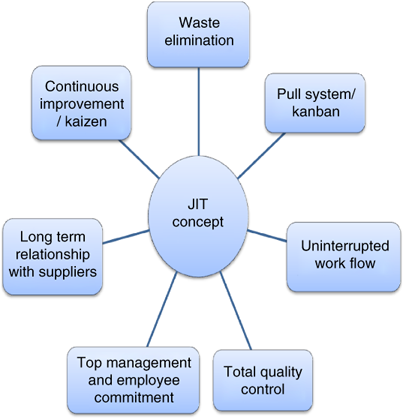
A good media supply chain workflow is crucial. Companies need to invest in new technology in order to make sure their content is delivered efficiently. Consumers are becoming more tech-savvy. It is possible to ensure your media assets are used in the most efficient way by using a cloud-based platform. You can also use it to facilitate processes and gain insight into your company.
To get the most from your media supply chain workflow you must understand all components. For example, the workflow may include quality control to ensure that your media files are in the right format, audio mapping, and codec. This is essential to ensure the content is delivered correctly and preserved. Having a good metadata framework also helps you understand what content is being delivered, which can help you find content faster.
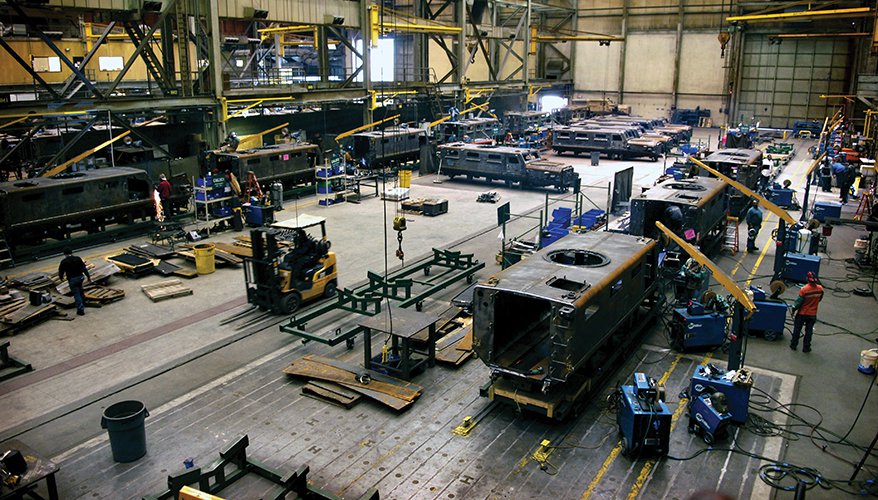
As part of your media supply chain workflow, you may receive content from other companies or third parties. The files might arrive in different formats, which can create challenges. Files may also need to be processed before you can use them. This might involve changing the format or transcoding large master files into smaller files. This can have a negative impact on your business' continuity and be very costly.
The media supply chain workflows have become more complex than they were in the past. It is long past the days of inserting tape in a machine. Streaming and video editing technologies have transformed the production of content. These technologies allow you to create multiple versions of the same piece of content. This ensures that you have the best quality. This can reduce your costs while delivering the highest quality content.
To get the best out of your media supply chain workflow you must have an expert understanding of the processes. Knowledge of client and server operating system, networking, and media terminology are essential. Experience with cloud deployments is also required. If you aren't sure how to do that, it is a good idea to speak with an IT Analyst who is skilled in these areas.
Video engineers work closely together with client teams to develop a media supply-chain workflow. They are responsible of improving functionality, collaborating and delivering media to users. They are also responsible for developing requirements for new features.
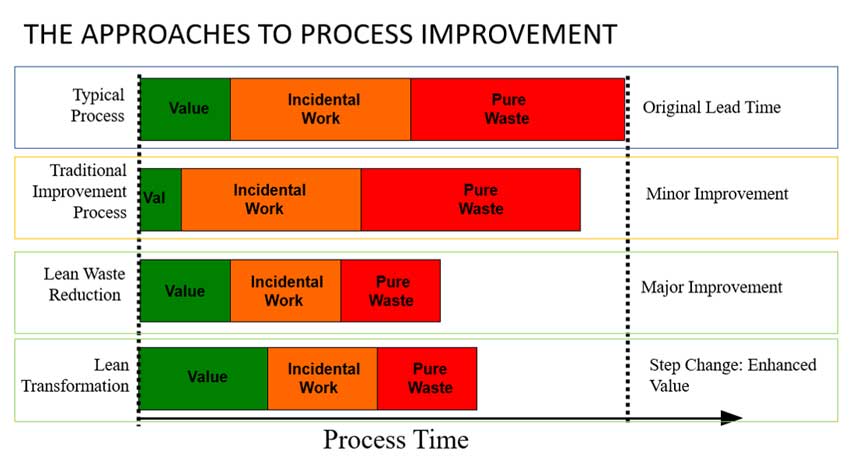
Paramount Global Media Supply Chain Platforms Operations workflows are managed by the Director of Product. They will work closely with colleagues and customers to devise and implement Paramount's solutions. They will also review product requirements and provide feedback on a regular basis. They will also manage product development cycles that use Agile methodology. They will also communicate product requirements to development teams and oversee the translation of these requirements into the product.
FAQ
What does manufacturing mean?
Manufacturing Industries refers to businesses that manufacture products. Consumers are those who purchase these products. These companies employ many processes to achieve this purpose, such as production and distribution, retailing, management and so on. They create goods from raw materials, using machines and various other equipment. This includes all types of manufactured goods, including food items, clothing, building supplies, furniture, toys, electronics, tools, machinery, vehicles, pharmaceuticals, medical devices, chemicals, and many others.
Is automation necessary in manufacturing?
Automating is not just important for manufacturers, but also for service providers. It enables them to provide services faster and more efficiently. In addition, it helps them reduce costs by reducing human errors and improving productivity.
How can excess manufacturing production be reduced?
Better inventory management is key to reducing excess production. This would reduce the time spent on unproductive activities like purchasing, storing and maintaining excess stock. This would allow us to use our resources for more productive tasks.
A Kanban system is one way to achieve this. A Kanban board, a visual display to show the progress of work, is called a Kanban board. Work items are moved through various states to reach their destination in a Kanban system. Each state represents a different priority level.
To illustrate, work can move from one stage or another when it is complete enough for it to be moved to a new stage. It is possible to keep a task in the beginning stages until it gets to the end.
This keeps work moving and ensures no work is lost. Managers can monitor the work being done by Kanban boards to see what is happening at any given time. This information allows managers to adjust their workflow based off real-time data.
Lean manufacturing, another method to control inventory levels, is also an option. Lean manufacturing seeks to eliminate waste from every step of the production cycle. Any product that isn't adding value can be considered waste. The following are examples of common waste types:
-
Overproduction
-
Inventory
-
Unnecessary packaging
-
Exceed materials
Manufacturers can reduce their costs and improve their efficiency by using these ideas.
Statistics
- You can multiply the result by 100 to get the total percent of monthly overhead. (investopedia.com)
- In 2021, an estimated 12.1 million Americans work in the manufacturing sector.6 (investopedia.com)
- (2:04) MTO is a production technique wherein products are customized according to customer specifications, and production only starts after an order is received. (oracle.com)
- It's estimated that 10.8% of the U.S. GDP in 2020 was contributed to manufacturing. (investopedia.com)
- Job #1 is delivering the ordered product according to specifications: color, size, brand, and quantity. (netsuite.com)
External Links
How To
How to use 5S in Manufacturing to Increase Productivity
5S stands for "Sort", "Set In Order", "Standardize", "Separate" and "Store". Toyota Motor Corporation developed the 5S method in 1954. It assists companies in improving their work environments and achieving higher efficiency.
This method has the basic goal of standardizing production processes to make them repeatable. This means that daily tasks such as cleaning and sorting, storage, packing, labeling, and packaging are possible. These actions allow workers to perform their job more efficiently, knowing what to expect.
Five steps are required to implement 5S: Sort, Set In Order, Standardize. Separate. Each step has a different action and leads to higher efficiency. You can make it easy for people to find things later by sorting them. You arrange items by placing them in an order. Once you have separated your inventory into groups and organized them, you will store these groups in easily accessible containers. Finally, label all containers correctly.
Employees need to reflect on how they do their jobs. Employees should understand why they do the tasks they do, and then decide if there are better ways to accomplish them. They must learn new skills and techniques in order to implement the 5S system.
The 5S method increases efficiency and morale among employees. They are more motivated to achieve higher efficiency levels as they start to see improvement.