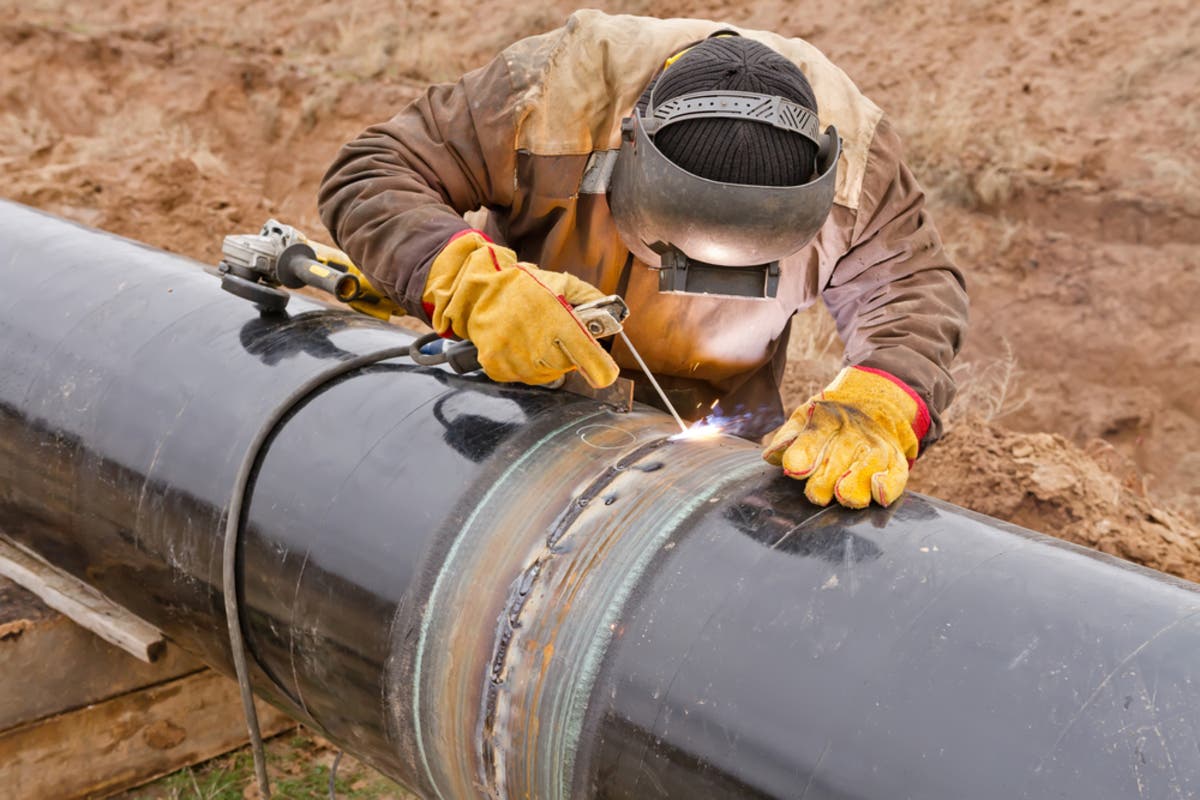
Supply chain management software will help you improve your efficiency and streamline your processes, no matter if you work for a large corporation or small business. These systems can give you a central view to your entire supply network, allowing for planning production, shipment planning, as well as delivery routes. These systems can automate and streamline processes so that employees can focus on other areas of their business. Every organization that manages shipping and manufacturing is going to need supply chain management software.
You must consider many capabilities and features in order to find the best supply management software. These include scalability. ease of use. And integration with other programs. You should also consider the provider's reputation and the features they offer. Also, make sure you choose a solution that is within your financial budget. You should also consider whether you want a SaaS package or a full-scale plan. This will allow you to adjust as your business grows.
E2open is a leading provider of supply chain management software. It specializes in cloud-based solutions that provide better demand forecasting, operations management, and other benefits. The company also offers advanced features and a technology platform. The software is designed for businesses in a variety of industries, including retail, transportation, and manufacturing.

Real-time visibility is an important feature of supply chain software. This allows you to monitor your inventory and track your products. It helps you ensure that your customers have what they need when they need it. It also helps you develop long-term strategies for managing demand-supply balance.
Kinaxis is a complete supply chain management solution that eliminates silos and streamlines processes. It combines human and machine intelligence to help you make better decisions. It can help you plan inventory and capacities so that you can respond better to opportunities.
This software can be used to forecast sales and helps you understand historical sales cycles and seasonality. It also makes use of machine learning to predict future sales. This software can help you forecast your sales and prepare your sales team for the future. You also have access to data from multiple sources so you can see the whole picture of your business.
Descartes Systems Group is the largest competitor in supply-chain management software. They are the top vendor for many organizations. This company has over 13,000 customers and products that compete with SAP SCM.
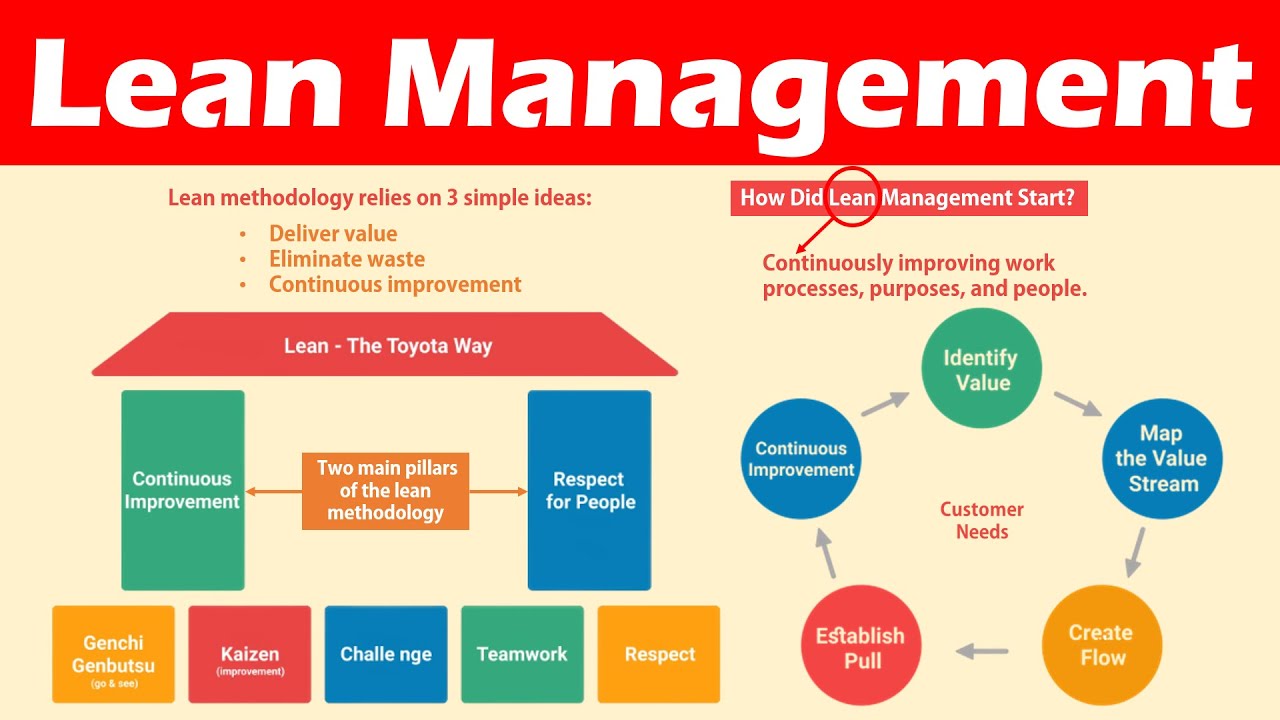
Manhattan Associates is another competitor to supply-chain management software. Manhattan Associates is a software company with thousands of users. Its revenue is approximately $617.5million. Eddie Capel runs the company. This company competes in the market against Logility, JDA, and Infor SCM.
Infor SCM, a supply chain management software platform, is one of the most popular. It's ideal for all businesses and is one of the most well-known supply chain management software solutions. It's a cloud-based application that unifies all enterprise processes. It also includes analytics at the core, which can help you optimize your end-to-end supply chain.
FAQ
What types of jobs can you find in logistics
There are different kinds of jobs available in logistics. Here are some examples:
-
Warehouse workers - They load and unload trucks and pallets.
-
Transportation drivers – They drive trucks or trailers to transport goods and perform pick-ups.
-
Freight handlers, - They sort out and pack freight in warehouses.
-
Inventory managers - They oversee the inventory of goods in warehouses.
-
Sales representatives - They sell products to customers.
-
Logistics coordinators are responsible for organizing and planning logistics operations.
-
Purchasing agents - They purchase goods and services needed for company operations.
-
Customer service representatives are available to answer customer calls and emails.
-
Shippers clerks - They process shipping order and issue bills.
-
Order fillers - They fill orders based on what is ordered and shipped.
-
Quality control inspectors – They inspect incoming and outgoing products to ensure that there are no defects.
-
Others - There are many types of jobs in logistics such as transport supervisors and cargo specialists.
What are the 7 Rs of logistics management?
The acronym 7R's for Logistics stands to represent the seven basic principles in logistics management. It was developed by International Association of Business Logisticians (IABL), and published as part of their "Seven Principles of Logistics Management Series" in 2004.
The acronym is composed of the following letters.
-
Responsible - ensure that actions are in compliance with legal requirements and do not cause harm to others.
-
Reliable - have confidence in the ability to deliver on commitments made.
-
Use resources effectively and sparingly.
-
Realistic - Consider all aspects of operations, including environmental impact and cost effectiveness.
-
Respectful - Treat people fairly and equitably
-
Reliable - Find ways to save money and increase your productivity.
-
Recognizable - provide customers with value-added services.
What is the role and responsibility of a Production Planner?
Production planners ensure that all project aspects are completed on time, within budget and within the scope. A production planner ensures that the service and product meet the client's expectations.
What is the best way to learn about manufacturing?
Hands-on experience is the best way to learn more about manufacturing. You can read books, or watch instructional videos if you don't have the opportunity to do so.
Do we need to know about Manufacturing Processes before learning about Logistics?
No. No. But, being familiar with manufacturing processes will give you a better understanding about how logistics works.
What skills do production planners need?
Production planners must be flexible, organized, and able handle multiple tasks. Effective communication with clients and colleagues is essential.
Statistics
- It's estimated that 10.8% of the U.S. GDP in 2020 was contributed to manufacturing. (investopedia.com)
- According to the United Nations Industrial Development Organization (UNIDO), China is the top manufacturer worldwide by 2019 output, producing 28.7% of the total global manufacturing output, followed by the United States, Japan, Germany, and India.[52][53] (en.wikipedia.org)
- (2:04) MTO is a production technique wherein products are customized according to customer specifications, and production only starts after an order is received. (oracle.com)
- In 2021, an estimated 12.1 million Americans work in the manufacturing sector.6 (investopedia.com)
- [54][55] These are the top 50 countries by the total value of manufacturing output in US dollars for its noted year according to World Bank.[56] (en.wikipedia.org)
External Links
How To
How to Use the Just In Time Method in Production
Just-intime (JIT), which is a method to minimize costs and maximize efficiency in business process, is one way. It's the process of obtaining the right amount and timing of resources when you need them. This means that you only pay the amount you actually use. The term was first coined by Frederick Taylor, who developed his theory while working as a foreman in the early 1900s. He saw how overtime was paid to workers for work that was delayed. He decided to ensure workers have enough time to do their jobs before starting work to improve productivity.
JIT is an acronym that means you need to plan ahead so you don’t waste your money. You should also look at the entire project from start to finish and make sure that you have sufficient resources available to deal with any problems that arise during the course of your project. You can anticipate problems and have enough equipment and people available to fix them. You won't have to pay more for unnecessary items.
There are many JIT methods.
-
Demand-driven: This type of JIT allows you to order the parts/materials required for your project on a regular basis. This will allow to track how much material has been used up. It will also allow you to predict how long it takes to produce more.
-
Inventory-based: You stock materials in advance to make your projects easier. This allows for you to anticipate how much you can sell.
-
Project-driven: This approach involves setting aside sufficient funds to cover your project's costs. When you know how much you need, you'll purchase the appropriate amount of materials.
-
Resource-based JIT: This is the most popular form of JIT. You assign certain resources based off demand. For example, if there is a lot of work coming in, you will have more people assigned to them. If you don't receive many orders, then you'll assign fewer employees to handle the load.
-
Cost-based: This approach is very similar to resource-based. However, you don't just care about the number of people you have; you also need to consider how much each person will cost.
-
Price-based: This approach is very similar to the cost-based method except that you don't look at individual workers costs but the total cost of the company.
-
Material-based: This approach is similar to cost-based. However, instead of looking at the total cost for the company, you look at how much you spend on average on raw materials.
-
Time-based JIT: A variation on resource-based JIT. Instead of focusing only on how much each employee is costing, you should focus on how long it takes to complete your project.
-
Quality-based JIT - This is another form of resource-based JIT. Instead of looking at the labor costs and time it takes to make a product, think about its quality.
-
Value-based JIT: One of the most recent forms of JIT. In this instance, you are not concerned about the product's performance or meeting customer expectations. Instead, your focus is on the value you bring to the market.
-
Stock-based: This stock-based method focuses on the actual quantity of products being made at any given time. This method is useful when you want to increase production while decreasing inventory.
-
Just-in-time (JIT) planning: This is a combination of JIT and supply chain management. It is the process of scheduling components' delivery as soon as they have been ordered. It's important as it reduces leadtimes and increases throughput.