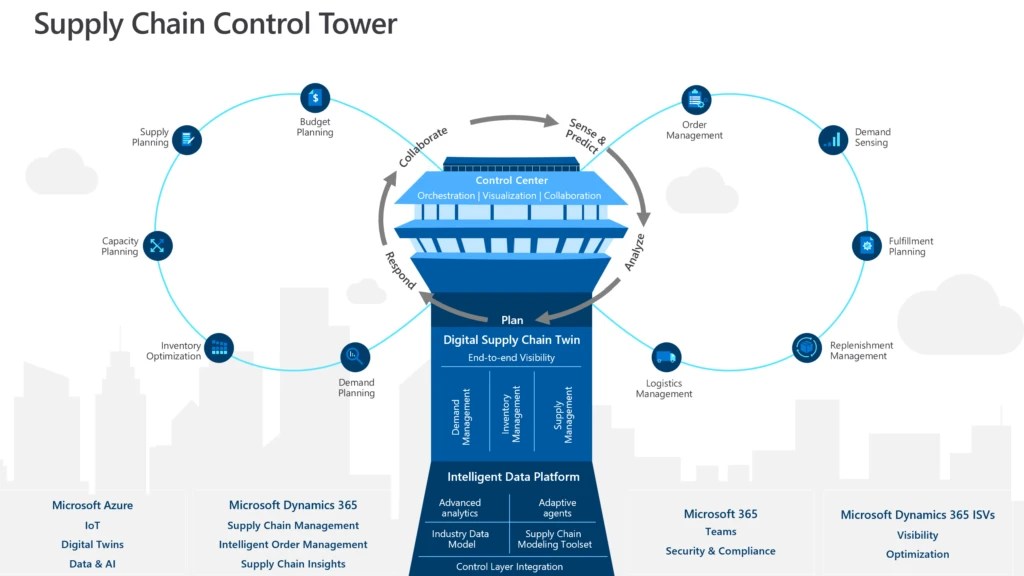
The core qualifications section should be included in the job description of an environmental engineer. This will set out the minimum requirements required for the job in order to attract qualified candidates. This will streamline the process of recruiting and help to avoid applicants who are not qualified. It is also beneficial to include a skills section in order to make the hiring process as easy as possible. Keep reading for more. The job description should be in a professional and formal language that makes it stand out from other applicants.
Qualifications
If you're considering changing careers to become an environmental engineer, you should know the details of the job. This position requires you to plan and implement systems to control air, water, and remediate site. This position often requires collaboration between other professionals such hazardous waste technicians and environmental experts. Sometimes, environmental engineers are required to provide technical assistance for environmental litigation and remediation. They also monitor the progress of environmental improvement programs and contribute to the development of environmental journals.
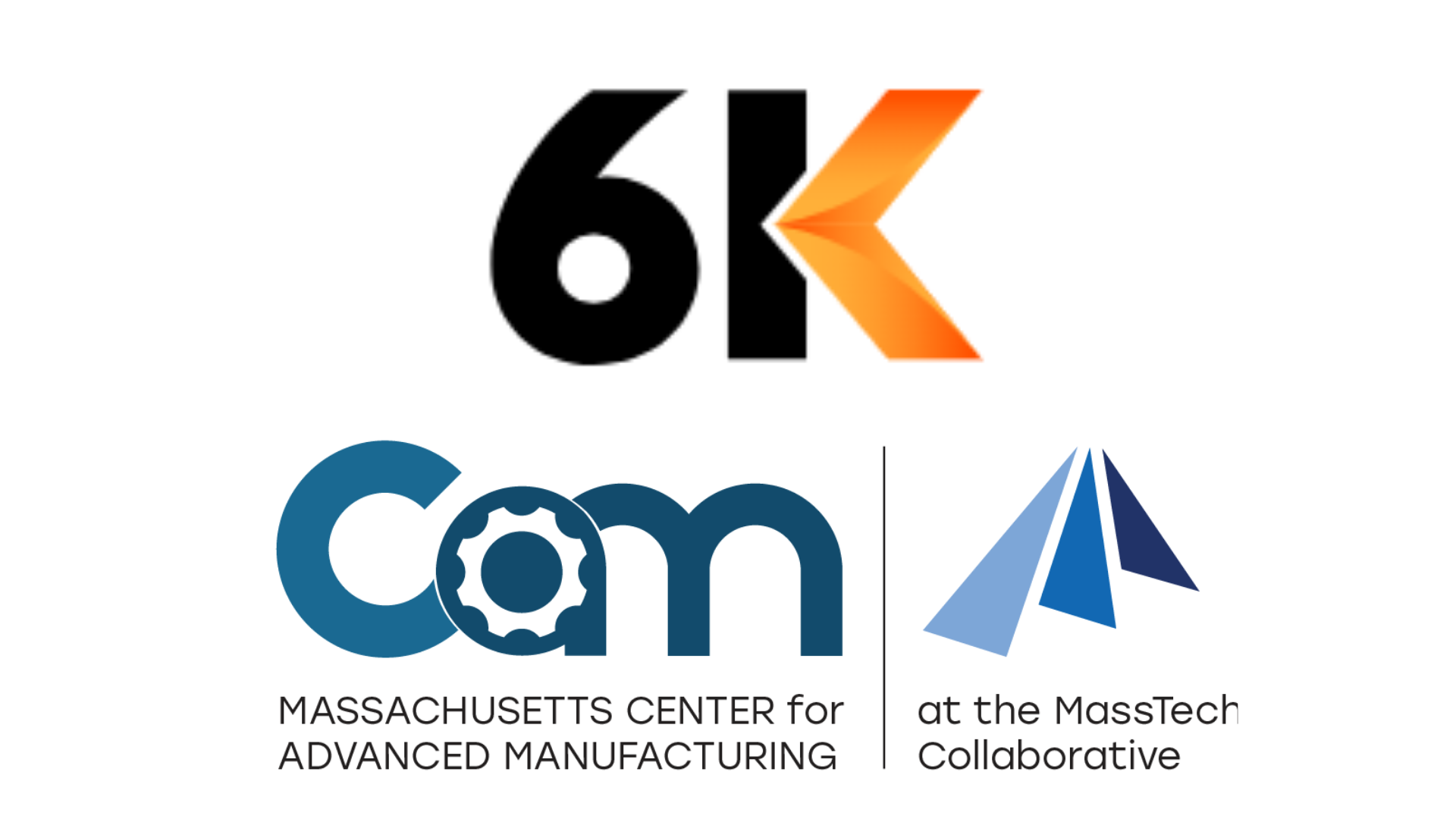
Being an environmental engineer requires extensive office and field work. An environmental engineer may be responsible for field inspections, characterizing and evaluating materials, or working with subcontractors on site. This job requires a deep understanding of environmental regulations. In addition, they may be required to create and maintain spreadsheets and other elements of a report. They may take on a range of projects and be able to move up from related jobs into their own fields.
Responsibilities
A variety of responsibilities are available to an environmental engineer. The environmental engineer can design technology to prevent pollution and make recommendations for clean-up efforts. They may also work alongside legal counsel or other experts, such business people and those who specialize in law. Other administrative duties that environmental engineers might perform include the creation of spreadsheets and other components for reports. Environmental engineers may advise federal, regional, and local government agencies in matters of environmental protection.
The role of an environmental engineering assistant includes the design and implementation plan and program development for conservation and management. They assess the effects of a proposed commercial activity on land and other resources. They are also responsible for general administrative tasks such as the preparation of project documentation, training staff and aiding in budget implementation. A policymaker may be advised by an environmental engineer on best practices and environmental issues.
Perspectives on employment
Positive employment prospects are available for environmental engineers. Engineers with the ability to assist businesses in complying environmental regulations, finding alternative ways of removing pollution, and managing their waste are in strong demand. Environmental engineers will see a rise in demand due to the growing population and emphasis on prevention. As workers leave and move into other fields or retire, job opportunities will increase. This is a job that will not disappoint. Here are some job opportunities you could be applying for in the near future.
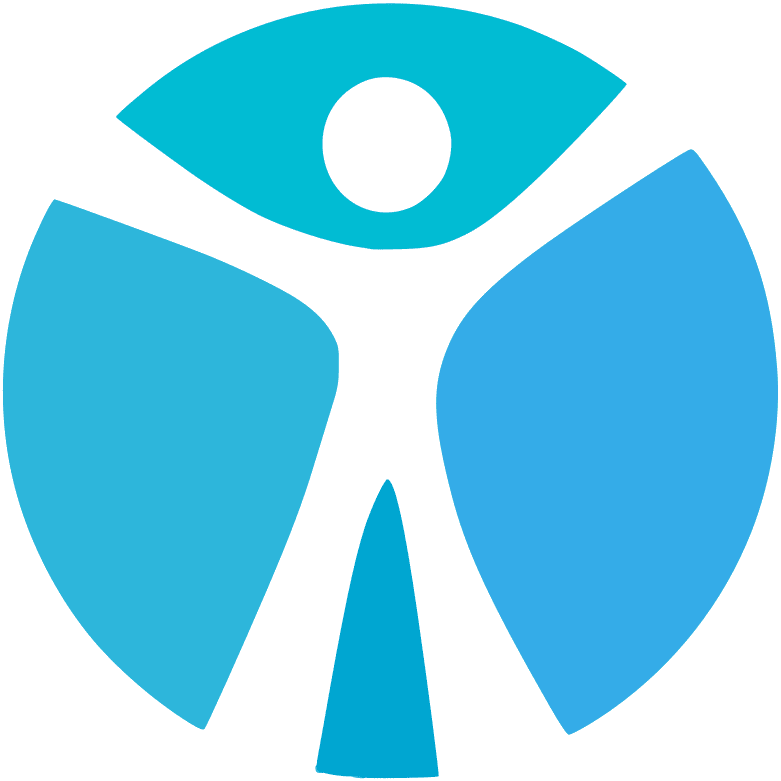
Many environmental engineers work in laboratories or offices. Some work indoors while others travel or spend time outside. They typically work forty hours a week. Your schedule might vary for certain jobs that require you to travel. You may face challenges, particularly if you have to meet deadlines. As the environment is their primary concern, environmental engineers must be aware their limitations. This career can also be subject to long hours and high stress levels.
FAQ
What are the main products of logistics?
Logistics is the process of moving goods from one point to another.
They cover all aspects of transportation, such as packing, loading, transporting and unloading.
Logisticians ensure that the product is delivered to the correct place, at the right time, and under safe conditions. They assist companies with their supply chain efficiency through information on demand forecasts. Stock levels, production times, and availability.
They monitor shipments in transit, ensure quality standards, manage inventories, replenish orders, coordinate with suppliers and other vendors, and offer support services for sales, marketing, and customer service.
What is the responsibility of a logistics manager?
Logistics managers ensure that goods arrive on time and are unharmed. This is achieved by using their knowledge and experience with the products of the company. He/she should also ensure enough stock is available to meet demand.
Do we need to know about Manufacturing Processes before learning about Logistics?
No. No. Knowing about manufacturing processes will help you understand how logistics works.
What are the responsibilities of a manufacturing manager
A manufacturing manager must ensure that all manufacturing processes are efficient and effective. They should be aware of any issues within the company and respond accordingly.
They should also be able and comfortable communicating with other departments like sales and marketing.
They must also keep up-to-date with the latest trends in their field and be able use this information to improve productivity and efficiency.
Why automate your factory?
Modern warehousing has seen automation take center stage. With the rise of ecommerce, there is a greater demand for faster delivery times as well as more efficient processes.
Warehouses must adapt quickly to meet changing customer needs. Technology investment is necessary to enable warehouses to respond quickly to changing demands. Automating warehouses has many benefits. Here are some benefits of investing in automation
-
Increases throughput/productivity
-
Reduces errors
-
Increases accuracy
-
Safety increases
-
Eliminates bottlenecks
-
Allows companies to scale more easily
-
Increases efficiency of workers
-
The warehouse can be viewed from all angles.
-
Enhances customer experience
-
Improves employee satisfaction
-
Reduces downtime and improves uptime
-
Quality products delivered on time
-
Human error can be eliminated
-
Assure compliance with regulations
How can we increase manufacturing efficiency?
First, determine which factors have the greatest impact on production time. Next, we must find ways to improve those factors. If you aren't sure where to begin, think about the factors that have the greatest impact on production time. Once you've identified them, try to find solutions for each of those factors.
Statistics
- Many factories witnessed a 30% increase in output due to the shift to electric motors. (en.wikipedia.org)
- According to a Statista study, U.S. businesses spent $1.63 trillion on logistics in 2019, moving goods from origin to end user through various supply chain network segments. (netsuite.com)
- Job #1 is delivering the ordered product according to specifications: color, size, brand, and quantity. (netsuite.com)
- (2:04) MTO is a production technique wherein products are customized according to customer specifications, and production only starts after an order is received. (oracle.com)
- It's estimated that 10.8% of the U.S. GDP in 2020 was contributed to manufacturing. (investopedia.com)
External Links
How To
How to Use Lean Manufacturing in the Production of Goods
Lean manufacturing (or lean manufacturing) is a style of management that aims to increase efficiency, reduce waste and improve performance through continuous improvement. It was developed in Japan between 1970 and 1980 by Taiichi Ohno. TPS founder Kanji Tyoda gave him the Toyota Production System, or TPS award. Michael L. Watkins published the book "The Machine That Changed the World", which was the first to be published about lean manufacturing.
Lean manufacturing refers to a set of principles that improve the quality, speed and costs of products and services. It is about eliminating defects and waste from all stages of the value stream. Just-in-time (JIT), zero defect (TPM), and 5S are all examples of lean manufacturing. Lean manufacturing emphasizes reducing non-value-added activities like inspection, rework and waiting.
Lean manufacturing improves product quality and costs. It also helps companies reach their goals quicker and decreases employee turnover. Lean manufacturing can be used to manage all aspects of the value chain. Customers, suppliers, distributors, retailers and employees are all included. Many industries worldwide use lean manufacturing. Toyota's philosophy, for example, is what has enabled it to be successful in electronics, automobiles, medical devices, healthcare and chemical engineering as well as paper and food.
Lean manufacturing is based on five principles:
-
Define Value - Determine the value that your business brings to society. Also, identify what sets you apart from your competitors.
-
Reduce waste - Get rid of any activity that does not add value to the supply chain.
-
Create Flow - Ensure work moves smoothly through the process without interruption.
-
Standardize and Simplify – Make processes as consistent, repeatable, and as simple as possible.
-
Build Relationships - Establish personal relationships with both internal and external stakeholders.
Lean manufacturing is not a new concept, but it has been gaining popularity over the last few years due to a renewed interest in the economy following the global financial crisis of 2008. To increase their competitiveness, many businesses have turned to lean manufacturing. Many economists believe lean manufacturing will play a major role in economic recovery.
With many benefits, lean manufacturing is becoming more common in the automotive industry. These include higher customer satisfaction, lower inventory levels, lower operating expenses, greater productivity, and improved overall safety.
You can apply Lean Manufacturing to virtually any aspect of your organization. This is because it ensures efficiency and effectiveness in all stages of the value chain.
There are three main types in lean manufacturing
-
Just-in-Time Manufacturing: Also known as "pull systems", this type of lean manufacturing uses just-in-time manufacturing (JIT). JIT means that components are assembled at the time of use and not manufactured in advance. This method reduces lead times, increases availability, and decreases inventory.
-
Zero Defects Manufacturing (ZDM): ZDM focuses on ensuring that no defective units leave the manufacturing facility. You should repair any part that needs to be repaired during an assembly line. This applies to finished products, which may need minor repairs before they are shipped.
-
Continuous Improvement (CI): CI aims to improve the efficiency of operations by continuously identifying problems and making changes in order to eliminate or minimize waste. Continuous improvement involves continuous improvement of processes and people as well as tools.