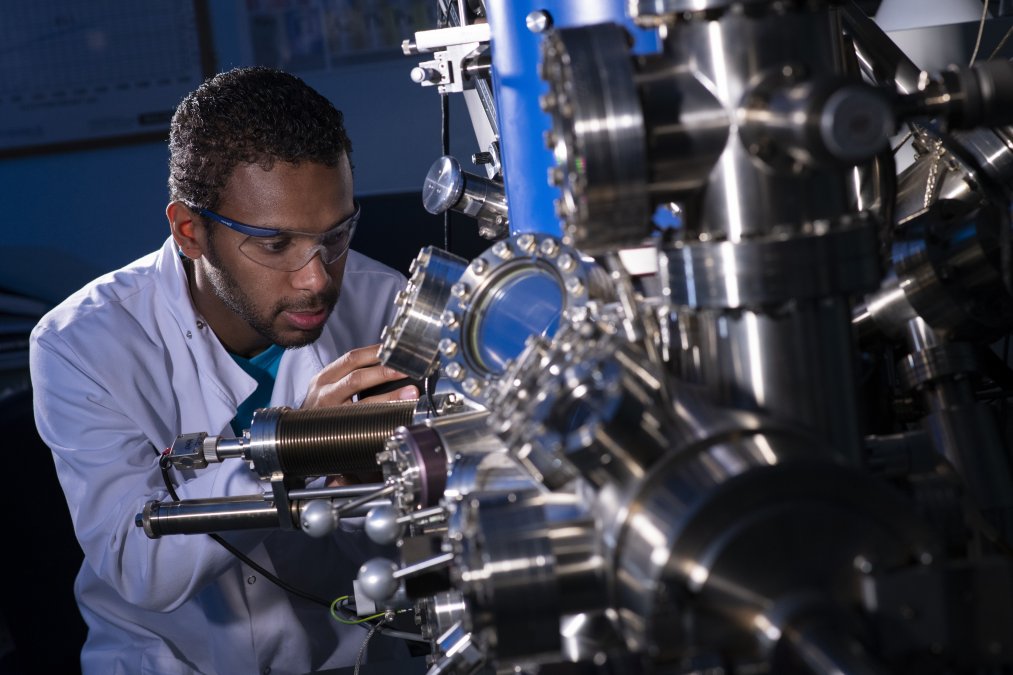
Using cellular manufacturing, a production line is divided into segments that each produce a certain component of the finished product. This helps to minimize waste and to decrease lead times. A cellular manufacturing system can be implemented in many different ways. While some methods are simpler, others require complicated computer models. Cellular manufacturing forms a sub-section of the lean manufacturing movement.
Cellular manufacturing, an innovative and highly efficient process, can help lower the cost and time it takes to produce parts. The goal of cellular manufacturing is to get products through the production process as quickly as possible and minimize waste. Cellular manufacturing also addresses issues of group cohesiveness and self-management, as well as issues of employee input and supervision. Cellular manufacturing provides more flexibility and can help companies meet customer needs. It has been proven that cellular manufacturing can also improve productivity.
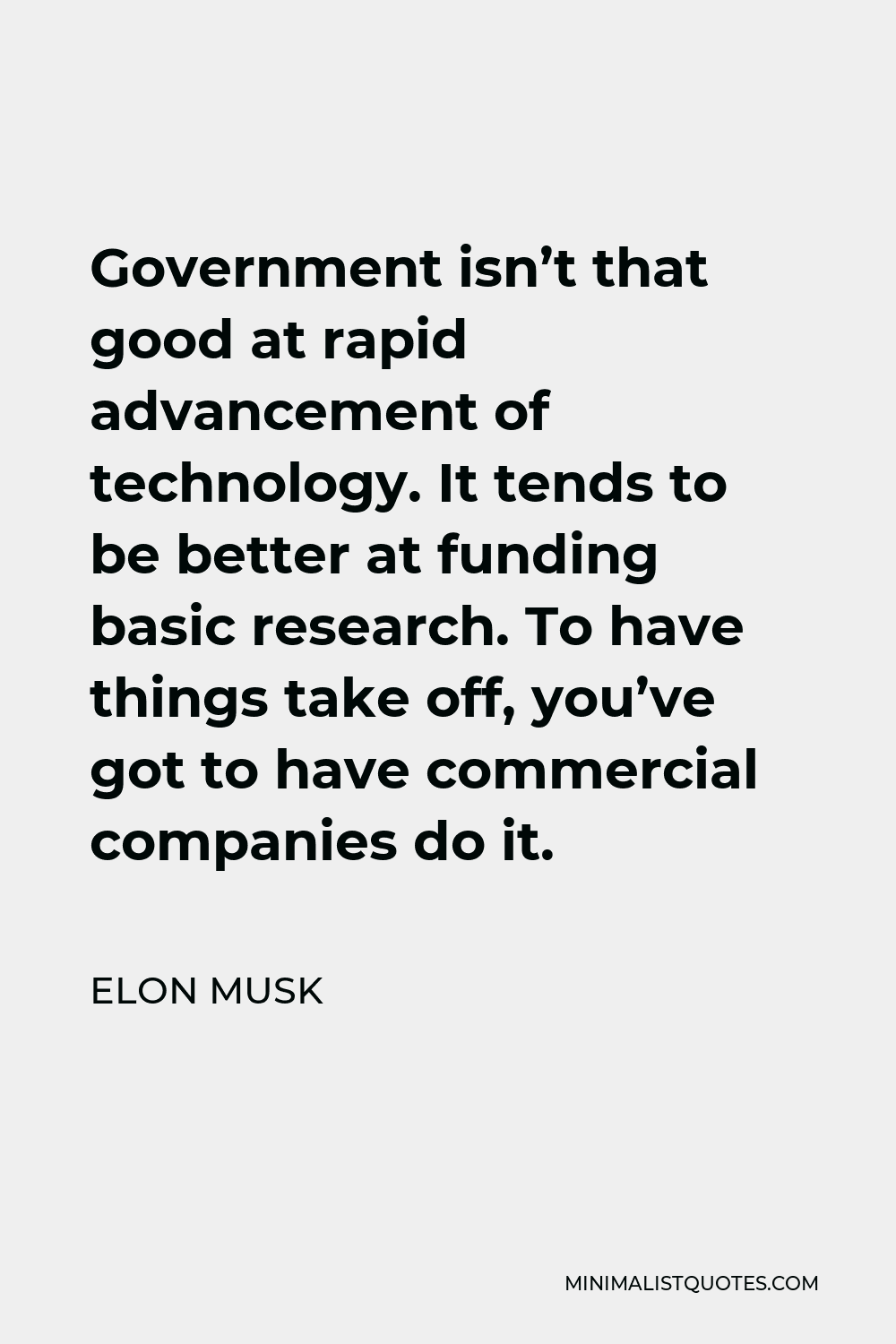
Cellular manufacturing can take many forms, including simple analysis like production flow analysis or more complex computer models. The goal of cellular manufacturing is to produce identical products at the same moment, which minimizes wasteful motions.
The overall takt time can be affected by the layout of the cell. Depending on the cells' design, motion can be reduced from non-value added to value added, reducing cycle time. Some cells are designed in a U-shape to allow operators to move more quickly from one machine to another. Others cells can be set up in a Z-shape which allows workers to work around heavy machinery. These designs are particularly effective for organizations that manufacture a variety of products.
The first step in creating a cell is identifying the products to be made in the cell. This can be accomplished with a processmap, which will allow you to calculate the production rate. Engineers need to determine the number and process steps of the workcell in order to create it. Next, determine what tools and equipment are needed in the cell. Modern work cells take into account the steps involved and the types of holding bins. They also take into consideration how many steps each machine will require. Which layout is best will depend on the physical structure of your cell.
Cellular manufacturing is only as successful as its layout. Cell design can affect how much motion is lost and how many waste products are created. It can also influence fatigue. Cellular manufacturing not only reduces motion, but can also improve process efficiency as well as quality. Cellular layout can make it easier to spot defects and minimize waste.
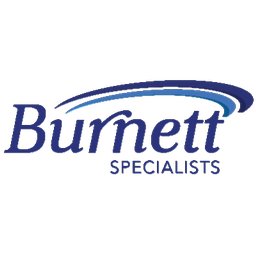
Some of the most common layouts include a U, Z, and S. The Z-shape is most commonly used to work around machines, while the S-shape is used to create cells that process parts one at a time. S-shaped cells are also useful for overcoming obstructions. The layout of cells can be customized, and different cells can be reconfigured to meet the requirements of different parts of the factory.
FAQ
What is the difference between a production planner and a project manager?
A production planner is more involved in the planning phase of the project than a project manger.
What skills are required to be a production manager?
To become a successful production planner, you need to be organized, flexible, and able to multitask. You must also be able to communicate effectively with clients and colleagues.
How can manufacturing excess production be decreased?
The key to reducing overproduction lies in developing better ways to manage inventory. This would reduce the time needed to manage inventory. This will allow us to free up resources for more productive tasks.
Kanban systems are one way to achieve this. A Kanban Board is a visual display that tracks work progress. In a Kanban system, work items move through a sequence of states until they reach their final destination. Each state is assigned a different priority.
When work is completed, it can be transferred to the next stage. It is possible to keep a task in the beginning stages until it gets to the end.
This allows work to move forward and ensures that no work is missed. Managers can monitor the work being done by Kanban boards to see what is happening at any given time. This information allows managers to adjust their workflow based off real-time data.
Lean manufacturing can also be used to reduce inventory levels. Lean manufacturing works to eliminate waste throughout every stage of the production chain. Anything that does not contribute to the product's value is considered waste. There are several types of waste that you might encounter:
-
Overproduction
-
Inventory
-
Unnecessary packaging
-
Exceed materials
Manufacturers can reduce their costs and improve their efficiency by using these ideas.
Statistics
- (2:04) MTO is a production technique wherein products are customized according to customer specifications, and production only starts after an order is received. (oracle.com)
- Job #1 is delivering the ordered product according to specifications: color, size, brand, and quantity. (netsuite.com)
- According to a Statista study, U.S. businesses spent $1.63 trillion on logistics in 2019, moving goods from origin to end user through various supply chain network segments. (netsuite.com)
- According to the United Nations Industrial Development Organization (UNIDO), China is the top manufacturer worldwide by 2019 output, producing 28.7% of the total global manufacturing output, followed by the United States, Japan, Germany, and India.[52][53] (en.wikipedia.org)
- [54][55] These are the top 50 countries by the total value of manufacturing output in US dollars for its noted year according to World Bank.[56] (en.wikipedia.org)
External Links
How To
How to Use lean manufacturing in the Production of Goods
Lean manufacturing is a management style that aims to increase efficiency and reduce waste through continuous improvement. It was developed in Japan between 1970 and 1980 by Taiichi Ohno. TPS founder Kanji Tyoda gave him the Toyota Production System, or TPS award. Michael L. Watkins published the original book on lean manufacturing, "The Machine That Changed the World," in 1990.
Lean manufacturing can be described as a set or principles that are used to improve quality, speed and cost of products or services. It emphasizes eliminating waste and defects throughout the value stream. Lean manufacturing is called just-in-time (JIT), zero defect, total productive maintenance (TPM), or 5S. Lean manufacturing focuses on eliminating non-value-added activities such as rework, inspection, and waiting.
Lean manufacturing can help companies improve their product quality and reduce costs. Additionally, it helps them achieve their goals more quickly and reduces employee turnover. Lean manufacturing has been deemed one of the best ways to manage the entire value-chain, including customers, distributors as well retailers and employees. Lean manufacturing can be found in many industries. Toyota's philosophy, for example, is what has enabled it to be successful in electronics, automobiles, medical devices, healthcare and chemical engineering as well as paper and food.
Lean manufacturing includes five basic principles:
-
Define value - Find out what your business contributes to society, and what makes it different from other competitors.
-
Reduce Waste – Eliminate all activities that don't add value throughout the supply chain.
-
Create Flow - Ensure work moves smoothly through the process without interruption.
-
Standardize and simplify – Make processes as repeatable and consistent as possible.
-
Build Relationships- Develop personal relationships with both internal as well as external stakeholders.
Lean manufacturing isn’t new, but it has seen a renewed interest since 2008 due to the global financial crisis. Many companies have adopted lean manufacturing methods to increase their marketability. Economists think that lean manufacturing is a crucial factor in economic recovery.
Lean manufacturing, which has many benefits, is now a standard practice in the automotive industry. These include better customer satisfaction and lower inventory levels. They also result in lower operating costs.
You can apply Lean Manufacturing to virtually any aspect of your organization. Because it makes sure that all value chains are efficient and effectively managed, Lean Manufacturing is particularly helpful for organizations.
There are three main types:
-
Just-in Time Manufacturing: This lean manufacturing method is commonly called "pull systems." JIT is a method in which components are assembled right at the moment of use, rather than being manufactured ahead of time. This method reduces lead times, increases availability, and decreases inventory.
-
Zero Defects Manufacturing - ZDM: ZDM focuses its efforts on making sure that no defective units leave a manufacturing facility. If a part needs to be fixed during the assembly line, it should be repaired rather than scrapped. This is true even for finished products that only require minor repairs prior to shipping.
-
Continuous Improvement (CI),: Continuous improvement aims improve the efficiency and effectiveness of operations by continuously identifying issues and making changes to reduce waste. It involves continuous improvement of processes, people, and tools.