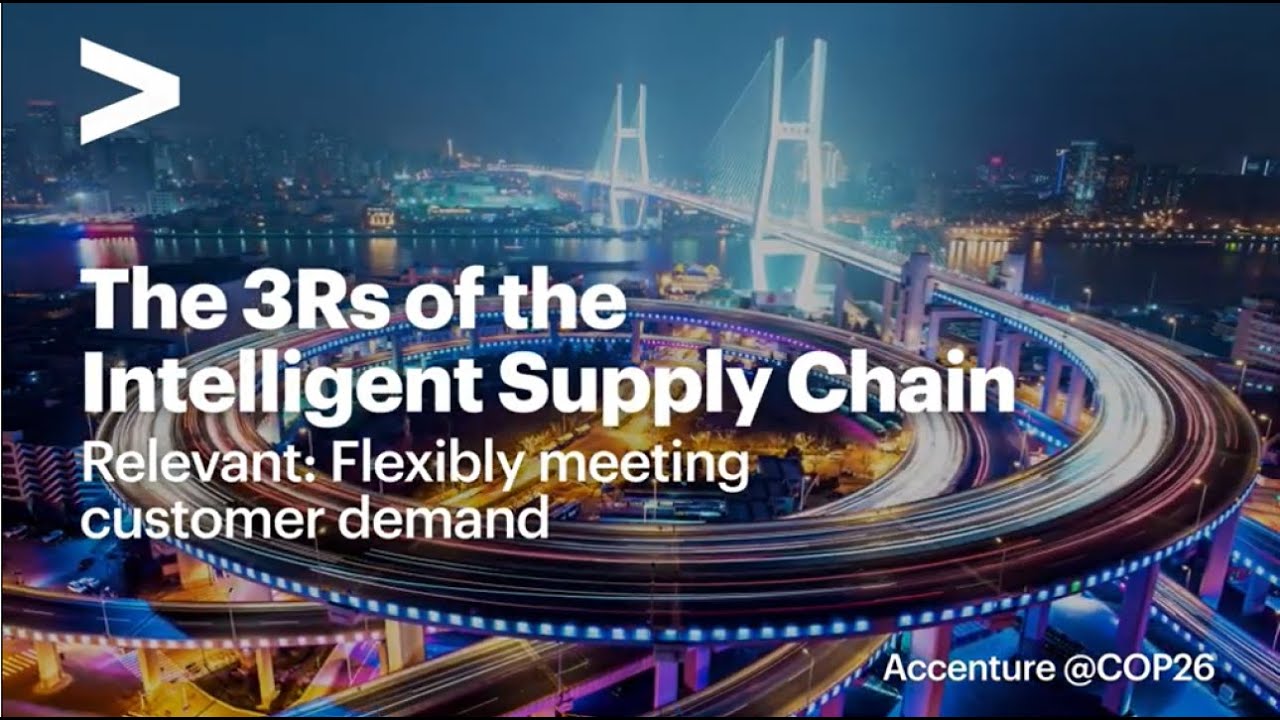
Manufacturing has been a key part of the economy all through history. From the production of stone tools to mass production, manufacturing provides humankind with all the necessary tools to survive. Manufacturing has allowed us to increase our human population as well as develop new technology. Manufacturing is also responsible for some of the greatest inventions ever made.
Manufacturing creates wealth. It produces goods, materials, and equipment that are used in other industries like food and construction. It improves the quality of life for all citizens. It provides jobs for the middle class and adds value to the economy. Strong manufacturing bases reduce the risk of poverty and war. The United States boasts one of largest manufacturing sectors worldwide. The manufacturing sector also contributes a large amount to exports.
Manufacturing is important as it is the process by which raw materials are transformed into useful products. These raw materials could be metals, natural gas, wood or any other material. Manufacturing is about producing more goods at lower prices. This is possible through the use of economies of scale. Ford was an example of mass production. By utilizing the assembly line, finished products could be easily produced. This allows for increased productivity and profit.
For their employees to be up-to-date with the latest technology, manufacturers need to invest in training. They also need to train their employees to be more efficient in their work. To cut costs, manufacturing companies may also buy locally made goods and supplies. The cost of shipping is also reduced, which helps lower the final product's price.
The United States' most important economic sector is the manufacturing industry. In 2010, manufacturing companies accounted for 12 percent of the nation's GDP. The Manufacturing Purchasing Managers Index, also known as the ISM Manufacturing Report, measures manufacturing industry activity monthly. Financial analysts watch the report each month to assess the state of manufacturing. The Economic Policy Institute recently reported that each manufacturing job supports three additional jobs. This multiplier effect is important for economic development and prosperity.
Also, manufacturing helps to raise living standards. Consumers demand that products are of high quality and perform as described. Consumers might stop purchasing products that are poor quality. This could lead to a decrease in manufacturer confidence. A manufacturer could be forced to close its doors. If a manufacturer is unable to produce the goods it sells, it may have its business reduced and customers lost. For inflation to be low, productivity is essential. A higher productivity rate means lower costs, and higher profits. This helps keep poverty rates under control.
Many opportunities exist for skill development in manufacturing. There are many skills you can acquire in the manufacturing industry, including engineering, machining. design and manufacturing. Manufacturers also fund almost a third of the research in the US. Today's products will continue to be advanced through research and innovation.
FAQ
How can we reduce manufacturing overproduction?
It is essential to find better ways to manage inventory to reduce overproduction. This would reduce the time spent on unproductive activities like purchasing, storing and maintaining excess stock. This could help us free up our time for other productive tasks.
A Kanban system is one way to achieve this. A Kanbanboard is a visual tool that allows you to keep track of the work being done. In a Kanban system, work items move through a sequence of states until they reach their final destination. Each state is assigned a different priority.
As an example, if work is progressing from one stage of the process to another, then the current task is complete and can be transferred to the next. A task that is still in the initial stages of a process will be considered complete until it moves on to the next stage.
This allows for work to continue moving forward, while also ensuring that there is no work left behind. Managers can see how much work has been done and the status of each task at any time with a Kanban Board. This information allows them to adjust their workflow based on real-time data.
Lean manufacturing can also be used to reduce inventory levels. Lean manufacturing seeks to eliminate waste from every step of the production cycle. Anything that does not contribute to the product's value is considered waste. These are some of the most common types.
-
Overproduction
-
Inventory
-
Unnecessary packaging
-
Excess materials
By implementing these ideas, manufacturers can improve efficiency and cut costs.
What is the difference between Production Planning and Scheduling?
Production Planning (PP) is the process of determining what needs to be produced at any given point in time. This is done through forecasting demand and identifying production capacities.
Scheduling refers the process by which tasks are assigned dates so that they can all be completed within the given timeframe.
Is it possible to automate certain parts of manufacturing
Yes! Yes! Automation has existed since ancient times. The Egyptians discovered the wheel thousands and years ago. To help us build assembly lines, we now have robots.
There are many applications for robotics in manufacturing today. These include:
-
Automated assembly line robots
-
Robot welding
-
Robot painting
-
Robotics inspection
-
Robots that produce products
Automation could also be used to improve manufacturing. 3D printing is a way to make custom products quickly and without waiting weeks or months for them to be manufactured.
What skills is required for a production planner?
You must be flexible and organized to become a productive production planner. You must also be able to communicate effectively with clients and colleagues.
Statistics
- Job #1 is delivering the ordered product according to specifications: color, size, brand, and quantity. (netsuite.com)
- (2:04) MTO is a production technique wherein products are customized according to customer specifications, and production only starts after an order is received. (oracle.com)
- In 2021, an estimated 12.1 million Americans work in the manufacturing sector.6 (investopedia.com)
- According to the United Nations Industrial Development Organization (UNIDO), China is the top manufacturer worldwide by 2019 output, producing 28.7% of the total global manufacturing output, followed by the United States, Japan, Germany, and India.[52][53] (en.wikipedia.org)
- [54][55] These are the top 50 countries by the total value of manufacturing output in US dollars for its noted year according to World Bank.[56] (en.wikipedia.org)
External Links
How To
How to Use 5S to Increase Productivity in Manufacturing
5S stands for "Sort", 'Set In Order", 'Standardize', & Separate>. The 5S methodology was developed at Toyota Motor Corporation in 1954. It helps companies achieve higher levels of efficiency by improving their work environment.
This method aims to standardize production processes so that they are repeatable, measurable and predictable. This means that daily tasks such as cleaning and sorting, storage, packing, labeling, and packaging are possible. Because workers know what they can expect, this helps them perform their jobs more efficiently.
Implementing 5S requires five steps. These are Sort, Set In Order, Standardize. Separate. And Store. Each step involves a different action which leads to increased efficiency. By sorting, for example, you make it easy to find the items later. Once you have placed items in an ordered fashion, you will put them together. After you have divided your inventory into groups you can store them in easy-to-reach containers. Labeling your containers will ensure that everything is correctly labeled.
Employees will need to be more critical about their work. Employees should understand why they do the tasks they do, and then decide if there are better ways to accomplish them. They will need to develop new skills and techniques in order for the 5S system to be implemented.
In addition to improving efficiency, the 5S system also increases morale and teamwork among employees. They are more motivated to achieve higher efficiency levels as they start to see improvement.