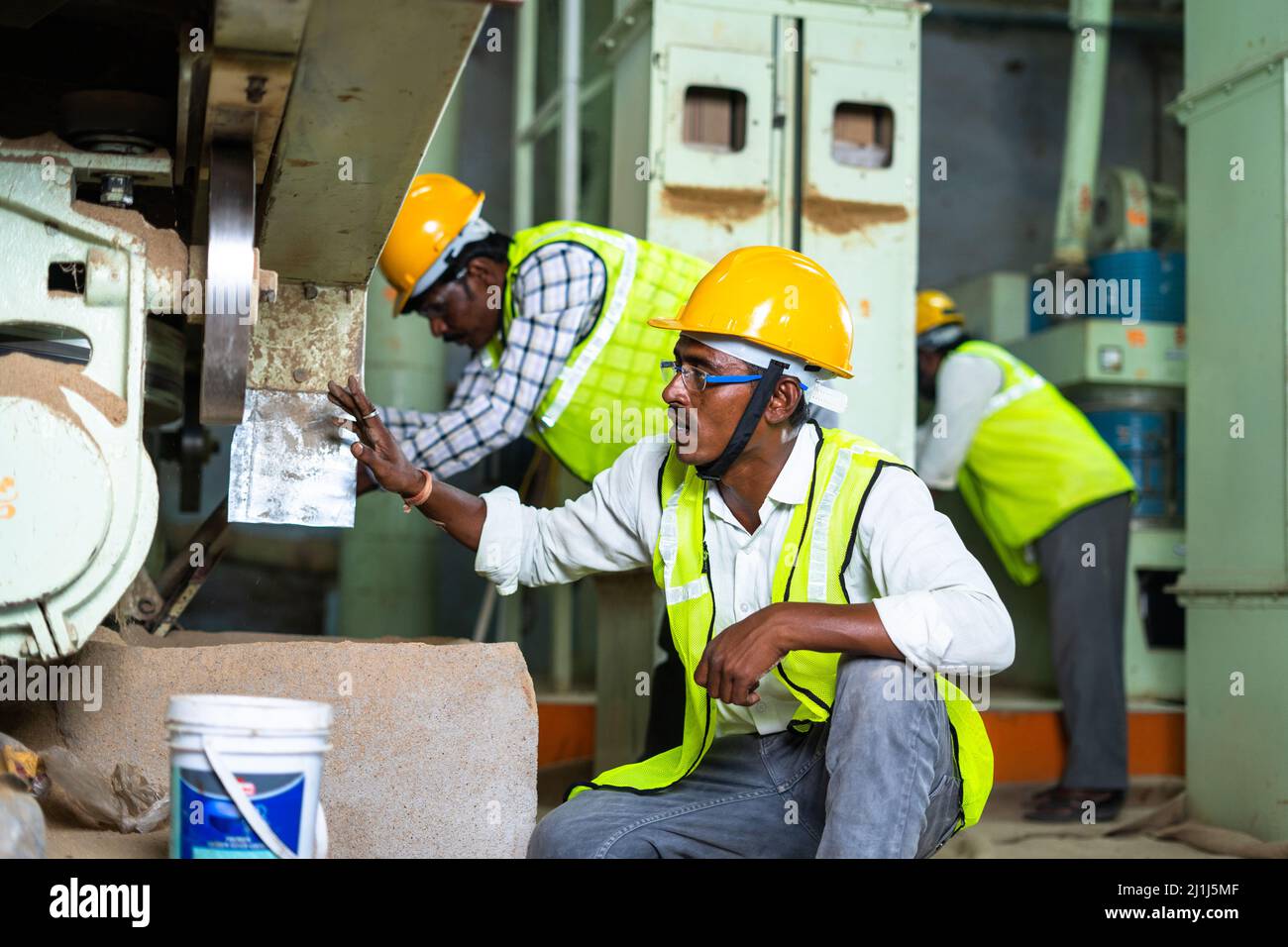
Columbus, Ohio is central Ohio's largest city has a wide range of activities and attractions. Columbus is a tourist hotspot with four world-class golf courses, a highly acclaimed park system, and an array of arts and entertainment. It is also ranked among America's most charming metropolitan areas. It also has a lot of high-tech firms that make it stand out on the corporate radar. Check out the Columbus Tech Council website for a complete list of local tech companies. The council is your one-stop shop for everything tech related, including job openings and networking opportunities. Whether you're in the market for a career move, or just looking for a change of scenery, the Columbus tech scene is sure to please. Columbus offers everything you need, whether you are looking for a job as an entry-level employee or a senior executive position. You will find a variety of employers looking to hire you in the city, such as JP Morgan, Limited Brands, Time Warner and JP Morgan. Columbus is home to many art galleries and museums, including the Franklin Park Conservatory. These are not to mention the many theaters and casinos. The city also has one of the best public transportation systems in America.
FAQ
What are the 7 Rs of logistics?
The acronym 7Rs of Logistics refers to the seven core principles of logistics management. It was developed and published by the International Association of Business Logisticians in 2004 as part of the "Seven Principles of Logistics Management".
The following letters make up the acronym:
-
Responsible - ensure that all actions taken are within legal requirements and are not harmful to others.
-
Reliable – have faith in your ability and capability to keep promises.
-
It is reasonable to use resources efficiently and not waste them.
-
Realistic – consider all aspects of operations, from cost-effectiveness to environmental impact.
-
Respectful - show respect and treat others fairly and fairly
-
Be resourceful: Look for opportunities to save money or increase productivity.
-
Recognizable provides value-added products and services to customers
Can we automate some parts of manufacturing?
Yes! Since ancient times, automation has been in existence. The Egyptians created the wheel thousands years ago. We now use robots to help us with assembly lines.
In fact, there are several applications of robotics in manufacturing today. These include:
-
Line robots
-
Robot welding
-
Robot painting
-
Robotics inspection
-
Robots that create products
Automation can be applied to manufacturing in many other ways. For example, 3D printing allows us to make custom products without having to wait for weeks or months to get them manufactured.
What are the jobs in logistics?
There are many jobs available in logistics. Some examples are:
-
Warehouse workers – They load and unload pallets and trucks.
-
Transportation drivers – These drivers drive trucks and wagons to transport goods and pick up the goods.
-
Freight handlers, - They sort out and pack freight in warehouses.
-
Inventory managers – These people oversee inventory at warehouses.
-
Sales representatives: They sell products to customers.
-
Logistics coordinators – They plan and coordinate logistics operations.
-
Purchasing agents - They buy goods and services that are necessary for company operations.
-
Customer service representatives are available to answer customer calls and emails.
-
Shipping clerks: They process shipping requests and issue bills.
-
Order fillers - These people fill orders based on what has been ordered.
-
Quality control inspectors – They inspect incoming and outgoing products to ensure that there are no defects.
-
Others - There are many other types of jobs available in logistics, such as transportation supervisors, cargo specialists, etc.
What is the job of a production plan?
A production planner makes sure all project elements are delivered on schedule, within budget, as well as within the agreed scope. They ensure that the product or service is of high quality and meets client requirements.
What's the difference between Production Planning & Scheduling?
Production Planning (PP) is the process of determining what needs to be produced at any given point in time. This is accomplished by forecasting the demand and identifying production resources.
Scheduling involves the assignment of dates and times to tasks in order to complete them within the timeframe.
What is meant by manufacturing industries?
Manufacturing Industries are companies that manufacture products. These products are sold to consumers. These companies use various processes such as production, distribution, retailing, management, etc., to fulfill this purpose. They make goods from raw materials with machines and other equipment. This includes all types if manufactured goods.
What is production plan?
Production Planning refers to the development of a plan for every aspect of production. This document aims to ensure that everything is planned and ready when you are ready to shoot. This document should also include information on how to get the best result on set. This information includes locations, crew details and equipment requirements.
The first step in filming is to define what you want. You may already know where you want the film to be shot, or perhaps you have specific locations and sets you wish to use. Once you have identified the scenes and locations, you can start to determine which elements are required for each scene. You might decide you need a car, but not sure what make or model. In this case, you could start looking up cars online to find out what models are available and then narrow your choices by choosing between different makes and models.
After you have chosen the right car, you will be able to begin thinking about accessories. Do you need people sitting in the front seats? Or perhaps you need someone walking around the back of the car? Maybe you'd like to change the interior from black to a white color. These questions will help determine the look and feel you want for your car. It is also worth considering the types of shots that you wish to take. Are you going to be shooting close-ups? Or wide angles? Maybe you want to show your engine or the steering wheel. These things will help you to identify the car that you are looking for.
Once you've determined the above, it is time to start creating a calendar. You can use a schedule to determine when and where you need it to be shot. Each day will include the time when you need to arrive at the location, when you need to leave and when you need to return home. Everyone knows exactly what they should do and when. Hire extra staff by booking them ahead of time. There is no point in hiring someone who won't turn up because you didn't let him know.
Also, consider how many days you will be filming your schedule. Some projects can be completed in a matter of days or weeks. Others may take several days. It is important to consider whether you require more than one photo per day when you create your schedule. Multiple shots at the same location can increase costs and make it more difficult to complete. You can't be certain if you will need multiple takes so it is better not to shoot too many.
Another important aspect of production planning is setting budgets. You will be able to manage your resources if you have a realistic budget. Remember that you can always reduce the budget later on if you run into unforeseen problems. It is important to not overestimate how much you will spend. If you underestimate the cost of something, you will have less money left after paying for other items.
Planning production is a tedious process. Once you have a good understanding of how everything works together, planning future projects becomes easy.
Statistics
- (2:04) MTO is a production technique wherein products are customized according to customer specifications, and production only starts after an order is received. (oracle.com)
- In 2021, an estimated 12.1 million Americans work in the manufacturing sector.6 (investopedia.com)
- In the United States, for example, manufacturing makes up 15% of the economic output. (twi-global.com)
- According to a Statista study, U.S. businesses spent $1.63 trillion on logistics in 2019, moving goods from origin to end user through various supply chain network segments. (netsuite.com)
- Job #1 is delivering the ordered product according to specifications: color, size, brand, and quantity. (netsuite.com)
External Links
How To
Six Sigma in Manufacturing
Six Sigma is defined by "the application SPC (statistical process control) techniques to achieve continuous improvements." Motorola's Quality Improvement Department, Tokyo, Japan, developed it in 1986. Six Sigma's main goal is to improve process quality by standardizing processes and eliminating defects. Since there are no perfect products, or services, this approach has been adopted by many companies over the years. Six Sigma's main objective is to reduce variations from the production average. This means that you can take a sample from your product and then compare its performance to the average to find out how often the process differs from the norm. If it is too large, it means that there are problems.
Understanding the nature of variability in your business is the first step to Six Sigma. Once you understand that, it is time to identify the sources of variation. These variations can also be classified as random or systematic. Random variations are caused by human errors. Systematic variations can be caused by outside factors. These are, for instance, random variations that occur when widgets are made and some fall off the production line. You might notice that your widgets always fall apart at the same place every time you put them together.
Once you've identified where the problems lie, you'll want to design solutions to eliminate those problems. You might need to change the way you work or completely redesign the process. Test them again once you've implemented the changes. If they don't work, you will need to go back to the drawing boards and create a new plan.