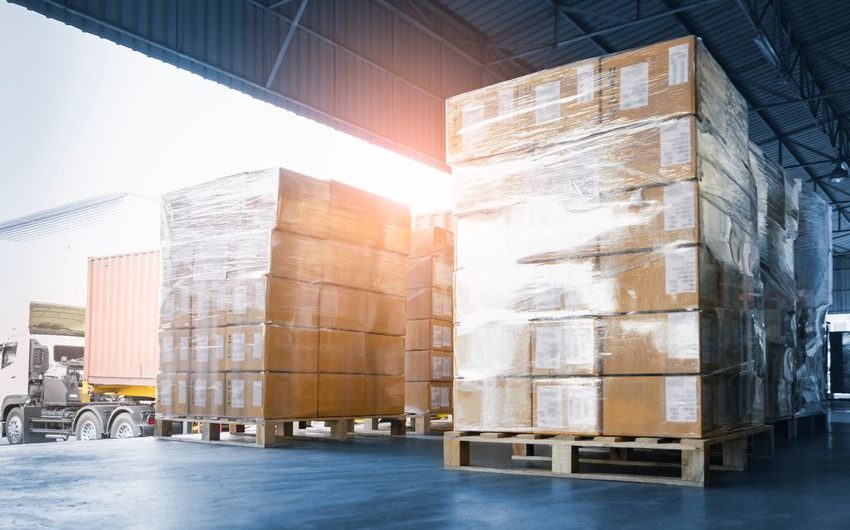
Andon, in the world of lean production, is a visual sign that highlights and draws attention to issues with the intention of solving them permanently. It's an instrument that empowers operators on the production floor and speeds up teamwork.
Andon
) is a Japanese-derived word, which comes from the fixed paper lanterns used between the Edo period (17th century to 19th century). In Japanese it can also refer to the system of attaching light signals and sounds to specific processes in order to alert employees.
Toyota uses this term to describe its Jidoka (or build-in quality), which is a major component of the TPS (Toyota Production System). It is often cited in the US as the origin of a concept which allows employees on the production line to stop it if there are safety or quality problems.
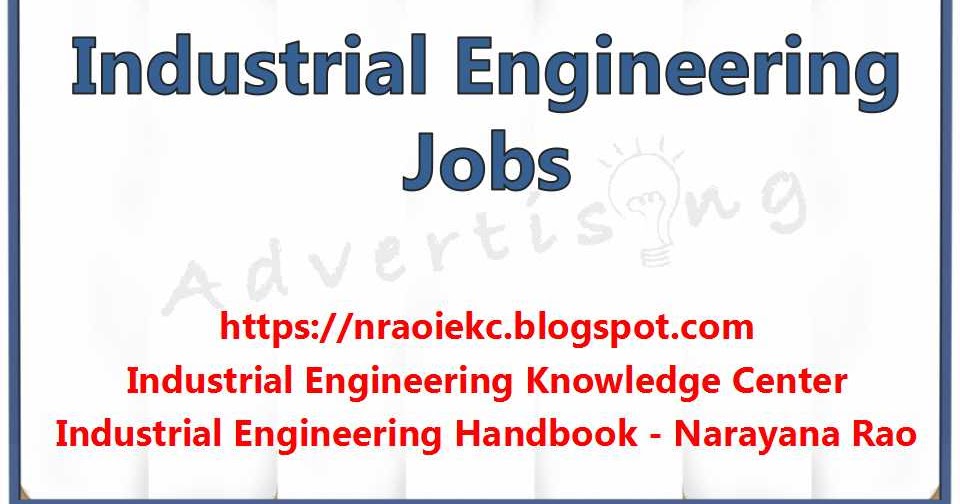
What is Andon?
Toyota was the first to introduce Andon, a lean-manufacturing system. It is a simple system that consists of a board with green, yellow and red lights. Each color indicates the different status of production. When the light is green, production is proceeding normally. The yellow light indicates that a problem was found and is currently being resolved. When the red light is lit, all production stops. Workers can take a break, prepare parts, go to help or fill their bins, etc.
Andon's board is simple to operate and supervisors understand exactly what has occurred. The system provides immediate feedback to ensure that any problems are dealt with as soon as they arise.
There are a variety of types of andons. But the most common is an alerting red light accompanied by a buzzer. These systems can be used to identify issues that may cause downtime or repeat problems.
When a problem occurs, a good andonboard can keep production running. It's a simple, effective tool to increase productivity, reduce downtime, and improve product quality.
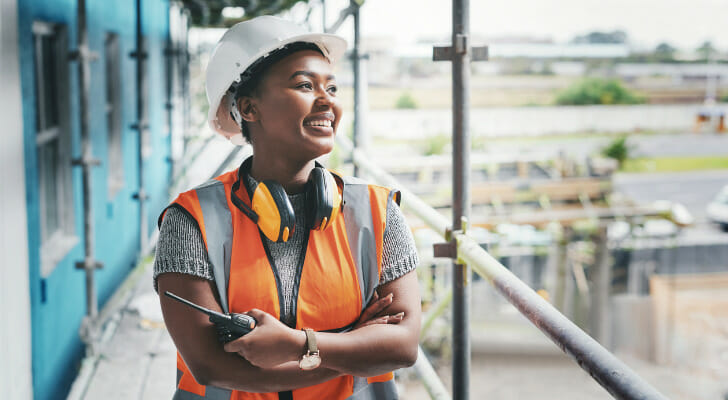
What is andon toyota?
Toyota had a cord that employees could pull on the production floor if they suspected a problem with a car. The cord was used by workers to stop production if they thought the car's integrity had been compromised.
In a similar way, modern andon system use technology in order to present curated data that helps to identify emerging issues, push notifications to stakeholder in real time and identify the underlying cause that requires a longer-term solution. Human touch is essential to interpret and act upon this information.
How to make the andon system work?
First, it's crucial to create an environment where employees and managers do not hesitate to identify or address problems. The more hesitant they are, the more likely they will hide problems and miss an opportunity to resolve them. The quickest way to improve this is to tie line stops to problem resolution, so that workers are more likely to hit the button and pull the cord when they see something amiss.
FAQ
How can overproduction in manufacturing be reduced?
It is essential to find better ways to manage inventory to reduce overproduction. This would reduce the amount of time spent on unnecessary activities such as purchasing, storing, and maintaining excess stock. This could help us free up our time for other productive tasks.
You can do this by adopting a Kanban method. A Kanban board is a visual display used to track work in progress. Kanban systems allow work items to move through different states until they reach their final destination. Each state represents a different priority level.
When work is completed, it can be transferred to the next stage. But if a task remains in the beginning stages it will stay that way until it reaches its end.
This allows for work to continue moving forward, while also ensuring that there is no work left behind. Managers can monitor the work being done by Kanban boards to see what is happening at any given time. This allows them to adjust their workflows based on real-time information.
Lean manufacturing can also be used to reduce inventory levels. Lean manufacturing works to eliminate waste throughout every stage of the production chain. Anything that does not contribute to the product's value is considered waste. The following are examples of common waste types:
-
Overproduction
-
Inventory
-
Packaging that is not necessary
-
Overstock materials
These ideas will help manufacturers increase efficiency and lower costs.
What is production planning?
Production Planning is the creation of a plan to cover all aspects, such as scheduling, budgeting. Location, crew, equipment, props and other details. It is important to have everything ready and planned before you start shooting. It should also provide information about how best to produce the best results while on set. This information includes locations, crew details and equipment requirements.
First, you need to plan what you want to film. You may already know where you want the film to be shot, or perhaps you have specific locations and sets you wish to use. Once you have identified the scenes and locations, you can start to determine which elements are required for each scene. If you decide you need a car and don't know what model to choose, this could be an example. To narrow your options, you can search online for available models.
After you have chosen the right car, you will be able to begin thinking about accessories. Do you need people sitting in the front seats? Perhaps you have someone who needs to be able to walk around the back of your car. You may want to change the interior's color from black or white. These questions will help determine the look and feel you want for your car. You can also think about the type of shots you want to get. Are you going to be shooting close-ups? Or wide angles? Maybe the engine or steering wheel is what you are looking to film. This will allow you to determine the type of car you want.
Once you've determined the above, it is time to start creating a calendar. A schedule will tell you when you need to start shooting and when you need to finish. A schedule for each day will detail when you should arrive at the location and when you need leave. Everyone knows exactly what they should do and when. It is possible to make arrangements in advance for additional staff if you are looking to hire. It's not worth paying someone to show up if you haven't told him.
It is important to calculate the amount of filming days when you are creating your schedule. Some projects take only a few days while others can last several weeks. While creating your schedule, it is important to remember whether you will require more than one shot per day. Shooting multiple takes over the same location will increase costs and take longer to complete. You can't be certain if you will need multiple takes so it is better not to shoot too many.
Budgeting is another important aspect of production planning. Setting a realistic budget is essential as it will allow you to work within your means. If you have to reduce your budget due to unexpected circumstances, you can always lower it later. But, don't underestimate how much money you'll spend. You will end up spending less money if you underestimate the cost of something.
Production planning is a very detailed process, but once you understand how everything works together, it becomes easier to plan future projects.
Why is logistics important in manufacturing
Logistics are an integral part any business. They are essential to any business's success.
Logistics are also important in reducing costs and improving efficiency.
What are the responsibilities of a manufacturing manager
A manufacturing manager must make sure that all manufacturing processes run smoothly and effectively. They should also be aware and responsive to any company problems.
They should also be able communicate with other departments, such as sales or marketing.
They should also be aware of the latest trends in their industry and be able to use this information to help improve productivity and efficiency.
How does a production planner differ from a project manager?
The main difference between a production planner and a project manager is that a project manager is usually the person who plans and organizes the entire project, whereas a production planner is mainly involved in the planning stage of the project.
Statistics
- Many factories witnessed a 30% increase in output due to the shift to electric motors. (en.wikipedia.org)
- It's estimated that 10.8% of the U.S. GDP in 2020 was contributed to manufacturing. (investopedia.com)
- [54][55] These are the top 50 countries by the total value of manufacturing output in US dollars for its noted year according to World Bank.[56] (en.wikipedia.org)
- In the United States, for example, manufacturing makes up 15% of the economic output. (twi-global.com)
- According to the United Nations Industrial Development Organization (UNIDO), China is the top manufacturer worldwide by 2019 output, producing 28.7% of the total global manufacturing output, followed by the United States, Japan, Germany, and India.[52][53] (en.wikipedia.org)
External Links
How To
How to use the Just-In Time Method in Production
Just-intime (JIT), a method used to lower costs and improve efficiency in business processes, is called just-in-time. It's a way to ensure that you get the right resources at just the right time. This means that you only pay for what you actually use. Frederick Taylor developed the concept while working as foreman in early 1900s. After observing how workers were paid overtime for late work, he realized that overtime was a common practice. He decided that workers would be more productive if they had enough time to complete their work before they started to work.
JIT teaches you to plan ahead and prepare everything so you don’t waste time. You should also look at the entire project from start to finish and make sure that you have sufficient resources available to deal with any problems that arise during the course of your project. If you anticipate that there might be problems, you'll have enough people and equipment to fix them. This way, you won't end up paying extra money for things that weren't really necessary.
There are many JIT methods.
-
Demand-driven: This JIT is where you place regular orders for the parts/materials that are needed for your project. This will allow you to track how much material you have left over after using it. This will allow to you estimate the time it will take for more to be produced.
-
Inventory-based: This type allows you to stock the materials needed for your projects ahead of time. This allows for you to anticipate how much you can sell.
-
Project-driven: This method allows you to set aside enough funds for your project. Once you have an idea of how much material you will need, you can purchase the necessary materials.
-
Resource-based: This is the most common form of JIT. This is where you assign resources based upon demand. You might assign more people to help with orders if there are many. If you don't receive many orders, then you'll assign fewer employees to handle the load.
-
Cost-based : This is similar in concept to resource-based. But here, you aren't concerned about how many people your company has but how much each individual costs.
-
Price-based: This is similar to cost-based but instead of looking at individual workers' salaries, you look at the total company price.
-
Material-based: This is very similar to cost-based but instead of looking at total costs of the company you are concerned with how many raw materials you use on an average.
-
Time-based: Another variation of resource-based JIT. Instead of focusing solely on the amount each employee costs, focus on how long it takes for the project to be completed.
-
Quality-based JIT is another variant of resource-based JIT. Instead of looking at the labor costs and time it takes to make a product, think about its quality.
-
Value-based JIT is the newest form of JIT. In this instance, you are not concerned about the product's performance or meeting customer expectations. Instead, you're focused on how much value you add to the market.
-
Stock-based: This inventory-based approach focuses on how many items are being produced at any one time. This is used to increase production and minimize inventory.
-
Just-in time (JIT), planning: This is a combination JIT/supply chain management. It is the process of scheduling components' delivery as soon as they have been ordered. It's important because it reduces lead times and increases throughput.