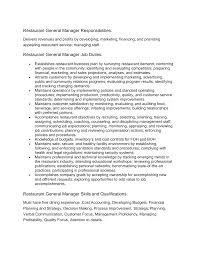
The best books in lean manufacturing provide industry managers with essential guidance. This bestselling book covers many concepts, including how to improve business processes and reduce costs while improving quality. The book includes step-by-step instructions and detailed drawings that make it easy to implement. This book includes information on the many tools that can be used for lean manufacturing.
The book provides a comprehensive overview of Toyota's global success and the Toyota production system. It also explains Toyota's motivation, problem-solving and management style. It also provides information about the success of Toyota's Lean strategy and explains the 14 management principles that form the foundation of Toyota's business practices. The book also contains a chapter on Toyota's involvement in the automotive market, which includes a section on Toyota using lean principles within the automotive sector.
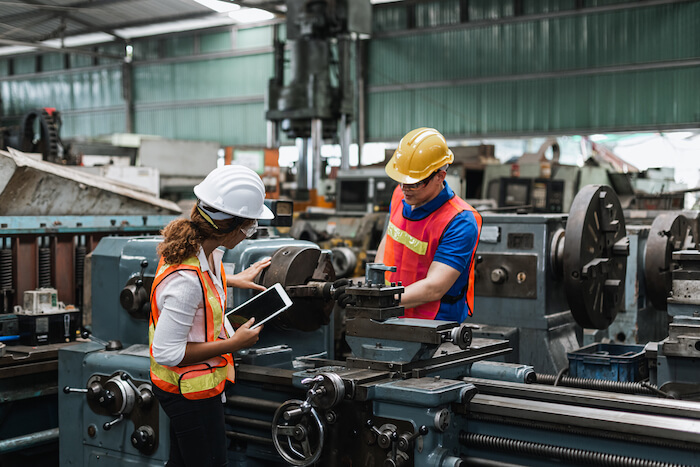
Lean manufacturing is a process of manufacturing that strives to improve the quality and efficiency of the products and services a company produces. Lean manufacturing aims to reduce waste, improve efficiency and eliminate errors. High-skilled people and machines are key to successful manufacturing processes. These interactions account for the majority of a manufacturing company's costs.
The Lean Manufacturing Tool Book and The Toyota Way: 14 Management Principles that Improve Quality and Productivity are the top three best books on lean manufacturing. These books include a comprehensive explanation about the Toyota production process and practical tips. They also provide step-by-step guidance for applying Lean techniques anywhere there is a manufacturing environment. The Lean Manufacturing Tool Book is a complete guide to the tools used in the Lean manufacturing process. The book provides expert advice to help you choose the right tool and lists the available tools. The book also explains Lean manufacturing concepts like Six Sigma and Lean Problem Solving.
The Toyota Way was one of the first books to introduce Lean manufacturing. It focuses on Toyota's management principles and discusses how to implement them within your own organization. It also features company profiles and the principles that have made Toyota's success possible. It also includes a new afterword that discusses the impact of Lean on the manufacturing industry since the publication of the book. It provides new frameworks to improve quality and reduce costs, as well as updated production processes.
The Machine that Changed the World - How Lean Changed the World - This book was the first to fully explain the Toyota Production System, and the impact it had on the manufacturing industry. This book was published in 1990. It provides an overview and context of the system. The book includes a revised introduction and an updated afterword to provide a better understanding about the Toyota Production System as well as its impact on global manufacturing. It also explains the foundational ideas that drive all Lean practices today.
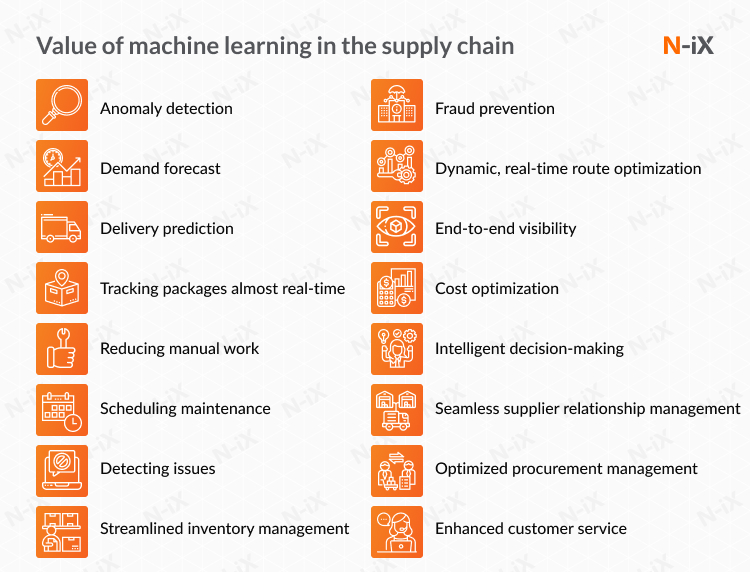
The Toyota Kata: Flow-Focused Manufacturing Methodology is another important book. It describes how Toyota works closely with customers to deliver quality products and services. It explains Toyota's commitment in quality, problem-solving and speeding business processes. It also describes how Toyota chooses and hires employees, and how they are motivated and inspired to provide high-quality products and services.
FAQ
Is it necessary to be familiar with Manufacturing Processes before we learn about Logistics.
No. No. However, knowing about manufacturing processes will definitely give you a better understanding of how logistics works.
How can we reduce manufacturing overproduction?
It is essential to find better ways to manage inventory to reduce overproduction. This would reduce time spent on activities such as purchasing, stocking, and maintaining excess stock. By doing this, we could free up resources for other productive tasks.
This can be done by using a Kanban system. A Kanban board can be used to monitor work progress. Kanban systems allow work items to move through different states until they reach their final destination. Each state represents a different priority.
When work is completed, it can be transferred to the next stage. It is possible to keep a task in the beginning stages until it gets to the end.
This keeps work moving and ensures no work is lost. Managers can monitor the work being done by Kanban boards to see what is happening at any given time. This data allows them adjust their workflow based upon real-time data.
Lean manufacturing, another method to control inventory levels, is also an option. Lean manufacturing emphasizes eliminating waste in all phases of production. Anything that doesn't add value to the product is considered waste. These are some of the most common types.
-
Overproduction
-
Inventory
-
Unnecessary packaging
-
Materials in excess
These ideas will help manufacturers increase efficiency and lower costs.
What are the responsibilities of a logistic manager?
Logistics managers make sure all goods are delivered on schedule and without damage. This is achieved by using their knowledge and experience with the products of the company. He/she should make sure that enough stock is on hand to meet the demands.
Statistics
- (2:04) MTO is a production technique wherein products are customized according to customer specifications, and production only starts after an order is received. (oracle.com)
- [54][55] These are the top 50 countries by the total value of manufacturing output in US dollars for its noted year according to World Bank.[56] (en.wikipedia.org)
- According to a Statista study, U.S. businesses spent $1.63 trillion on logistics in 2019, moving goods from origin to end user through various supply chain network segments. (netsuite.com)
- In the United States, for example, manufacturing makes up 15% of the economic output. (twi-global.com)
- You can multiply the result by 100 to get the total percent of monthly overhead. (investopedia.com)
External Links
How To
How to Use the 5S to Increase Productivity In Manufacturing
5S stands in for "Sort", the "Set In Order", "Standardize", or "Separate". Toyota Motor Corporation was the first to develop the 5S approach in 1954. It improves the work environment and helps companies to achieve greater efficiency.
The basic idea behind this method is to standardize production processes, so they become repeatable, measurable, and predictable. This means that tasks such as cleaning, sorting, storing, packing, and labeling are performed daily. Because workers know what they can expect, this helps them perform their jobs more efficiently.
There are five steps to implementing 5S, including Sort, Set In Order, Standardize, Separate and Store. Each step involves a different action which leads to increased efficiency. By sorting, for example, you make it easy to find the items later. When items are ordered, they are put together. You then organize your inventory in groups. Labeling your containers will ensure that everything is correctly labeled.
Employees need to reflect on how they do their jobs. Employees need to understand the reasons they do certain jobs and determine if there is a better way. They will need to develop new skills and techniques in order for the 5S system to be implemented.
In addition to increasing efficiency, the 5S method also improves morale and teamwork among employees. They are more motivated to achieve higher efficiency levels as they start to see improvement.