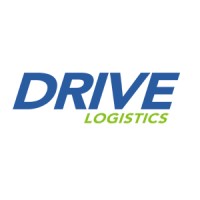
Facilities engineers are also known as maintenance engineers. They provide support in the engineering and construction of buildings and operations. Their duties include implementing and planning procedures, recommending upgrades and repairs, and managing routine and emergency maintenance. A wide range of engineering disciplines can play a part in their role, including electrical, mechanical, and plumbing. Their technical skills are not only complemented by their understanding of construction law and safety standards.
As a career, facilities engineers typically begin at the entry level, and can quickly advance to more senior positions. The best way to stand out in the field is to build a strong portfolio, which may include engineering projects, research, and articles. Facilities engineers must continue to study their specialty. This will make them stand out when they apply for a new job.
While it is not required for all facilities engineers to have a professional engineer certificate, it can be an advantage when applying for a new job. A professional engineer should be well-versed in engineering principles and concepts. He or she must also have the ability to analyse data and present compelling arguments. Facility engineers must have knowledge in areas such as predictive maintenance, asset reliability and maintenance strategies, as well the design of facilities.
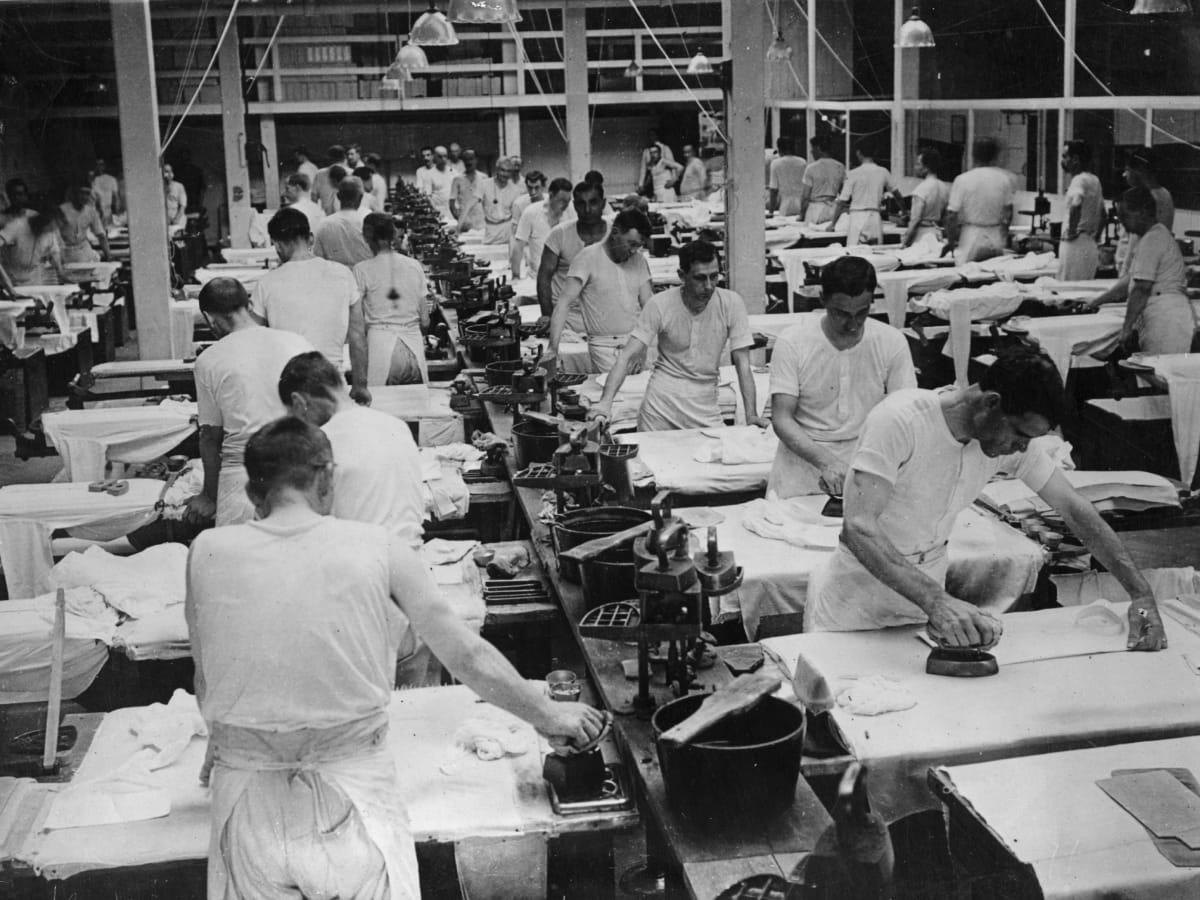
Facility engineers have a variety of jobs. They can be found in manufacturing, construction or office settings. They implement and oversee processes to ensure that facility utilities systems are safe, efficient and effective. Facilities engineers often work closely alongside other engineers and managers, helping to create efficient work routines and deal with any issues that might arise.
Based on the size or type of facility, the duties of a facilities engineering will vary. Typically, the job requires excellent time management skills, problem-solving abilities, and an ability to work well with others. During a typical day, a facilities engineer may perform hundreds of tasks. The engineer is usually responsible for fixing or troubleshooting problems with electrical, mechanical or plumbing equipment.
Many websites offer information and news about the field, including the Association of Facility Engineers' (AFE) website. You can find a sample resume, salary information, and job-related articles on these websites.
Other than these websites, facilities engineers can also read books and articles, participate in training courses, and connect with other engineers. For a successful facility engineer to succeed, you need to have organizational skills and a solid understanding about building and safety codes.
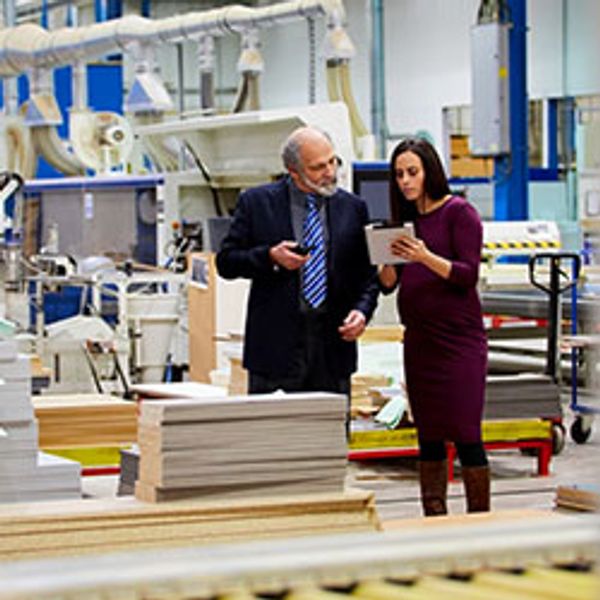
It is important for facilities engineers to be able to simultaneously perform many tasks and analyze data. For this to happen, they will need to have a working knowledge about AutoCAD as well construction techniques such the CAM. Other skills that are beneficial include project management, critical thinking, and problem-solving.
The best thing about a job as a facilities engineer is the ability to work alongside a variety of people. Many of these engineers are trained to work with a variety of different materials and are able to coordinate the work of other engineers.
FAQ
What are the 7 R's of logistics?
The acronym "7R's" of Logistics stands for seven principles that underpin logistics management. It was developed and published by the International Association of Business Logisticians in 2004 as part of the "Seven Principles of Logistics Management".
The acronym is composed of the following letters.
-
Responsible - ensure that actions are in compliance with legal requirements and do not cause harm to others.
-
Reliable - have confidence in the ability to deliver on commitments made.
-
Be responsible - Use resources efficiently and avoid wasting them.
-
Realistic - consider all aspects of operations, including cost-effectiveness and environmental impact.
-
Respectful: Treat others with fairness and equity
-
Reliable - Find ways to save money and increase your productivity.
-
Recognizable - provide customers with value-added services.
What is meant by manufacturing industries?
Manufacturing Industries is a group of businesses that produce goods for sale. These products are sold to consumers. These companies use various processes such as production, distribution, retailing, management, etc., to fulfill this purpose. They produce goods from raw materials by using machines and other machinery. This covers all types of manufactured goods including clothing, food, building supplies and furniture, as well as electronics, tools, machinery, vehicles and pharmaceuticals.
What is production planning?
Production Planning includes planning for all aspects related to production. It is important to have everything ready and planned before you start shooting. This document should include information about how to achieve the best results on-set. This includes shooting schedules, locations, cast lists, crew details, and equipment requirements.
It is important to first outline the type of film you would like to make. You may already know where you want the film to be shot, or perhaps you have specific locations and sets you wish to use. Once you have identified the scenes and locations, you can start to determine which elements are required for each scene. Perhaps you have decided that you need to buy a car but aren't sure which model. You could look online for cars to see what options are available, and then narrow down your choices by selecting between different makes or models.
After you have selected the car you want, you can begin to think about additional features. You might need to have people in the front seats. Maybe you need someone to move around in the back. Perhaps you would like to change the interior colour from black to white. These questions will help determine the look and feel you want for your car. The type of shots that you are looking for is another thing to consider. You will be filming close-ups and wide angles. Maybe you want to show the engine and the steering wheel. These things will help you to identify the car that you are looking for.
Once you have established all the details, you can create a schedule. You will know when you should start and when you should finish shooting. You will need to know when you have to be there, what time you have to leave and when your return home. This way, everyone knows what they need to do and when. Book extra staff ahead of time if you need them. It is not worth hiring someone who won’t show up because you didn’t tell him.
You will need to factor in the days that you have to film when creating your schedule. Some projects take only a few days while others can last several weeks. You should consider whether you will need more than one shot per week when creating your schedule. Multiplying takes in the same area will result both in increased costs and a longer time. It is better to be cautious and take fewer shots than you risk losing money if you are not sure if multiple takes are necessary.
Budget setting is another important aspect in production planning. You will be able to manage your resources if you have a realistic budget. It is possible to reduce the budget at any time if you experience unexpected problems. It is important to not overestimate how much you will spend. If you underestimate how much something costs, you'll have less money to pay for other items.
Planning production is a tedious process. Once you have a good understanding of how everything works together, planning future projects becomes easy.
What do we need to know about Manufacturing Processes in order to learn more about Logistics?
No. No. However, knowing about manufacturing processes will definitely give you a better understanding of how logistics works.
What makes a production planner different from a project manger?
A production planner is more involved in the planning phase of the project than a project manger.
What's the difference between Production Planning & Scheduling?
Production Planning (PP), or production planning, is the process by which you determine what products are needed at any given time. Forecasting demand is one way to do this.
Scheduling is the process that assigns dates to tasks so they can get completed within a given timeframe.
Statistics
- You can multiply the result by 100 to get the total percent of monthly overhead. (investopedia.com)
- (2:04) MTO is a production technique wherein products are customized according to customer specifications, and production only starts after an order is received. (oracle.com)
- It's estimated that 10.8% of the U.S. GDP in 2020 was contributed to manufacturing. (investopedia.com)
- Job #1 is delivering the ordered product according to specifications: color, size, brand, and quantity. (netsuite.com)
- According to a Statista study, U.S. businesses spent $1.63 trillion on logistics in 2019, moving goods from origin to end user through various supply chain network segments. (netsuite.com)
External Links
How To
How to Use 5S to Increase Productivity in Manufacturing
5S stands for "Sort", 'Set In Order", 'Standardize', & Separate>. Toyota Motor Corporation invented the 5S strategy in 1954. It assists companies in improving their work environments and achieving higher efficiency.
The basic idea behind this method is to standardize production processes, so they become repeatable, measurable, and predictable. This means that every day tasks such cleaning, sorting/storing, packing, and labeling can be performed. Workers can be more productive by knowing what to expect.
There are five steps to implementing 5S, including Sort, Set In Order, Standardize, Separate and Store. Each step has a different action and leads to higher efficiency. If you sort items, it makes them easier to find later. When items are ordered, they are put together. You then organize your inventory in groups. Finally, when you label your containers, you ensure everything is labeled correctly.
Employees need to reflect on how they do their jobs. Employees need to understand the reasons they do certain jobs and determine if there is a better way. They must learn new skills and techniques in order to implement the 5S system.
In addition to increasing efficiency, the 5S method also improves morale and teamwork among employees. Once they start to notice improvements, they are motivated to keep working towards their goal of increasing efficiency.