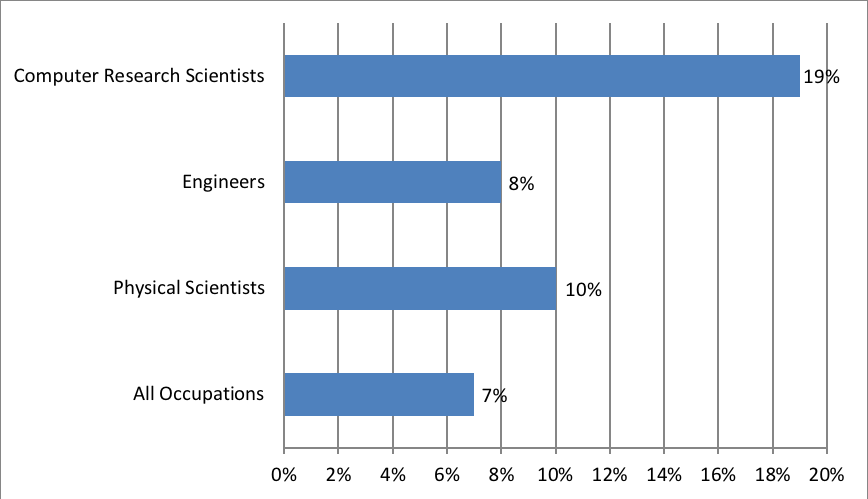
Are you interested in Estimators jobs? Then you might be curious about what it takes to get the job. This article will talk about the typical role, the work environment and the salary range. It will also cover the skills and experience required for this role. Continue reading for more information. Here are some key characteristics that an ideal candidate needs to possess. All of these characteristics will make your job as an estimator more appealing.
Ideal candidate for estimator role
The ideal candidate to fill the Estimator role is well-versed in mathematics and exceptional analytical skills. He or she should also possess excellent communication skills and be detail-oriented. A minimum of a Bachelor's degree is required, along with 3 years experience in a related field. Candidates should also be proficient in MS Office suite. They must be able work under pressure and have strong analytical skills.
A bachelor's degree or equivalent in construction is necessary to apply for the Estimator job. The candidate must be motivated and enthusiastic. They must be able and willing to communicate with clients and demonstrate self-confidence. They should be able and confident to present their estimates, as well as make a positive first impression. It is essential that the candidate can live up to their promises and holds them responsible for meeting deadlines.
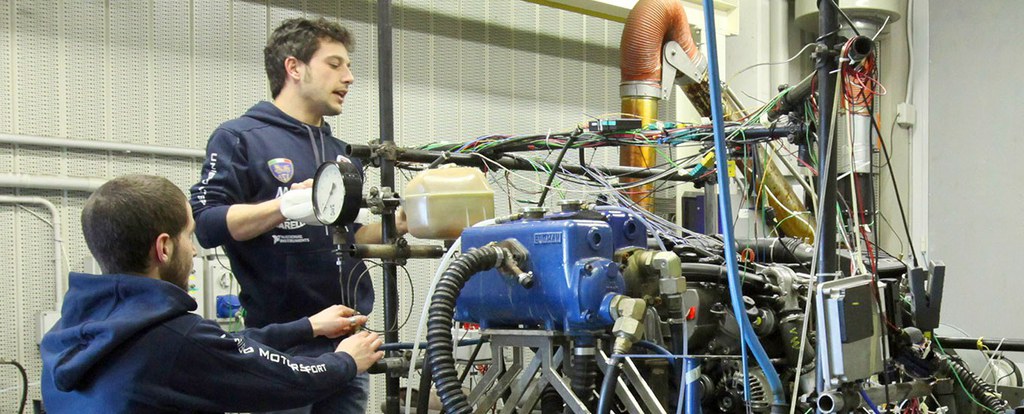
Job description
An estimator's primary task is to produce detailed reports that will help improve the company's profitability. An estimator uses computer software to communicate with staff and determine the cost and time of a project. The estimates also present recommendations to clients and include budget risks. Estimators make educated guesses about the costs of a project. These workers are still valuable to employers and can greatly improve a company's bottom-line.
In this role, the job description for estimators should be tailored to the particular area of interest of the applicant. An example of this is a job description that requires a background knowledge in quantity surveying. However, it is not necessary to be an expert on all construction projects. Estimators should also be familiar with other fields, such as technology, environment, and energy. There is a job description that suits the needs of every construction company, whether they are looking for a contractor or full-time employee.
Salary
An Estimator is a person who works in the construction industry to determine the cost of a project. Estimators have a wide variety of responsibilities and may specialize in a particular area. To increase your salary as an estimator, it is important to first determine the amount of experience you have. It is important to find a company offering an apprenticeship program. It may be worth looking for a position if you have an associates degree in estimating. You will be able to move up the ladder and earn a full time salary.
An estimator must not only provide valuable information but also have a deep understanding of building materials and techniques. This knowledge allows them to produce accurate and useful forecasts. They often work under high pressure. Although they work in high-pressure environments, their job requires them be collaborative. They must provide accurate information to other professionals and work in teams. Salary figures for estimators are based on Indeed Salaries data and may differ by location, employer, and candidate's education.
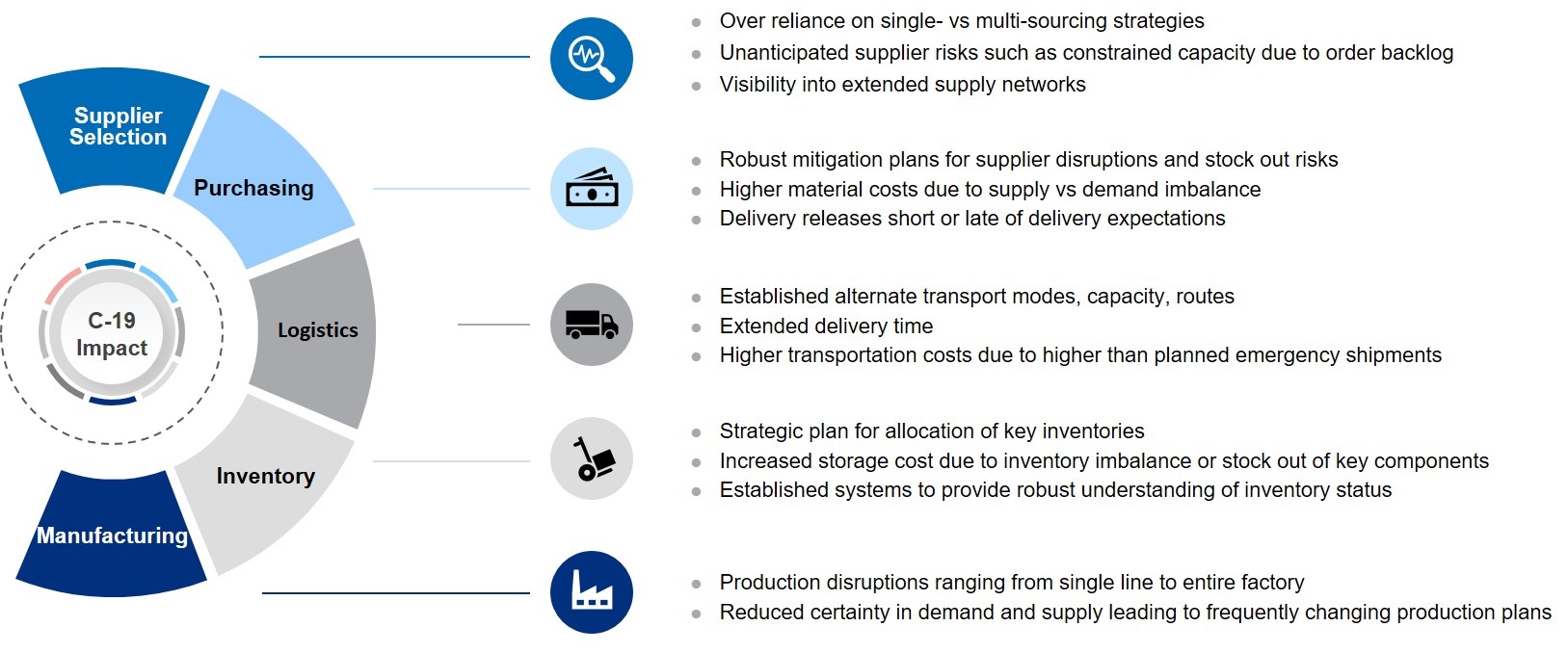
Work environment
Your primary responsibility as an estimator is to prepare competitive bids on construction projects. You will also be responsible for all aspects of estimating, including analyzing RFPs and identifying high-yielding work. As a bidding coordinator, you will help to set priorities and coordinate pre-bid meetings. You will also identify the labor, equipment, materials, and other requirements for each project. You will also be working with project managers to prepare different change orders.
Although a bachelor's is required for most estimator positions, some employers will only hire people with a high-school diploma. Some employers will hire individuals with only an associate's level, but most prefer those with a four-year or five year college degree. Mathematics, business-related degrees, applied science and civil engineering are some of the most popular. A strong understanding of numeracy is essential for construction estimators.
FAQ
Is automation important in manufacturing?
Automation is essential for both manufacturers and service providers. They can provide services more quickly and efficiently thanks to automation. It also helps to reduce costs and improve productivity.
What are the differences between these four types?
Manufacturing is the process by which raw materials are transformed into useful products through machines and processes. Manufacturing involves many activities, including designing, building, testing and packaging, shipping, selling, service, and so on.
What jobs are available in logistics?
There are different kinds of jobs available in logistics. Here are some:
-
Warehouse workers - They load trucks and pallets.
-
Transportation drivers – These drivers drive trucks and wagons to transport goods and pick up the goods.
-
Freight handlers – They sort and package freight at warehouses.
-
Inventory managers - These are responsible for overseeing the stock of goods in warehouses.
-
Sales representatives - They sell products to customers.
-
Logistics coordinators - They organize and plan logistics operations.
-
Purchasing agents: They are responsible for purchasing goods and services to support company operations.
-
Customer service representatives are available to answer customer calls and emails.
-
Ship clerks - They issue bills and process shipping orders.
-
Order fillers - These people fill orders based on what has been ordered.
-
Quality control inspectors – They inspect incoming and outgoing products to ensure that there are no defects.
-
Others – There are many other types available in logistics. They include transport supervisors, cargo specialists and others.
What are the 7 Rs of logistics?
The acronym 7Rs of Logistics refers to the seven core principles of logistics management. It was created by the International Association of Business Logisticians and published in 2004 under its "Seven Principles of Logistics Management".
The following letters make up the acronym:
-
Responsible - ensure that all actions taken are within legal requirements and are not harmful to others.
-
Reliable - have confidence in the ability to deliver on commitments made.
-
Use resources effectively and sparingly.
-
Realistic - Take into consideration all aspects of operations including cost-effectiveness, environmental impact, and other factors.
-
Respectful - show respect and treat others fairly and fairly
-
Resourceful - look for opportunities to save money and increase productivity.
-
Recognizable - provide customers with value-added services.
Why is logistics so important in manufacturing?
Logistics are an essential component of any business. Logistics can help you achieve amazing results by helping to manage product flow from raw materials to finished products.
Logistics plays a significant role in reducing cost and increasing efficiency.
Statistics
- In the United States, for example, manufacturing makes up 15% of the economic output. (twi-global.com)
- In 2021, an estimated 12.1 million Americans work in the manufacturing sector.6 (investopedia.com)
- It's estimated that 10.8% of the U.S. GDP in 2020 was contributed to manufacturing. (investopedia.com)
- According to a Statista study, U.S. businesses spent $1.63 trillion on logistics in 2019, moving goods from origin to end user through various supply chain network segments. (netsuite.com)
- [54][55] These are the top 50 countries by the total value of manufacturing output in US dollars for its noted year according to World Bank.[56] (en.wikipedia.org)
External Links
How To
How to use the Just-In Time Method in Production
Just-intime (JIT), a method used to lower costs and improve efficiency in business processes, is called just-in-time. It's the process of obtaining the right amount and timing of resources when you need them. This means you only pay what you use. The term was first coined by Frederick Taylor, who developed his theory while working as a foreman in the early 1900s. He saw how overtime was paid to workers for work that was delayed. He then concluded that if he could ensure that workers had enough time to do their job before starting to work, this would improve productivity.
JIT teaches you to plan ahead and prepare everything so you don’t waste time. Also, you should look at the whole project from start-to-finish and make sure you have the resources necessary to address any issues. You can anticipate problems and have enough equipment and people available to fix them. You won't have to pay more for unnecessary items.
There are many JIT methods.
-
Demand-driven: This JIT is where you place regular orders for the parts/materials that are needed for your project. This will allow to track how much material has been used up. This will allow you to calculate how long it will take to make more.
-
Inventory-based: This type allows you to stock the materials needed for your projects ahead of time. This allows you to forecast how much you will sell.
-
Project-driven : This is a method where you make sure that enough money is set aside to pay the project's cost. When you know how much you need, you'll purchase the appropriate amount of materials.
-
Resource-based JIT: This is the most popular form of JIT. This is where you assign resources based upon demand. For instance, if you have a lot of orders coming in, you'll assign more people to handle them. If there aren't many orders, you will assign fewer people.
-
Cost-based: This is the same as resource-based except that you don't care how many people there are but how much each one of them costs.
-
Price-based: This is very similar to cost-based, except that instead of looking at how much each individual worker costs, you look at the overall price of the company.
-
Material-based is an alternative to cost-based. Instead of looking at the total cost in the company, this method focuses on the average amount of raw materials that you consume.
-
Time-based: Another variation of resource-based JIT. Instead of focusing solely on the amount each employee costs, focus on how long it takes for the project to be completed.
-
Quality-based JIT: This is another variation of resource based JIT. Instead of thinking about how much each employee costs or how long it takes to manufacture something, you think about how good the quality of your product is.
-
Value-based: This is one of the newest forms of JIT. This is where you don't care about how the products perform or whether they meet customers' expectations. Instead, your focus is on the value you bring to the market.
-
Stock-based: This stock-based method focuses on the actual quantity of products being made at any given time. It's used when you want to maximize production while minimizing inventory.
-
Just-in-time (JIT) planning: This is a combination of JIT and supply chain management. It's the process of scheduling delivery of components immediately after they are ordered. It is essential because it reduces lead-times and increases throughput.