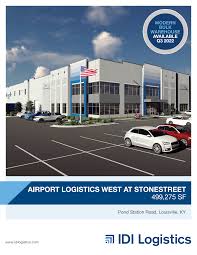
Six-Sigma and Lean both offer complementary methods for improving processes. Both of these approaches use the same tools to solve problems, but each one has its own strengths and weaknesses. Six-Sigma refers to a statistical control technique. Lean, on the other hand, starts with the assumption that a product should add value to its customers, not just make it. Lean is about reducing waste and improving the quality of products as they are being made.
PDCA problem solving
While there are some differences between DMAIC solution solving and PDCA problem solving, they are both based on DMAIC. The PDCA cycle is more complex and requires more analysis. PDCA isn't as efficient for solving urgent issues like DMAIC. This approach requires a problem-solver who has technical skills. Six Sigma is looking for a problem-solving partner who is certified as a Six Sigma green belt practitioner.
Six Sigma uses a cycle introduced by W. Edwards Deming in the 1950s to solve problems. Its creators intended to use it in conjunction with continuous improvement methods to help rebuild Japan's industries. Real data must be collected and a clear mission statement must created in the P (Plan). After the PDCA phase, the team must agree on a solution.
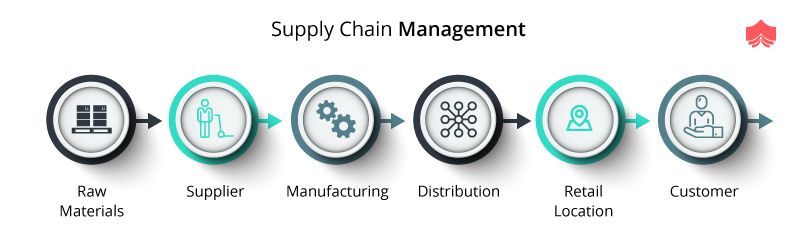
Process maps
There is one key difference between Six Sigma process maps and Lean. It's how each method describes the processes. Both focus on the details of a process, but each methodology will be more focused on certain aspects. For example, Lean involves mapping actual processes instead of standard operating procedures. Consider major decisions and approval sources when creating process maps. Include areas where you use multiple methods and factors that may obstruct members. Make sure you match the roles and look at the process flow.
A process map should have steps, symbols and arrows that show the flow of a particular process. To ensure accuracy, each process should be reviewed and approved by multiple people. The date the process map was created should be included, along with contact information for anyone who has questions. Process maps can be a great way to improve any process. They may also be complex.
Analyse cause-effect
Six Sigma and lean project management techniques include statistical analysis and stochastic optimizing. The Cause and Effect Matrix is a way to link the steps in a process with their outputs and inputs. The customer requirements are listed by importance and then inputs and outputs are ranked according their effect on the outcome. It is important to determine the ranking of key process input variables.
Each technique offers a different set of benefits. Lean Six Sigma uses a process improvement methodology that is based on Frederick Winslow Taylor's Principles of Scientific Management. Taylor envisioned business processes as interlocking processes and workflows. In addition to eliminating variation, he recommended reducing waste. Six-Sigma, lean and lean can be used in conjunction to reduce waste.
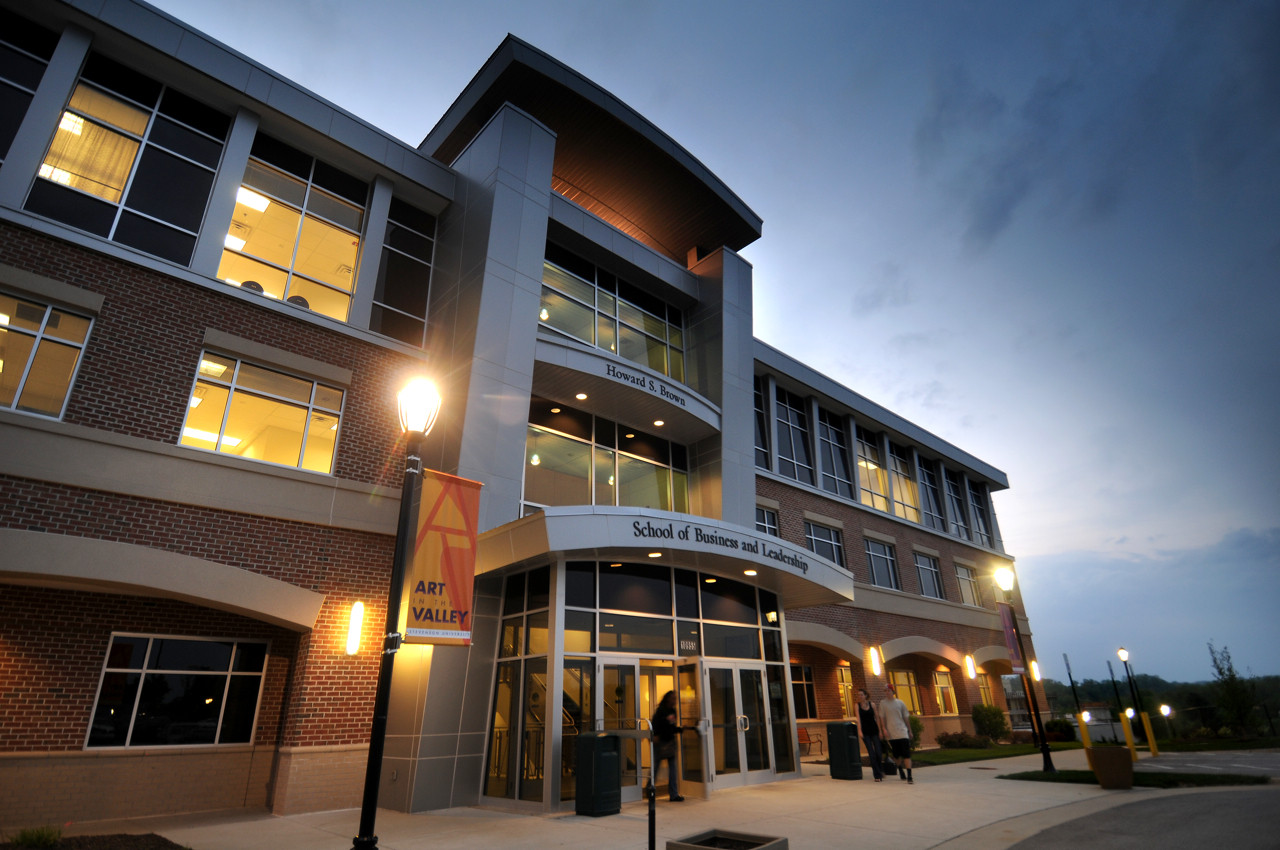
Eliminating variation
Variation is a natural part of any manufacturing process. This variability can create uncertainty in the result. Professional results require consistency. Six Sigma and Lean manufacturing methods strive to eliminate variation. A certain amount of variation is okay, but excessive variation can cause costly repairs, rework and even business consequences. The best way to manage variation is to identify the root cause.
Look for variations at decision points first. Process maps use diamonds to represent decision points. Six Sigma teams can start by identifying decision points and start eliminating variations there. This information comes from the Six Sigma owner. The Six Sigma team will not be able to focus if the process owner does not follow a standard procedure. This is why a Six Sigma team must have the technical capabilities to adjust the process map.
FAQ
How can manufacturing prevent production bottlenecks?
The key to avoiding bottlenecks in production is to keep all processes running smoothly throughout the entire production cycle, from the time you receive an order until the time when the product ships.
This includes planning for capacity requirements as well as quality control measures.
Continuous improvement techniques like Six Sigma are the best way to achieve this.
Six Sigma is a management method that helps to improve quality and reduce waste.
It's all about eliminating variation and creating consistency in work.
What is the job of a production plan?
A production planner makes sure all project elements are delivered on schedule, within budget, as well as within the agreed scope. They make sure that the product and services meet client expectations.
What are the products of logistics?
Logistics refers to all activities that involve moving goods from A to B.
They encompass all aspects transport, including packaging and loading, transporting, storage, unloading.
Logisticians make sure that the right product arrives at the right place at the correct time and in safe conditions. They help companies manage their supply chain efficiency by providing information on demand forecasts, stock levels, production schedules, and availability of raw materials.
They keep track and monitor the transit of shipments, maintain quality standards, order replenishment and inventories, coordinate with suppliers, vendors, and provide support for sales and marketing.
What is the difference between a production planner and a project manager?
The main difference between a production planner and a project manager is that a project manager is usually the person who plans and organizes the entire project, whereas a production planner is mainly involved in the planning stage of the project.
What are the 7 Rs of logistics.
The acronym 7R's for Logistics stands to represent the seven basic principles in logistics management. It was developed by International Association of Business Logisticians (IABL), and published as part of their "Seven Principles of Logistics Management Series" in 2004.
The acronym consists of the following letters:
-
Responsible – ensure that all actions are legal and don't cause harm to anyone else.
-
Reliable - You can have confidence that you will fulfill your promises.
-
It is reasonable to use resources efficiently and not waste them.
-
Realistic – Consider all aspects, including cost-effectiveness as well as environmental impact.
-
Respectful – Treat others fairly and equitably.
-
Responsive - Look for ways to save time and increase productivity.
-
Recognizable is a company that provides customers with value-added solutions.
What are the responsibilities for a manufacturing manager
Manufacturing managers must ensure that manufacturing processes are efficient, effective, and cost-effective. They should be aware of any issues within the company and respond accordingly.
They should also know how to communicate with other departments such as sales and marketing.
They must also keep up-to-date with the latest trends in their field and be able use this information to improve productivity and efficiency.
Statistics
- According to a Statista study, U.S. businesses spent $1.63 trillion on logistics in 2019, moving goods from origin to end user through various supply chain network segments. (netsuite.com)
- (2:04) MTO is a production technique wherein products are customized according to customer specifications, and production only starts after an order is received. (oracle.com)
- In 2021, an estimated 12.1 million Americans work in the manufacturing sector.6 (investopedia.com)
- Job #1 is delivering the ordered product according to specifications: color, size, brand, and quantity. (netsuite.com)
- It's estimated that 10.8% of the U.S. GDP in 2020 was contributed to manufacturing. (investopedia.com)
External Links
How To
How to use the Just-In Time Method in Production
Just-in-time (JIT) is a method that is used to reduce costs and maximize efficiency in business processes. It's a way to ensure that you get the right resources at just the right time. This means that you only pay for what you actually use. Frederick Taylor, a 1900s foreman, first coined the term. After observing how workers were paid overtime for late work, he realized that overtime was a common practice. He decided that workers would be more productive if they had enough time to complete their work before they started to work.
The idea behind JIT is that you should plan ahead and have everything ready so you don't waste money. You should also look at the entire project from start to finish and make sure that you have sufficient resources available to deal with any problems that arise during the course of your project. If you expect problems to arise, you will be able to provide the necessary equipment and personnel to address them. This will ensure that you don't spend more money on things that aren't necessary.
There are different types of JIT methods:
-
Demand-driven: This type of JIT allows you to order the parts/materials required for your project on a regular basis. This will allow you to track how much material you have left over after using it. This will allow to you estimate the time it will take for more to be produced.
-
Inventory-based: This is a type where you stock the materials required for your projects in advance. This allows you to forecast how much you will sell.
-
Project-driven: This approach involves setting aside sufficient funds to cover your project's costs. Knowing how much money you have available will help you purchase the correct amount of materials.
-
Resource-based JIT: This is the most popular form of JIT. You allocate resources based on the demand. If you have many orders, you will assign more people to manage them. If you don’t have many orders you will assign less people to the work.
-
Cost-based: This is a similar approach to resource-based but you are not only concerned with how many people you have, but also how much each one costs.
-
Price-based: This is similar to cost-based but instead of looking at individual workers' salaries, you look at the total company price.
-
Material-based is an alternative to cost-based. Instead of looking at the total cost in the company, this method focuses on the average amount of raw materials that you consume.
-
Time-based JIT: A variation on resource-based JIT. Instead of focusing solely on the amount each employee costs, focus on how long it takes for the project to be completed.
-
Quality-based JIT: This is another variation of resource based JIT. Instead of worrying about the costs of each employee or how long it takes for something to be made, you should think about how quality your product is.
-
Value-based JIT: One of the most recent forms of JIT. This is where you don't care about how the products perform or whether they meet customers' expectations. Instead, you focus on the added value that you provide to your market.
-
Stock-based: This is an inventory-based method that focuses on the actual number of items being produced at any given time. It's used when you want to maximize production while minimizing inventory.
-
Just-intime planning (JIT), is a combination JIT/sales chain management. It refers to the process of scheduling the delivery of components as soon as they are ordered. It reduces lead times and improves throughput.