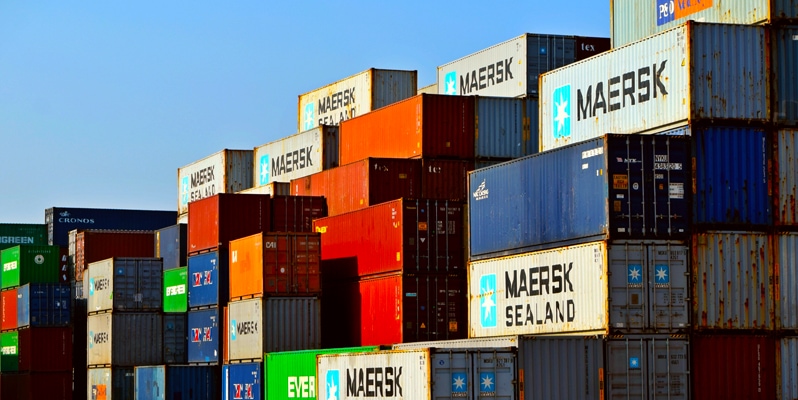
In the industrial manufacturing sector, there is increased global competition as well as a shortage skilled workers. Combined with increased supply chain volatility, the industrial manufacturing industry faces a challenging landscape in the 2020s. The Industrial Products & Services sector requires a comprehensive culture of innovation to ensure optimisation of growth in established markets, while also optimising for growth opportunities in new markets.
According to Deloitte and Manufacturing Institute studies, the US manufacturing workforce is likely to experience the largest skill shortage in recent history. In fact, it is estimated that 2 million unfilled jobs will occur over the next 10 years. The future of the industry is now in the hands of manufacturers. They must decide how to develop their digital capabilities and innovate. Deloitte’s Industrial Manufacturing team can help manufacturers navigate their industry landscape.
As the fourth industrial revolution continues its disruption in the manufacturing sector, the industry must prepare employees for a future that includes networking within the internet of things' as well as digital transformation. The Industrial Manufacturing team is skilled at establishing innovative management models that are grounded industry-specific expertise and deep industry knowledge. The team also offers a variety of digital transformation services to help manufacturers thrive in an era of digital disruption.
The Deloitte analysis is based upon extensive secondary data analysis on labor supply as well as interviews of executives from all sizes of manufacturing organizations. The research also includes economic projections. Findings also emphasize the importance of diverse workforces. In particular, half of respondents said that adaptability to company values was key to their job happiness. Over a third of respondents said that employees need to have a purpose to feel satisfied at their jobs. Furthermore, executives feel that millennials understand the importance of environmental awareness and that Generation Z workers are becoming more involved in climate issues.
Deloitte uses the Oxford Economic Model to predict that manufacturing GDP will increase at a moderate rate, of 1.3 percent, in 2020. The study points out that this growth rate is less than half the rate experienced in recent years. This means that companies will need to rethink their approaches to supply chain assurance. Additionally, companies will need broader management initiatives like increasing operational resilience. In fact, the Deloitte study indicates that manufacturers will likely be making decisions about workplaces and work practices.
In order to prepare for the future, manufacturing companies need to develop pathways for careers and develop an inclusive culture. The ability to increase resilience in operations can help improve manufacturing efficiency, reduce waste and reduce costs. In addition, the combination of digital technologies and lean principles can also help reduce manufacturing variability.
As the US manufacturing industry continues to evolve, Deloitte has released a new report that explores diversity in manufacturing. Deloitte's "Beyond Reskilling" report discusses how diversity is essential to manufacturing's future, and it highlights the benefits of having a diverse workforce.
FAQ
What is meant by manufacturing industries?
Manufacturing Industries refers to businesses that manufacture products. The people who buy these products are called consumers. These companies use various processes such as production, distribution, retailing, management, etc., to fulfill this purpose. They manufacture goods from raw materials using machines and other equipment. This includes all types and varieties of manufactured goods, such as food items, clothings, building supplies, furnitures, toys, electronics tools, machinery vehicles, pharmaceuticals medical devices, chemicals, among others.
How does a production planner differ from a project manager?
The main difference between a production planner and a project manager is that a project manager is usually the person who plans and organizes the entire project, whereas a production planner is mainly involved in the planning stage of the project.
Why is logistics important in manufacturing?
Logistics is an integral part of every business. They help you achieve great results by helping you manage all aspects of product flow, from raw materials to finished goods.
Logistics also play a major role in reducing costs and increasing efficiency.
Do we need to know about Manufacturing Processes before learning about Logistics?
No. No. It is important to know about the manufacturing processes in order to understand how logistics works.
How can we increase manufacturing efficiency?
The first step is to identify the most important factors affecting production time. Then we need to find ways to improve these factors. If you aren't sure where to begin, think about the factors that have the greatest impact on production time. Once you identify them, look for solutions.
Why should you automate your warehouse?
Automation has become increasingly important in modern warehousing. The rise of e-commerce has led to increased demand for faster delivery times and more efficient processes.
Warehouses must be able to quickly adapt to changing demands. In order to do this, they need to invest in technology. The benefits of automating warehouses are numerous. Here are some benefits of investing in automation
-
Increases throughput/productivity
-
Reduces errors
-
Increases accuracy
-
Safety enhancements
-
Eliminates bottlenecks
-
Companies can scale up more easily
-
It makes workers more efficient
-
The warehouse can be viewed from all angles.
-
Enhances customer experience
-
Improves employee satisfaction
-
Minimizes downtime and increases uptime
-
This ensures that quality products are delivered promptly
-
Removes human error
-
Helps ensure compliance with regulations
What is the difference between Production Planning, Scheduling and Production Planning?
Production Planning (PP) is the process of determining what needs to be produced at any given point in time. This is accomplished by forecasting the demand and identifying production resources.
Scheduling involves the assignment of dates and times to tasks in order to complete them within the timeframe.
Statistics
- According to a Statista study, U.S. businesses spent $1.63 trillion on logistics in 2019, moving goods from origin to end user through various supply chain network segments. (netsuite.com)
- [54][55] These are the top 50 countries by the total value of manufacturing output in US dollars for its noted year according to World Bank.[56] (en.wikipedia.org)
- According to the United Nations Industrial Development Organization (UNIDO), China is the top manufacturer worldwide by 2019 output, producing 28.7% of the total global manufacturing output, followed by the United States, Japan, Germany, and India.[52][53] (en.wikipedia.org)
- You can multiply the result by 100 to get the total percent of monthly overhead. (investopedia.com)
- (2:04) MTO is a production technique wherein products are customized according to customer specifications, and production only starts after an order is received. (oracle.com)
External Links
How To
Six Sigma and Manufacturing
Six Sigma is "the application statistical process control (SPC), techniques for continuous improvement." Motorola's Quality Improvement Department, Tokyo, Japan, developed it in 1986. Six Sigma is a method to improve quality through standardization and elimination of defects. This method has been adopted by many companies in recent years as they believe there are no perfect products or services. Six Sigma seeks to reduce variation between the mean production value. It is possible to measure the performance of your product against an average and find the percentage of time that it differs from the norm. If there is a significant deviation from the norm, you will know that something needs to change.
Understanding the nature of variability in your business is the first step to Six Sigma. Once you've understood that, you'll want to identify sources of variation. It is important to identify whether the variations are random or systemic. Random variations are caused when people make mistakes. While systematic variations are caused outside of the process, they can occur. For example, if you're making widgets, and some of them fall off the assembly line, those would be considered random variations. It would be considered a systematic problem if every widget that you build falls apart at the same location each time.
Once you identify the problem areas, it is time to create solutions. This could mean changing your approach or redesigning the entire process. To verify that the changes have worked, you need to test them again. If they didn't work, then you'll need to go back to the drawing board and come up with another plan.