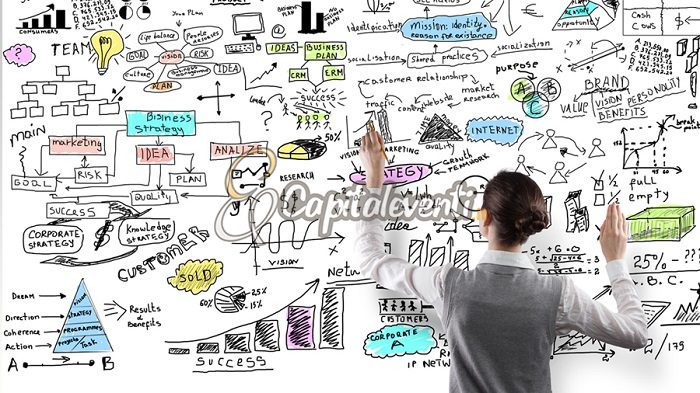
Industrial Engineering Managers are an integral part of any team, regardless of whether it is for a new or regular project. They are responsible for directing staff and improving production output. This includes overseeing and coordinating the layout and design for the factory floor as well the implementation of processes. Aside from their technical expertise, they can help companies develop new products or processes.
Industrial Engineering Managers are responsible for developing and maintaining efficient manufacturing processes. This requires the knowledge of the latest trends in automation and robotics. They also need to monitor and maintain industrial procedures and ensure compliance to health and safety standards. They supervise the usage of raw materials, consumables, and other industrial processes. They also conduct studies to improve workflow and space usage. The manager oversees the implementation of all work projects, including cycle time reduction, product cost reduction, and process improvement. They are also responsible for managing preventative maintenance plans.
In collaboration with other teams, the manager develops new processes, streamlines operations, and improves efficiency. The manager also supervises the renovation and installation of equipment. Managers communicate technical information to non-technical parties as part of the project management process. Additionally, the manager ensures that resources are available to teams and makes site visits at suppliers' facilities. He or she represents the team members and ensures compliance with quality guidelines.
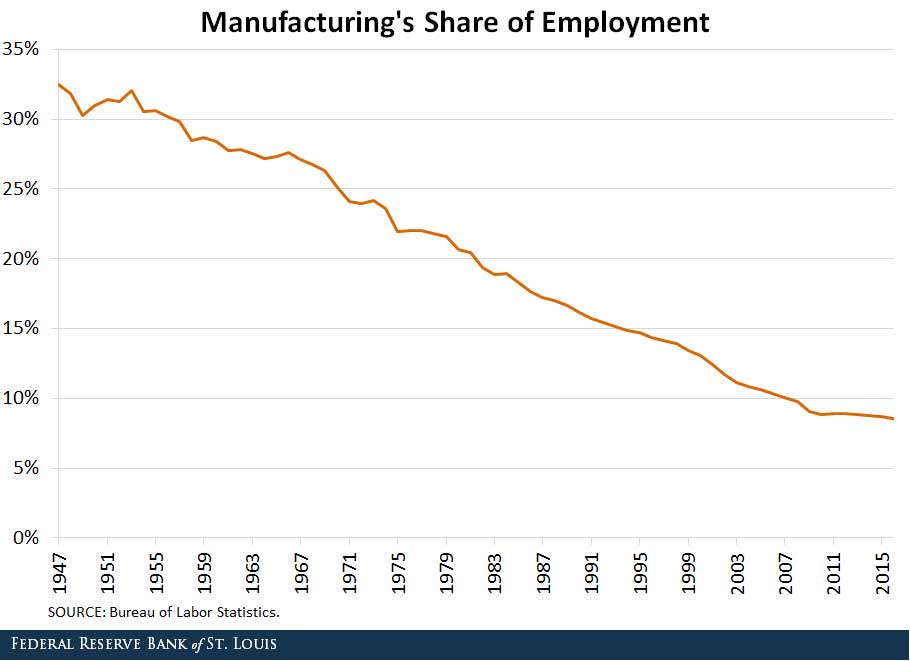
Industrial engineering managers must be motivated, creative, and able solve problems. They must be able walk and climb for 8 to 12 hours each day and can work in extreme heat and cold. They must also be able communicate with all levels of employees.
Industrial Engineering Managers must have a degree in engineering or a related field. They must also possess at least five year's experience in the industry. Some employers prefer candidates with a postgraduate degree. These candidates may also require specific skills such as project management and logistics.
Managers in Industrial Engineering oversee the development and design of new products and processes. They have a strong background for problem-solving and quality improvements. They enjoy working in a team. A manager can be most successful if he or she can encourage employees' growth.
Industrial Engineers are highly skilled at streamlining operations and cutting costs. They have a good understanding of manufacturing processes and are able to meet deadlines. They also have experience with recruiting, human resources, logistics, and vendor / supplier relations. They are proficient in setting goals, administering procedures, and creating budgets. They are also able to prepare strategies to increase the efficiency of engineering projects.
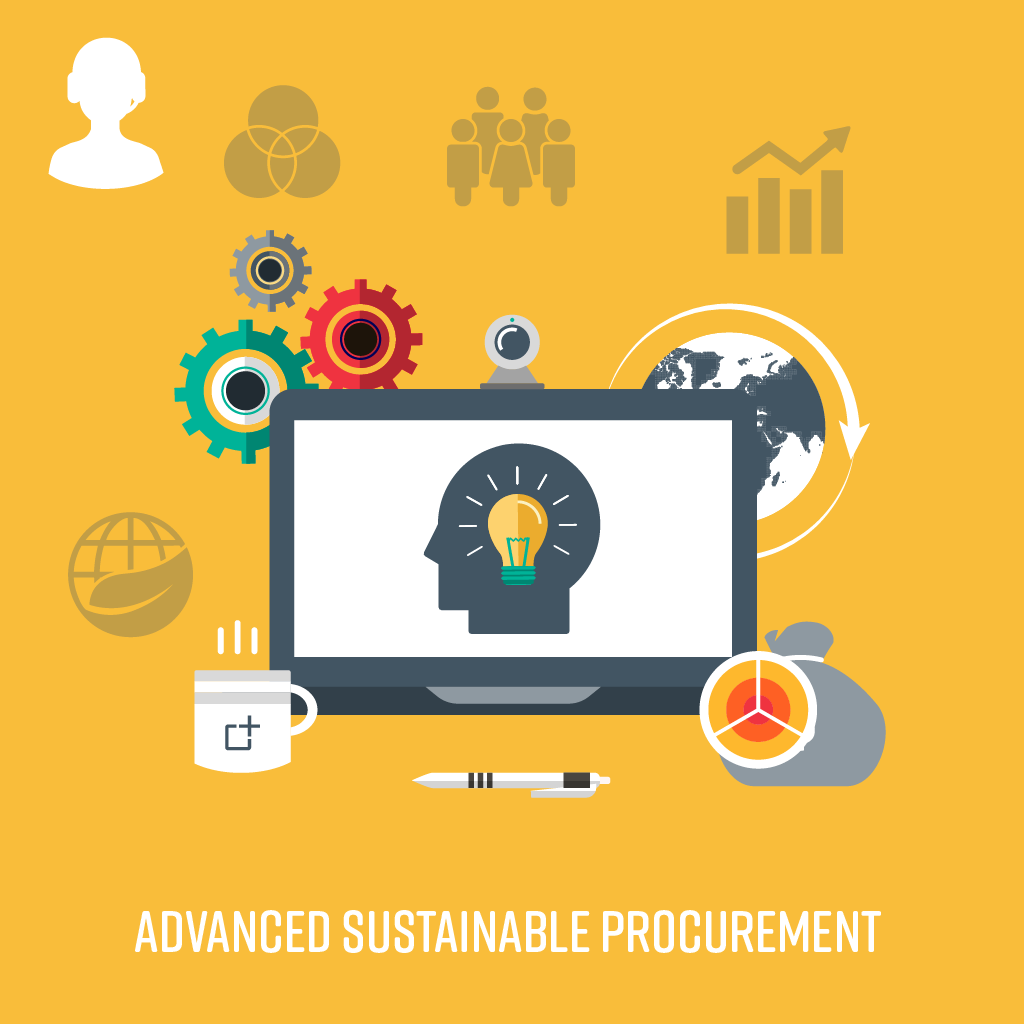
The Industrial Engineering Manager may be responsible to oversee the design and implementation new manufacturing processes or equipment. They will need to develop plans and operate methods that conform to existing standards and guidelines. They will also be responsible for overseeing waste elimination plans. They are also responsible to assess the labor productivity in the factory.
Industrial Engineering Managers can help improve productivity and develop new products. They also have the expertise to manage human resources. They can also help develop and improve the efficiency of existing processes.
FAQ
What types of jobs can you find in logistics
There are many jobs available in logistics. Some of them are:
-
Warehouse workers: They load and unload trucks, pallets, and other cargo.
-
Transportation drivers – These drivers drive trucks and wagons to transport goods and pick up the goods.
-
Freight handlers are people who sort and pack freight into warehouses.
-
Inventory managers – These people oversee inventory at warehouses.
-
Sales reps are people who sell products to customers.
-
Logistics coordinators - They plan and organize logistics operations.
-
Purchasing agents - They buy goods and services that are necessary for company operations.
-
Customer service representatives - Answer calls and email from customers.
-
Ship clerks - They issue bills and process shipping orders.
-
Order fillers: They fill orders based off what has been ordered and shipped.
-
Quality control inspectors are responsible for inspecting incoming and outgoing products looking for defects.
-
Others – There are many other types available in logistics. They include transport supervisors, cargo specialists and others.
What does it take for a logistics enterprise to succeed?
A successful logistics business requires a lot more than just knowledge. You must have good communication skills to interact effectively with your clients and suppliers. You must be able analyze data and draw out conclusions. You must be able manage stress and pressure under pressure. You must be creative and innovative to develop new ideas to improve efficiency. You need to have strong leadership qualities to motivate team members and direct them towards achieving organizational goals.
It is important to be organized and efficient in order to meet tight deadlines.
What makes a production planner different from a project manger?
The main difference between a production planner and a project manager is that a project manager is usually the person who plans and organizes the entire project, whereas a production planner is mainly involved in the planning stage of the project.
How can manufacturing reduce production bottlenecks?
The key to avoiding bottlenecks in production is to keep all processes running smoothly throughout the entire production cycle, from the time you receive an order until the time when the product ships.
This includes planning for both capacity requirements and quality control measures.
Continuous improvement techniques such Six Sigma can help you achieve this.
Six Sigma is a management system used to improve quality and reduce waste in every aspect of your organization.
It focuses on eliminating variation and creating consistency in your work.
What is production planning?
Production Planning refers to the development of a plan for every aspect of production. This document will ensure everything is in order and ready to go when you need it. It should also contain information on achieving the best results on set. This includes shooting schedules, locations, cast lists, crew details, and equipment requirements.
First, you need to plan what you want to film. You may have already chosen the location you want, or there are locations or sets you prefer. Once you've identified the locations and scenes you want to use, you can begin to plan what elements you need for each scene. One example is if you are unsure of the exact model you want but decide that you require a car. In this case, you could start looking up cars online to find out what models are available and then narrow your choices by choosing between different makes and models.
After you've found the perfect car, it's time to start thinking about adding extras. Are you looking for people to sit in the front seats? Maybe you need someone to move around in the back. You may want to change the interior's color from black or white. These questions will help you determine the exact look and feel of your car. You can also think about the type of shots you want to get. Do you want to film close-ups, or wider angles? Perhaps you want to show the engine or the steering wheel? All of these things will help you identify the exact style of car you want to film.
Once you have determined all of the above, you can move on to creating a schedule. A schedule will tell you when you need to start shooting and when you need to finish. A schedule for each day will detail when you should arrive at the location and when you need leave. It will help everyone know exactly what they have to do and when. You can also make sure to book extra staff in advance if you have to hire them. You don't want to hire someone who won't show up because he didn't know.
When creating your schedule, you will also need to consider the number of days you need to film. Some projects take only a few days while others can last several weeks. When creating your schedule, be aware of whether you need more shots per day. Multiple takes at the same place will result in higher costs and longer completion times. It is better to be cautious and take fewer shots than you risk losing money if you are not sure if multiple takes are necessary.
Budgeting is another important aspect of production planning. As it will allow you and your team to work within your financial means, setting a realistic budget is crucial. It is possible to reduce the budget at any time if you experience unexpected problems. But, don't underestimate how much money you'll spend. You will end up spending less money if you underestimate the cost of something.
Production planning is a complicated process. But once you understand how everything works together, it becomes much easier to plan future project.
What does manufacturing mean?
Manufacturing Industries are companies that manufacture products. Consumers are those who purchase these products. To accomplish this goal, these companies employ a range of processes including distribution, sales, management, and production. They make goods from raw materials with machines and other equipment. This includes all types if manufactured goods.
Statistics
- (2:04) MTO is a production technique wherein products are customized according to customer specifications, and production only starts after an order is received. (oracle.com)
- You can multiply the result by 100 to get the total percent of monthly overhead. (investopedia.com)
- Many factories witnessed a 30% increase in output due to the shift to electric motors. (en.wikipedia.org)
- It's estimated that 10.8% of the U.S. GDP in 2020 was contributed to manufacturing. (investopedia.com)
- [54][55] These are the top 50 countries by the total value of manufacturing output in US dollars for its noted year according to World Bank.[56] (en.wikipedia.org)
External Links
How To
How to Use 5S for Increasing Productivity in Manufacturing
5S stands in for "Sort", the "Set In Order", "Standardize", or "Separate". The 5S methodology was developed at Toyota Motor Corporation in 1954. It improves the work environment and helps companies to achieve greater efficiency.
This method has the basic goal of standardizing production processes to make them repeatable. It means tasks like cleaning, sorting or packing, labeling, and storing are done every day. This knowledge allows workers to be more efficient in their work because they are aware of what to expect.
Implementing 5S involves five steps: Sort, Set in Order, Standardize Separate, Store, and Each step has a different action and leads to higher efficiency. For example, when you sort things, you make them easy to find later. When you set items in an order, you put items together. Then, after you separate your inventory into groups, you store those groups in containers that are easy to access. Finally, when you label your containers, you ensure everything is labeled correctly.
Employees must be able to critically examine their work practices. Employees must be able to see why they do what they do and find a way to achieve them without having to rely on their old methods. They will need to develop new skills and techniques in order for the 5S system to be implemented.
In addition to increasing efficiency, the 5S method also improves morale and teamwork among employees. As they begin to see improvements, they feel motivated to continue working towards the goal of achieving higher levels of efficiency.