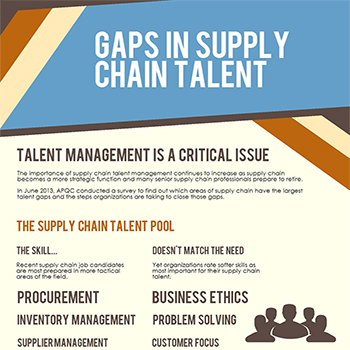
The five s's are the key to lean manufacturing. They are Standardize. Straighten. Shine. and Sustain. These are the steps to follow. You need to train your frontline personnel and team leaders in order to make the most of your lean transformation.
Standardize
Clean and organize your workspace is the first step in the 5S process. This can be a one-time effort, but by standardizing the process, you can turn it into a routine. To ensure a consistent approach to 5S tasks, you can use visual cues, checklist templates, and checklists.
These five s’s of lean can help improve the productivity and efficiency of your workplace. This will help your staff be more organized and perform their tasks in a more efficient manner. By organizing and cleaning up your workspace, you can improve efficiency. These five s’s are helpful for improving safety in the workplace. A well-organized workspace will help avoid accidents, reduce mistakes, and increase the likelihood of productive work.
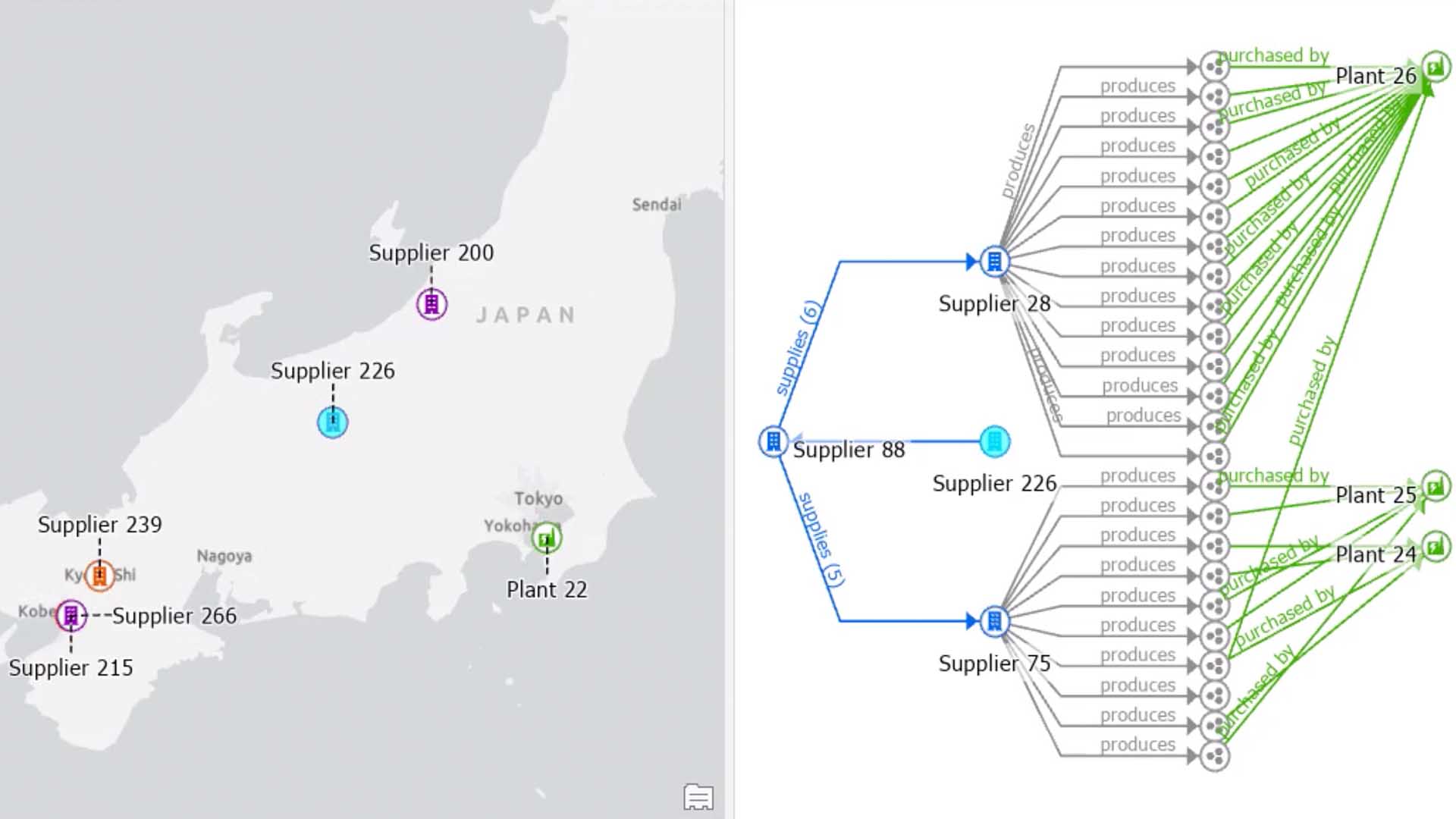
Straighten
Your 5 s's can be done easily. Companies can improve their business processes by applying lean principles in a systematic way. Workers will be able find the parts they need faster if the components are organized in an assembly plant. This will reduce time spent searching for missing parts and increase safety and efficiency in the company's workflow.
This will allow you to reduce the number items in each area. It will also help you save money on consumables. This will allow you to reduce your office supply costs. Straightening work cells can not only help you save money, but it will also improve your production processes and increase quality, safety, standard work, and efficiency.
Shine
Shine is a step that inspects the workspace and points out potential problems. By examining equipment and tools, Shine helps to improve flow and reduce waste. Shine is an aid in the maintenance of workspaces and allows workers to identify problems before they impact production. It helps increase output by standardizing the layout of a workspace.
Shine is one tool used in lean manufacturing. This technique is designed to automate and streamline work processes, reduce waste, and increase efficiency. It can also be used in manufacturing. The 5S principles are applied across businesses. It allows companies to reduce inventory, work-in process, and supply stock.
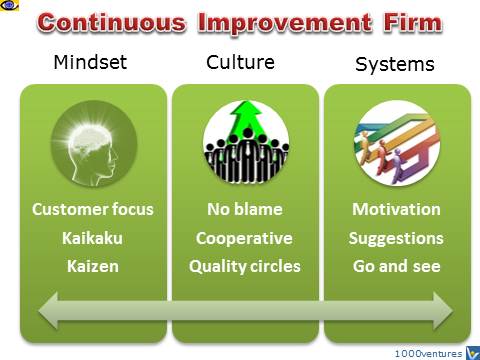
Sustain
To sustain the 5 s's, a facility must be re-introduced to a standard system. This process is intended to be ongoing and should be repeated to ensure that the facility is functioning at its best. This is why employees need to be trained in 5S auditing.
The 5S method emphasizes reducing waste, increasing productivity, and maintaining an orderly work environment. The five principles of Toyota Production System are applied to it. It's a system that organizes workplaces. It was developed by Hiroyuki Hirano in post-war Japan as a means to improve efficiency in manufacturing facilities.
FAQ
What do you mean by warehouse?
A warehouse is a place where goods are stored until they are sold. It can be an outdoor or indoor area. In some cases, it may be a combination of both.
What can I do to learn more about manufacturing?
Experience is the best way for you to learn about manufacturing. You can also read educational videos or take classes if this isn't possible.
What skills do production planners need?
Production planners must be flexible, organized, and able handle multiple tasks. It is also important to be able communicate with colleagues and clients.
What is manufacturing and logistics?
Manufacturing refers to the process of making goods using raw materials and machines. Logistics manages all aspects of the supply chain, including procurement, production planning and distribution, inventory control, transportation, customer service, and transport. Manufacturing and logistics are often considered together as a broader term that encompasses both the process of creating products and delivering them to customers.
What is the responsibility for a logistics manager
A logistics manager makes sure that all goods are delivered on-time and in good condition. This is achieved by using their knowledge and experience with the products of the company. He/she should make sure that enough stock is on hand to meet the demands.
How can manufacturing excess production be decreased?
In order to reduce excess production, you need to develop better inventory management methods. This would decrease the time that is spent on inefficient activities like purchasing, storing, or maintaining excess stock. By doing this, we could free up resources for other productive tasks.
One way to do this is to adopt a Kanban system. A Kanbanboard is a visual tool that allows you to keep track of the work being done. In a Kanban system, work items move through a sequence of states until they reach their final destination. Each state is assigned a different priority.
When work is completed, it can be transferred to the next stage. It is possible to keep a task in the beginning stages until it gets to the end.
This allows work to move forward and ensures that no work is missed. With a Kanban board, managers can see exactly how much work is being done at any given moment. This data allows them adjust their workflow based upon real-time data.
Another way to control inventory levels is to implement lean manufacturing. Lean manufacturing works to eliminate waste throughout every stage of the production chain. Any product that isn't adding value can be considered waste. There are several types of waste that you might encounter:
-
Overproduction
-
Inventory
-
Unnecessary packaging
-
Material surplus
Manufacturers can reduce their costs and improve their efficiency by using these ideas.
Statistics
- [54][55] These are the top 50 countries by the total value of manufacturing output in US dollars for its noted year according to World Bank.[56] (en.wikipedia.org)
- Job #1 is delivering the ordered product according to specifications: color, size, brand, and quantity. (netsuite.com)
- You can multiply the result by 100 to get the total percent of monthly overhead. (investopedia.com)
- Many factories witnessed a 30% increase in output due to the shift to electric motors. (en.wikipedia.org)
- In 2021, an estimated 12.1 million Americans work in the manufacturing sector.6 (investopedia.com)
External Links
How To
Six Sigma in Manufacturing:
Six Sigma refers to "the application and control of statistical processes (SPC) techniques in order to achieve continuous improvement." It was developed by Motorola's Quality Improvement Department at their plant in Tokyo, Japan, in 1986. Six Sigma's main goal is to improve process quality by standardizing processes and eliminating defects. Since there are no perfect products, or services, this approach has been adopted by many companies over the years. Six Sigma seeks to reduce variation between the mean production value. You can calculate the percentage of deviation from the norm by taking a sample of your product and comparing it to the average. If you notice a large deviation, then it is time to fix it.
Understanding how your business' variability is a key step towards Six Sigma implementation is the first. Once you've understood that, you'll want to identify sources of variation. These variations can also be classified as random or systematic. Random variations are caused by human errors. Systematic variations can be caused by outside factors. Random variations would include, for example, the failure of some widgets to fall from the assembly line. But if you notice that every widget you make falls apart at the exact same place each time, this would indicate that there is a problem.
Once you've identified the problem areas you need to find solutions. The solution could involve changing how you do things, or redesigning your entire process. After implementing the new changes, you should test them again to see if they worked. If they don't work you need to rework them and come up a better plan.