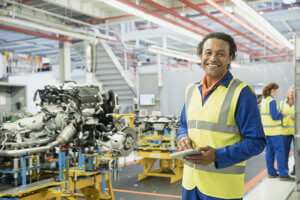
Lean can be used as an acronym in the manufacturing world to describe certain principles and techniques. It can also be a motivational word that encourages improvement in the process.
The Definition of Lean
If an organization wants to improve its efficiency, it might have to eliminate certain activities. They may not add any value to the products or services it offers. This can include unused equipment or idle time.
Lean management is an approach that aims to eliminate all waste from the production process. The process will never end, and it is always being adjusted.
Lean is a concept that focuses on what the customer wants and makes it a priority to provide this value. It does not focus on what the business thinks they need. So, businesses will not waste time or money on products that their customers do not want.
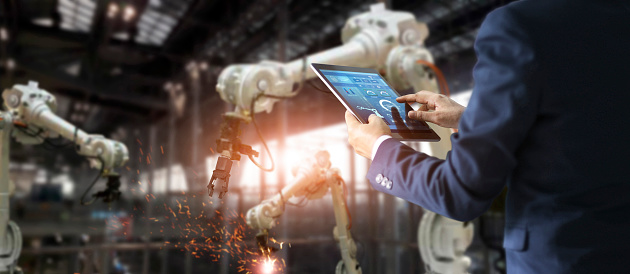
The idea of lean is adaptable to any production method or industry. This is why lean has become so popular across many different industries.
Lean manufacturing has been around for many years. It is a system which focuses delivering the best products in the most efficient way. It is also a great tool for creating efficiencies in the manufacturing process.
Toyoda's definition of lean is based on the elimination of waste in production. This includes wastes such as defects which are not acceptable by the customer.
Toyoda came up with a solution that involved a flow-process, where workers would stop the production line and inspect an item. If necessary, they would remove it. The company was able to optimize each stage of production to reduce defects and increase productivity.
Jidoka can be defined as a system which automatically stops when an abnormality is detected in a production process. Kaizen is a vital part of lean production.
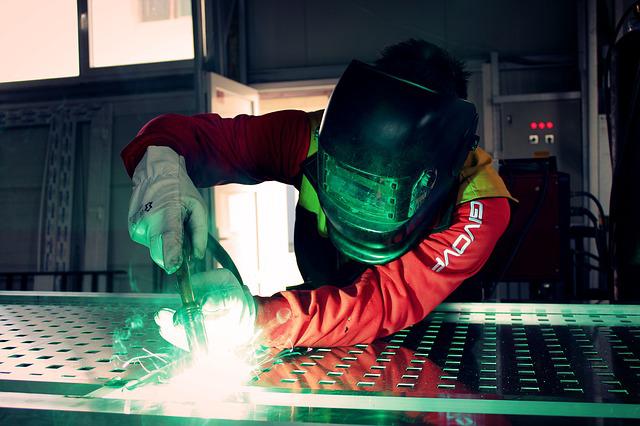
Kaizen involves continuous improvements for any process. This can apply to product production, or any part of the company that requires an update.
A lot of people don't really understand what lean means, but it is a great concept that helps improve the way businesses run. Lean can save companies money and time, while also helping them to build a stronger reputation with their customers.
It is important to remember that lean is not an isolated practice; it's a process that will need to be improved by all levels of a company in order to be successful. This is why it is crucial to involve all employees in the process, so that everyone can contribute their ideas and ensure that everything goes smoothly.
FAQ
How can we improve manufacturing efficiency?
The first step is to identify the most important factors affecting production time. We must then find ways that we can improve these factors. If you don't know where to start, then think about which factor(s) have the biggest impact on production time. Once you've identified them all, find solutions to each one.
What are the four types of manufacturing?
Manufacturing is the process that transforms raw materials into useful products. Manufacturing involves many activities, including designing, building, testing and packaging, shipping, selling, service, and so on.
Why automate your warehouse
Modern warehousing is becoming more automated. With the rise of ecommerce, there is a greater demand for faster delivery times as well as more efficient processes.
Warehouses must be able to quickly adapt to changing demands. Technology is essential for warehouses to be able to adapt quickly to changing needs. Automating warehouses has many benefits. Here are some of the reasons automation is worth your investment:
-
Increases throughput/productivity
-
Reduces errors
-
Improves accuracy
-
Safety enhancements
-
Eliminates bottlenecks
-
Companies can scale more easily
-
Workers are more productive
-
Provides visibility into everything that happens in the warehouse
-
Enhances customer experience
-
Improves employee satisfaction
-
Minimizes downtime and increases uptime
-
You can be sure that high-quality products will arrive on time
-
Human error can be eliminated
-
This helps to ensure compliance with regulations
What is the role of a manager in manufacturing?
A manufacturing manager must ensure that all manufacturing processes are efficient and effective. They should also be aware of any problems within the company and act accordingly.
They should also be able and comfortable communicating with other departments like sales and marketing.
They should be up to date on the latest trends and be able apply this knowledge to increase productivity and efficiency.
Statistics
- Many factories witnessed a 30% increase in output due to the shift to electric motors. (en.wikipedia.org)
- In 2021, an estimated 12.1 million Americans work in the manufacturing sector.6 (investopedia.com)
- According to a Statista study, U.S. businesses spent $1.63 trillion on logistics in 2019, moving goods from origin to end user through various supply chain network segments. (netsuite.com)
- According to the United Nations Industrial Development Organization (UNIDO), China is the top manufacturer worldwide by 2019 output, producing 28.7% of the total global manufacturing output, followed by the United States, Japan, Germany, and India.[52][53] (en.wikipedia.org)
- Job #1 is delivering the ordered product according to specifications: color, size, brand, and quantity. (netsuite.com)
External Links
How To
How to Use the 5S to Increase Productivity In Manufacturing
5S stands in for "Sort", the "Set In Order", "Standardize", or "Separate". Toyota Motor Corporation invented the 5S strategy in 1954. This methodology helps companies improve their work environment to increase efficiency.
This method aims to standardize production processes so that they are repeatable, measurable and predictable. It means tasks like cleaning, sorting or packing, labeling, and storing are done every day. Because workers know what they can expect, this helps them perform their jobs more efficiently.
Implementing 5S involves five steps: Sort, Set in Order, Standardize Separate, Store, and Each step has a different action and leads to higher efficiency. By sorting, for example, you make it easy to find the items later. When you arrange items, you place them together. After you have divided your inventory into groups you can store them in easy-to-reach containers. Labeling your containers will ensure that everything is correctly labeled.
This requires employees to critically evaluate how they work. Employees should understand why they do the tasks they do, and then decide if there are better ways to accomplish them. To implement the 5S system, employees must acquire new skills and techniques.
In addition to increasing efficiency, the 5S method also improves morale and teamwork among employees. They will feel motivated to strive for higher levels of efficiency once they start to see results.