plan ahead and prepare everything so you don’t waste time. It is important to look at your entire project from beginning to end and ensure that you have enough resources to handle any issues that may arise. You can anticipate problems and have enough equipment and people available to fix them. You won't have to pay more for unnecessary items.
There are several types of JIT techniques:
-
Demand-driven JIT: You order the parts and materials you need for your project every other day. This will allow you to track how much material you have left over after using it. This will let you know how long it will be to produce more.
-
Inventory-based: This is a type where you stock the materials required for your projects in advance. This allows you to predict how much you can expect to sell.
-
Project-driven: This approach involves setting aside sufficient funds to cover your project's costs. Once you have an idea of how much material you will need, you can purchase the necessary materials.
-
Resource-based JIT: This type of JIT is most commonly used. This is where you assign resources based upon demand. For example, if there is a lot of work coming in, you will have more people assigned to them. You'll have fewer orders if you have fewer.
-
Cost-based: This is a similar approach to resource-based but you are not only concerned with how many people you have, but also how much each one costs.
-
Price-based: This is similar to cost-based but instead of looking at individual workers' salaries, you look at the total company price.
-
Material-based - This is a variant of cost-based. But instead of looking at the total company cost, you focus on how much raw material you spend per year.
-
Time-based: This is another variation of resource-based JIT. Instead of worrying about how much each worker costs, you can focus on how long the project takes.
-
Quality-based JIT: This is another variation of resource based JIT. Instead of focusing on the cost of each worker or how long it takes, think about how high quality your product is.
-
Value-based JIT : This is the newest type of JIT. In this scenario, you're not concerned about how products perform or whether customers expect them to meet their expectations. Instead, your goal is to add value to the market.
-
Stock-based: This is an inventory-based method that focuses on the actual number of items being produced at any given time. It is used when production goals are met while inventory is kept to a minimum.
-
Just-intime (JIT), planning is a combination JIT management and supply chain management. It refers to the process of scheduling the delivery of components as soon as they are ordered. It's important because it reduces lead times and increases throughput.