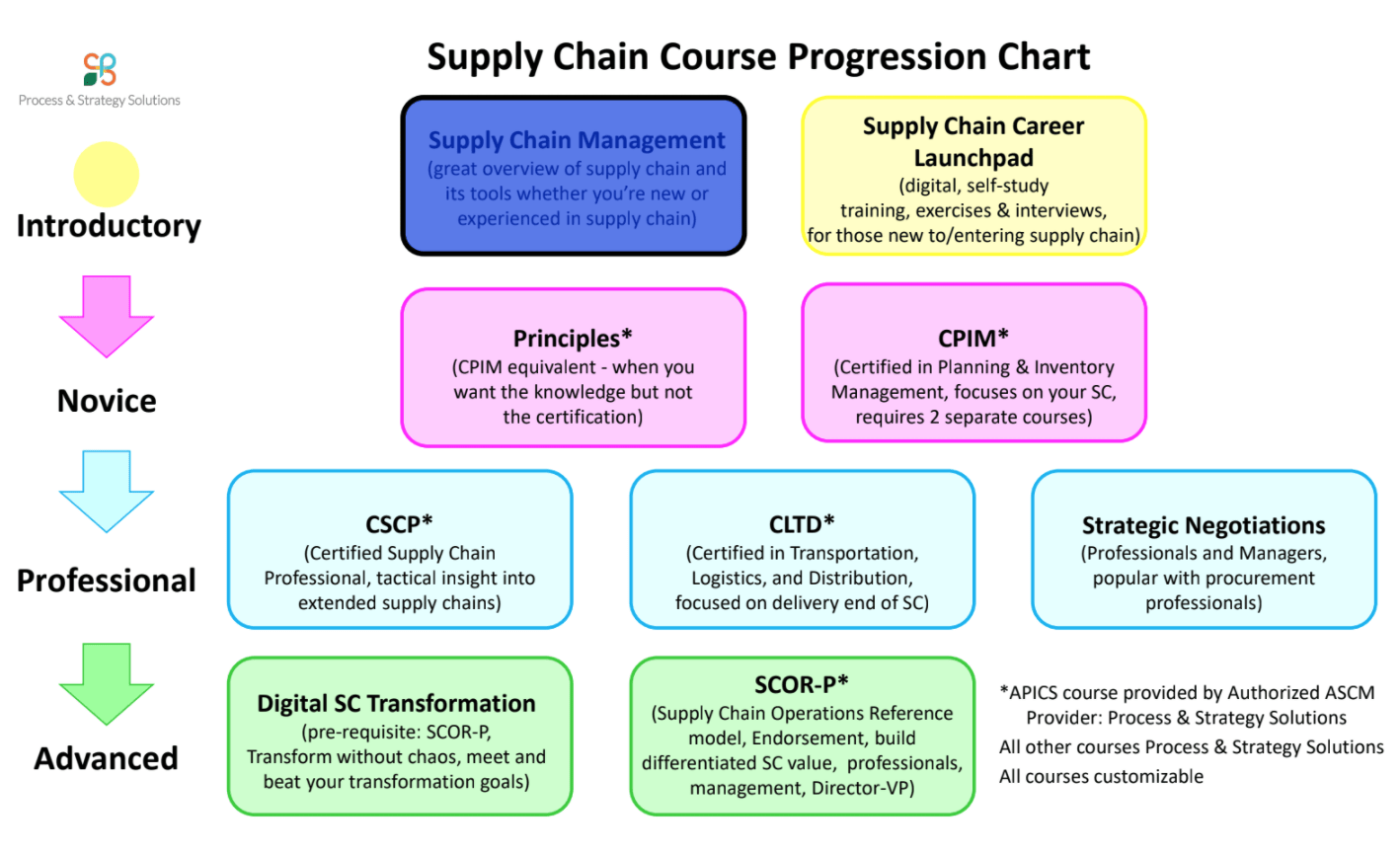
The manufacturing sector is experiencing rapid changes. This requires new skills, and cutting-edge knowledge. The factory of tomorrow will be digital and flexible, efficient, responsible, and accountable. The factory of the future will be digital, flexible, responsible, efficient, and sustainable. Manufacturing engineers are at the forefront. Here are three areas of expertise that you need to master. These key skills are essential for your industry's future success.
Analyst perspectives
Analyst perspectives on industry future are important for understanding current trends and assessing the industry's competitive dynamics. These insights can provide insight into changing consumer behavior, such as attitudes and intentions. NPD has conducted an annual survey of the industry to get a clear picture of its outlook. Each country has its own forecasted categories. This chapter examines industry analysts' role in validating market-based data.
Consumer survey data
Prosper collects responses from approximately seven thousand adult respondents each month. It is trended and correlated, and includes questions about consumers' emotional state, future plans, and purchasing habits. The archive also contains monthly data over 18 years on hundreds of major retailers. It's the best way to understand the underlying attitudes and spending habits of consumers in a specific market. Marketing and business leaders can use the survey data to make informed decisions.
Trends in industry growth
This chapter focuses on the growth patterns of industries and firms. The speed of industry growth depends on the extent to which financial markets are developed in advanced countries. Financially-hungry industries grow faster in countries that have developed financial markets. Sectors that depend on foreign finance also grow faster during periods of high stock market performance. These patterns align with theories related to trade and development. They suggest that the product mix of a country reflects its economic status. We will discuss here the main trends and drivers that affect industry growth.
Automation
Gartner estimates that automation will be a major factor in almost every occupation over the next ten years. While automation can only be achieved in five percent, there are many other activities that could be automated. Most occupations will be affected at some point, and the nature of these jobs may change. The workplace will determine whether or not they adapt to change. Here are five ways automation can impact the manufacturing sector.
Hybrid workplace
Companies should listen to employees and offer multiple ways for them to share their feedback in order to create a hybrid workplace. To gather valuable information, they can use focus groups or human resources surveys. They can also give employees performance incentives such as financial rewards, food deliveries, or tokens of appreciation. Companies can listen to employees and ensure that the transition to the new environment is smooth. This will create a positive experience for all.
Streaming media
The Streaming media industry is a new business model, and its future is far from certain. Many media conglomerates are now selling short-term streaming rights to three services. Although streaming was a small market at first, it is now a booming industry that is poised to surpass linear television as the leading viewing option in the next few years. In 2025, almost every production of the four media conglomerates should only be available through their streaming services.
Automotive industry
What are the prospects for the Automotive Industry's future? Experts believe it will gradually recover over the next decade. Automakers face many problems right now. However, new technologies such as connected cars could provide new income streams. The government can make emission laws more flexible, while automotive companies can increase their resilience and expand R&D. There are several reasons why the Automotive Industry could start to recover slowly over the coming decade.
FAQ
What jobs are available in logistics?
There are many types of jobs in logistics. Some examples are:
-
Warehouse workers – They load and unload pallets and trucks.
-
Transportation drivers – They drive trucks or trailers to transport goods and perform pick-ups.
-
Freight handlers – They sort and package freight at warehouses.
-
Inventory managers: They are responsible for the inventory and management of warehouses.
-
Sales reps are people who sell products to customers.
-
Logistics coordinators - They organize and plan logistics operations.
-
Purchasing agents are those who purchase goods and services for the company.
-
Customer service representatives – They answer emails and phone calls from customers.
-
Shippers clerks - They process shipping order and issue bills.
-
Order fillers - These people fill orders based on what has been ordered.
-
Quality control inspectors – They inspect incoming and outgoing products to ensure that there are no defects.
-
Others - There are many other types of jobs available in logistics, such as transportation supervisors, cargo specialists, etc.
How can manufacturing reduce production bottlenecks?
To avoid production bottlenecks, ensure that all processes run smoothly from the moment you receive your order to the time the product ships.
This includes both quality control and capacity planning.
Continuous improvement techniques such Six Sigma are the best method to accomplish this.
Six Sigma can be used to improve the quality and decrease waste in all areas of your company.
It's all about eliminating variation and creating consistency in work.
Do we need to know about Manufacturing Processes before learning about Logistics?
No. No. However, knowing about manufacturing processes will definitely give you a better understanding of how logistics works.
How can I learn about manufacturing?
Experience is the best way for you to learn about manufacturing. You can also read educational videos or take classes if this isn't possible.
What are the products of logistics?
Logistics refers to all activities that involve moving goods from A to B.
They encompass all aspects transport, including packaging and loading, transporting, storage, unloading.
Logisticians ensure that the right product reaches the right place at the right time and under safe conditions. They assist companies with their supply chain efficiency through information on demand forecasts. Stock levels, production times, and availability.
They monitor shipments in transit, ensure quality standards, manage inventories, replenish orders, coordinate with suppliers and other vendors, and offer support services for sales, marketing, and customer service.
How important is automation in manufacturing?
Automation is important not only for manufacturers but also for service providers. Automation allows them to deliver services quicker and more efficiently. It reduces human errors and improves productivity, which in turn helps them lower their costs.
What do you mean by warehouse?
A warehouse, or storage facility, is where goods are stored prior to being sold. It can be an outdoor or indoor area. In some cases, it may be a combination of both.
Statistics
- It's estimated that 10.8% of the U.S. GDP in 2020 was contributed to manufacturing. (investopedia.com)
- According to a Statista study, U.S. businesses spent $1.63 trillion on logistics in 2019, moving goods from origin to end user through various supply chain network segments. (netsuite.com)
- According to the United Nations Industrial Development Organization (UNIDO), China is the top manufacturer worldwide by 2019 output, producing 28.7% of the total global manufacturing output, followed by the United States, Japan, Germany, and India.[52][53] (en.wikipedia.org)
- [54][55] These are the top 50 countries by the total value of manufacturing output in US dollars for its noted year according to World Bank.[56] (en.wikipedia.org)
- In 2021, an estimated 12.1 million Americans work in the manufacturing sector.6 (investopedia.com)
External Links
How To
How to use Lean Manufacturing in the production of goods
Lean manufacturing refers to a method of managing that seeks to improve efficiency and decrease waste. It was first developed in Japan in the 1970s/80s by Taiichi Ahno, who was awarded the Toyota Production System (TPS), award from KanjiToyoda, the founder of TPS. Michael L. Watkins published the first book on lean manufacturing in 1990.
Lean manufacturing is often defined as a set of principles used to improve the quality, speed, and cost of products and services. It emphasizes eliminating waste and defects throughout the value stream. The five-steps of Lean Manufacturing are just-in time (JIT), zero defect and total productive maintenance (TPM), as well as 5S. Lean manufacturing emphasizes reducing non-value-added activities like inspection, rework and waiting.
Lean manufacturing is a way for companies to achieve their goals faster, improve product quality, and lower costs. Lean manufacturing is considered one of the most effective ways to manage the entire value chain, including suppliers, customers, distributors, retailers, and employees. Lean manufacturing is widely practiced in many industries around the world. Toyota's philosophy is the foundation of its success in automotives, electronics and appliances, healthcare, chemical engineers, aerospace, paper and food, among other industries.
Five principles are the basis of lean manufacturing:
-
Define Value- Identify the added value your company brings to society. What makes you stand out from your competitors?
-
Reduce waste - Get rid of any activity that does not add value to the supply chain.
-
Create Flow - Ensure work moves smoothly through the process without interruption.
-
Standardize and simplify - Make your processes as consistent as possible.
-
Build Relationships- Develop personal relationships with both internal as well as external stakeholders.
Lean manufacturing is not a new concept, but it has been gaining popularity over the last few years due to a renewed interest in the economy following the global financial crisis of 2008. Many businesses are now using lean manufacturing to improve their competitiveness. In fact, some economists believe that lean manufacturing will be an important factor in economic recovery.
Lean manufacturing, which has many benefits, is now a standard practice in the automotive industry. These include improved customer satisfaction, reduced inventory levels, lower operating costs, increased productivity, and better overall safety.
It can be applied to any aspect of an organisation. It is especially useful for the production aspect of an organization, as it ensures that every step in the value chain is efficient and effective.
There are three types principally of lean manufacturing:
-
Just-in Time Manufacturing, (JIT): This kind of lean manufacturing is also commonly known as "pull-systems." JIT refers to a system in which components are assembled at the point of use instead of being produced ahead of time. This approach is designed to reduce lead times and increase the availability of components. It also reduces inventory.
-
Zero Defects Manufacturing, (ZDM): ZDM is focused on ensuring that no defective products leave the manufacturing facility. It is better to repair a part than have it removed from the production line if it needs to be fixed. This is true even for finished products that only require minor repairs prior to shipping.
-
Continuous Improvement (CI): CI aims to improve the efficiency of operations by continuously identifying problems and making changes in order to eliminate or minimize waste. Continuous Improvement involves continuous improvement of processes.