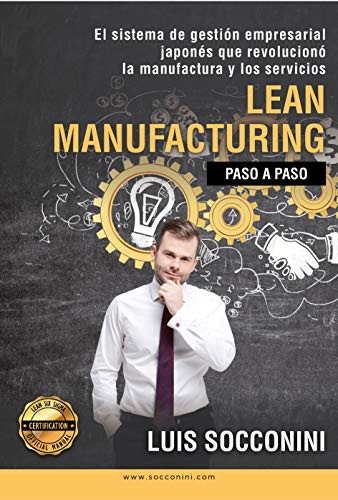
Manufacturing in the US is a big part of the American economy. About eleven percent of total national economic output is driven by the sector. It also contributes a lot to the world economy, accounting for 18.2 per cent of global goods. However, growth in the manufacturing sector has been slowing in recent years.
Since 2000 the US has lost nearly a third of its manufacturing jobs. According to the Bureau of Labor Statistics, manufacturing productivity grew by 4.5 percent each year between 1995 and 2000. While once manufacturing was seen as a declining job generator but automation and other technological advances have led to a reexamination regarding how technology is impacting the employment market.
Walmart pledged to support American jobs in January 2013. Walmart intends to purchase $250 Billion in products from American companies within ten years. Walmart will continue to support American manufacturing and encourage companies to explore possible opportunities with the giant retailer.
The United States has been a major player on the global market but it has also faced many challenges. Some of these challenges are caused by the rising cost of labor overseas, a soaring corporate tax rate, and a lack of skills in trade negotiations. These issues could hinder the sector's future.
The US also faces a skills problem, with an estimated 1.42 million factory workers in desperate need of training. Trump's policies are aimed at expanding apprenticeship programs and training, but there have been concerns about the quality.
Despite the difficulties the US manufacturing industry has recovered after the Great Recession. Manufacturing output hit a new record of $2.00 Trillion in the first quarter 2018. This was significantly higher than the $1.95 billion that was reached in the prior year, before the recession.
While the US's manufacturing sector has experienced slower growth than the US overall economy, the industry is expected to grow at an even faster pace in the next few years. The industry is expected to grow by 2.4 percent in 2020 and 1.9% 2021.
Exports are expected to increase, which will help the manufacturing sector. In addition, energy costs have been reduced as shale oil has benefited the industry. The United States also has a competitive corporate rate that is higher than many other countries around the globe.
In parallel, China and Japan are experiencing manufacturing contraction. This is the first time the S&P Global purchasing management index has been below 50 in these countries for almost two years.
According to reports, the Trump administration is working on a federal program that's less bureaucratic to support the manufacturing industry. Manufacturing Extension Partnership (MEP), one of the most critical federal programs, is one of its most important. MEPs can generate $21 in client investment for every $21 invested by the federal government. The MEP also has centers in all 50 states as well as Canada, Mexico, and Europe.
The US is far less successful in trade negotiations than other industrial nations. This means that the government does not have the skills to negotiate bilateral trade agreements. The US faces challenges in attracting more manufacturers and keeping existing companies.
FAQ
What are the jobs in logistics?
Logistics can offer many different jobs. Some of them are:
-
Warehouse workers - They load and unload trucks and pallets.
-
Transportation drivers - They drive trucks and trailers to deliver goods and carry out pick-ups.
-
Freight handlers – They sort and package freight at warehouses.
-
Inventory managers - They oversee the inventory of goods in warehouses.
-
Sales representatives - They sell products to customers.
-
Logistics coordinators: They plan and manage logistics operations.
-
Purchasing agents – They buy goods or services necessary to run a company.
-
Customer service representatives – They answer emails and phone calls from customers.
-
Shippers clerks - They process shipping order and issue bills.
-
Order fillers are people who fill orders based only on what was ordered.
-
Quality control inspectors – They inspect incoming and outgoing products to ensure that there are no defects.
-
Others - There are many other types of jobs available in logistics, such as transportation supervisors, cargo specialists, etc.
What are the four types of manufacturing?
Manufacturing is the process by which raw materials are transformed into useful products through machines and processes. Manufacturing involves many activities, including designing, building, testing and packaging, shipping, selling, service, and so on.
How does manufacturing avoid bottlenecks in production?
The key to avoiding bottlenecks in production is to keep all processes running smoothly throughout the entire production cycle, from the time you receive an order until the time when the product ships.
This includes both quality control and capacity planning.
Continuous improvement techniques such Six Sigma can help you achieve this.
Six Sigma is a management system used to improve quality and reduce waste in every aspect of your organization.
It's all about eliminating variation and creating consistency in work.
Statistics
- You can multiply the result by 100 to get the total percent of monthly overhead. (investopedia.com)
- Job #1 is delivering the ordered product according to specifications: color, size, brand, and quantity. (netsuite.com)
- Many factories witnessed a 30% increase in output due to the shift to electric motors. (en.wikipedia.org)
- It's estimated that 10.8% of the U.S. GDP in 2020 was contributed to manufacturing. (investopedia.com)
- (2:04) MTO is a production technique wherein products are customized according to customer specifications, and production only starts after an order is received. (oracle.com)
External Links
How To
Six Sigma and Manufacturing
Six Sigma is "the application statistical process control (SPC), techniques for continuous improvement." Motorola's Quality Improvement Department developed it at their Tokyo plant in Japan in 1986. Six Sigma's basic concept is to improve quality and eliminate defects through standardization. In recent years, many companies have adopted this method because they believe there is no such thing as perfect products or services. Six Sigma aims to reduce variation in the production's mean value. You can calculate the percentage of deviation from the norm by taking a sample of your product and comparing it to the average. If you notice a large deviation, then it is time to fix it.
Understanding the dynamics of variability within your business is the first step in Six Sigma. Once you have a good understanding of the basics, you can identify potential sources of variation. You'll also want to determine whether these variations are random or systematic. Random variations occur when people do mistakes. Symmetrical variations are caused due to factors beyond the process. Random variations would include, for example, the failure of some widgets to fall from the assembly line. It would be considered a systematic problem if every widget that you build falls apart at the same location each time.
Once you've identified the problem areas you need to find solutions. You might need to change the way you work or completely redesign the process. You should then test the changes again after they have been implemented. If they don't work, you will need to go back to the drawing boards and create a new plan.