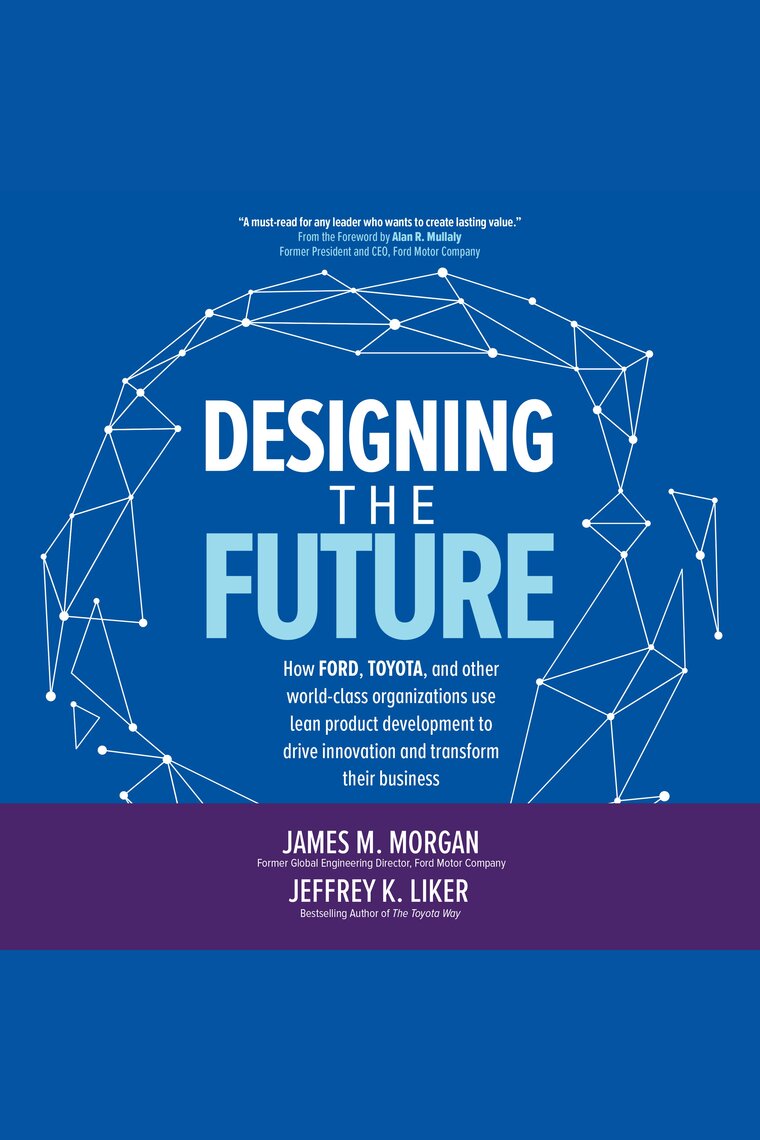
Lean System Management is a technique for reducing waste on the job. It is based in the belief every process or activity within an organisation should add to the value of the service or product it offers customers. This can only be achieved by eliminating the activities that are not adding value and working on a systematic basis to create even more value.
A lean management is designed to increase the performance of an organization. It helps employees to understand their purpose and goals.
The first step of lean system-management is to define what value is. This is done by identifying customer needs and then designing a system that meets those needs. To achieve this, it is important to ensure that the entire production process and customer service are efficient and consistent.
The use of lean principles in the production of products can be an effective way to cut costs and increase efficiency. However, it is important to get your employees on board. Results could be disastrous without a commitment to the programme.
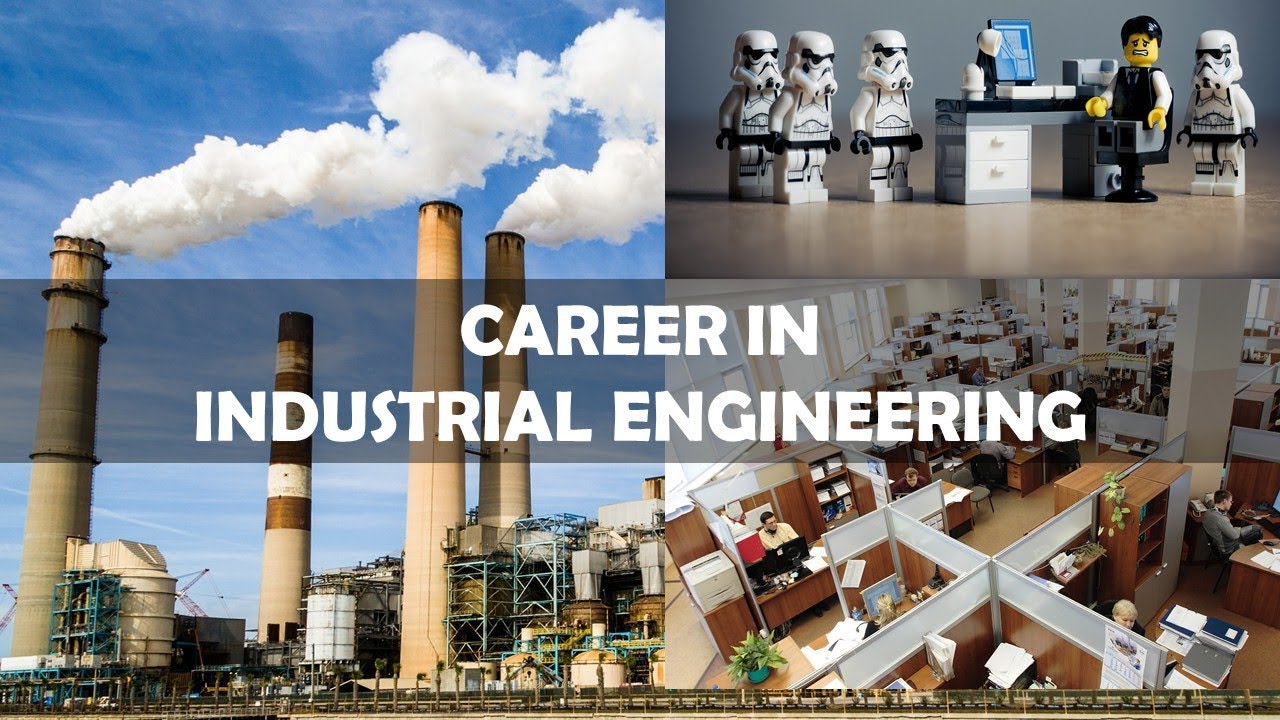
You must also ensure that the supply chain of your company is healthy. It's because many lean initiatives involve retooling the supply-chain to make it function well.
To help you achieve this, it is important to ensure that your staff has received proper training in lean concepts. This includes making sure employees understand waste and why it is important to eliminate it.
You should also take into account the need for teamwork when you implement lean principles. This is not easy to do, but it's an important element of the Lean System and will allow you to eliminate waste from your production.
This will enable your team to produce products and services of higher quality and ultimately increase the bottom line of your business. Give them the chance to meet up regularly to discuss how they can reduce waste.
A lean manager will be able to help you by ensuring all your workers are properly trained in these techniques. They can keep your production processes flowing smoothly and efficiently by keeping all team members informed of potential problems.
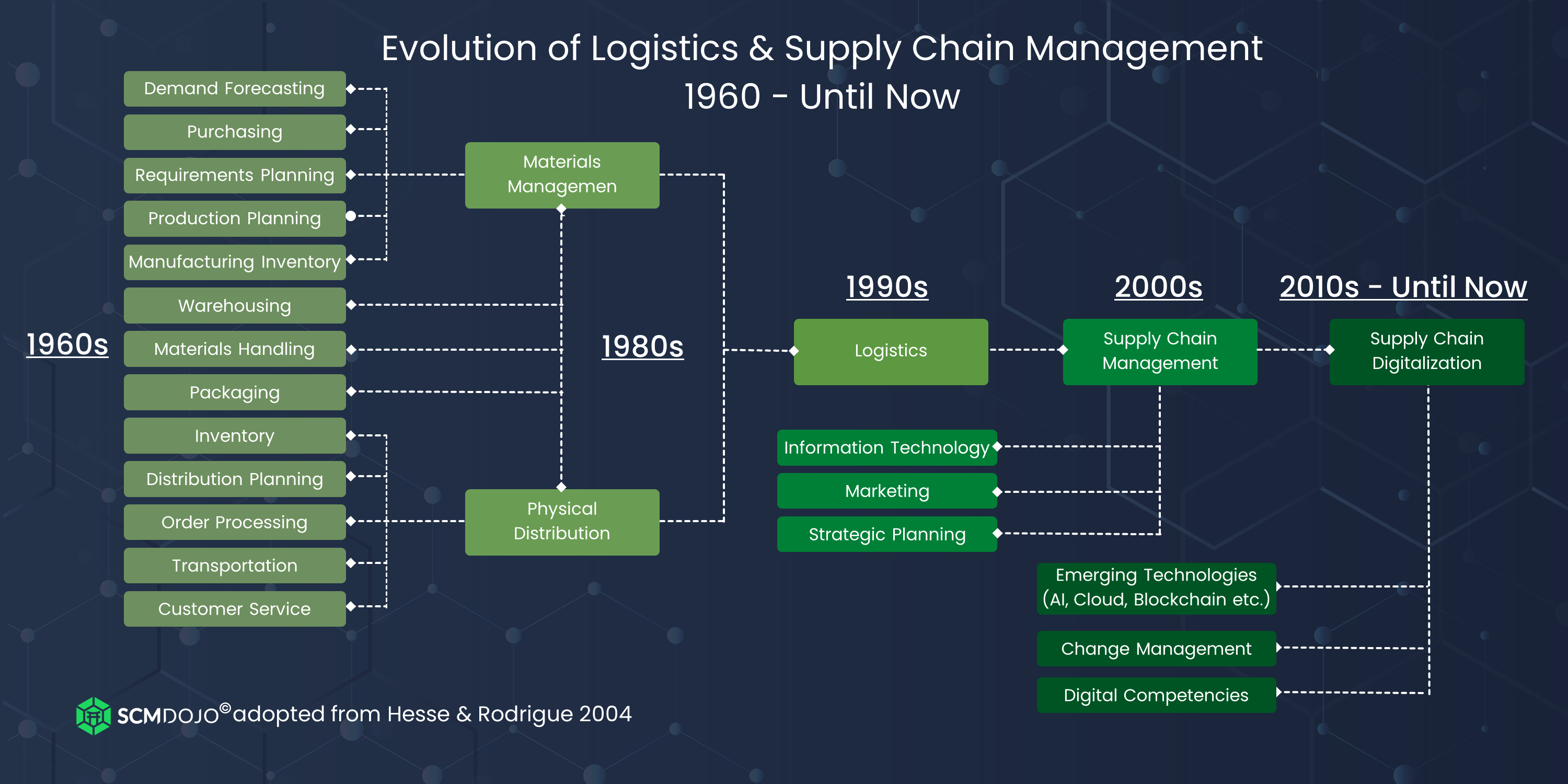
The final step to lean system management involves monitoring and improving each of the implemented procedures. This can be achieved by tracking progress on each project and ensuring any necessary changes are implemented.
Depending on the level of your organization, you may need to hire someone to manage your lean operations. Searching for lean management positions or job boards can help you find candidates.
FAQ
What is the distinction between Production Planning or Scheduling?
Production Planning (PP), or production planning, is the process by which you determine what products are needed at any given time. This is accomplished by forecasting the demand and identifying production resources.
Scheduling involves the assignment of dates and times to tasks in order to complete them within the timeframe.
What are the differences between these four types?
Manufacturing is the process that transforms raw materials into useful products. It can involve many activities like designing, manufacturing, testing packaging, shipping, selling and servicing.
What makes a production planner different from a project manger?
The primary difference between a producer planner and a manager of a project is that the manager usually plans and organizes the whole project, while a production planner is only involved in the planning stage.
What is the responsibility of a production planner?
Production planners ensure that all project aspects are completed on time, within budget and within the scope. They also ensure the quality of the product and service meets the client's requirements.
How can we reduce manufacturing overproduction?
The key to reducing overproduction lies in developing better ways to manage inventory. This would decrease the time that is spent on inefficient activities like purchasing, storing, or maintaining excess stock. By doing this, we could free up resources for other productive tasks.
You can do this by adopting a Kanban method. A Kanbanboard is a visual tool that allows you to keep track of the work being done. A Kanban system allows work items to move through several states before reaching their final destination. Each state represents an individual priority level.
As an example, if work is progressing from one stage of the process to another, then the current task is complete and can be transferred to the next. But if a task remains in the beginning stages it will stay that way until it reaches its end.
This allows for work to continue moving forward, while also ensuring that there is no work left behind. Managers can see how much work has been done and the status of each task at any time with a Kanban Board. This allows them the ability to adjust their workflow using real-time data.
Lean manufacturing is another way to manage inventory levels. Lean manufacturing emphasizes eliminating waste in all phases of production. Waste includes anything that does not add value to the product. There are several types of waste that you might encounter:
-
Overproduction
-
Inventory
-
Packaging that is not necessary
-
Material surplus
By implementing these ideas, manufacturers can improve efficiency and cut costs.
How can manufacturing avoid production bottlenecks
Production bottlenecks can be avoided by ensuring that processes are running smoothly during the entire production process, starting with the receipt of an order and ending when the product ships.
This includes planning to meet capacity requirements and quality control.
Continuous improvement techniques such Six Sigma can help you achieve this.
Six Sigma is a management system used to improve quality and reduce waste in every aspect of your organization.
It emphasizes consistency and eliminating variance in your work.
What is the importance of logistics in manufacturing?
Logistics are an essential part of any business. They are essential to any business's success.
Logistics are also important in reducing costs and improving efficiency.
Statistics
- (2:04) MTO is a production technique wherein products are customized according to customer specifications, and production only starts after an order is received. (oracle.com)
- Job #1 is delivering the ordered product according to specifications: color, size, brand, and quantity. (netsuite.com)
- Many factories witnessed a 30% increase in output due to the shift to electric motors. (en.wikipedia.org)
- According to a Statista study, U.S. businesses spent $1.63 trillion on logistics in 2019, moving goods from origin to end user through various supply chain network segments. (netsuite.com)
- You can multiply the result by 100 to get the total percent of monthly overhead. (investopedia.com)
External Links
How To
Six Sigma in Manufacturing:
Six Sigma refers to "the application and control of statistical processes (SPC) techniques in order to achieve continuous improvement." Motorola's Quality Improvement Department in Tokyo, Japan developed Six Sigma in 1986. Six Sigma's core idea is to improve the quality of processes by standardizing and eliminating defects. This method has been adopted by many companies in recent years as they believe there are no perfect products or services. Six Sigma's primary goal is to reduce variation from the average value of production. It is possible to measure the performance of your product against an average and find the percentage of time that it differs from the norm. If you notice a large deviation, then it is time to fix it.
Understanding how variability works in your company is the first step to Six Sigma. Once you have a good understanding of the basics, you can identify potential sources of variation. Also, you will need to identify the sources of variation. Random variations occur when people do mistakes. Symmetrical variations are caused due to factors beyond the process. For example, if you're making widgets, and some of them fall off the assembly line, those would be considered random variations. If however, you notice that each time you assemble a widget it falls apart in exactly the same spot, that is a problem.
Once you have identified the problem, you can design solutions. You might need to change the way you work or completely redesign the process. You should then test the changes again after they have been implemented. If they don't work you need to rework them and come up a better plan.